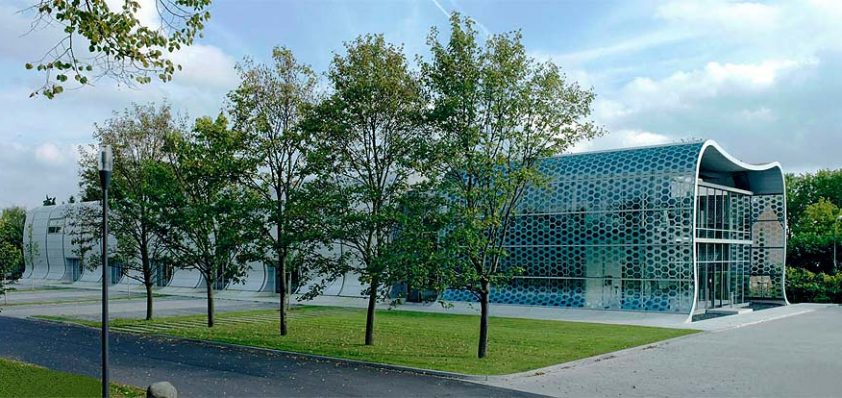
ARCA Regler GmbH: A Century of Innovation in Control Valves for the Process Industry
Not a regular knowledge base
ARCA has achieved continuous growth and a strong reputation since its first patent was filed in 1917.
Today Germany based ARCA Regler GmbH is a globally active developer, manufacturer and marketer of quality control valves. With such a long history ARCA employs an unmatched experience in valve applications and market demands of the process industry. ARCA operates as head office of the ARCA Flow Group, which also includes companies such as ‘FELUWA’ pumps, ‘WEKA’ cryogenic components and ‘von Rohr Armaturen’. The still family owned group of companies continues to deliver benchmark products as well as superior after sales and maintenance services to the process industry worldwide.
Since it was previously featured in European Oil & Gas Magazine, the innovative firm has maintained its focus on research and development to meet the specific needs of its customers, especially finding solutions to unique challenges within the oil and gas industry. Managing director Markus Dönni highlights: “ARCA valves have helped ensure production and process reliability in the industry for many years; we have a wide range of precision engineered control valves available ranging from DN15 (1/2) to DN700 (28 inch) as well as PN16 to PN400 (ANSI 150- 2500) sizes. In addition, we have special purpose valves for all media handled in chemical and petrochemical industry.”
Referring to the most recent invention of ARCA’s ‘Moonshine Trim’ Technical Director Lothar Grutesen gives a detailed example, how ARCA’s products support the specific needs of its customers in the oil and gas industry:
Processes based on the reaction of a process fluid under high pressure and at a high reaction temperature (possibly with the addition of a catalyst), are of major significance in the chemical and petrochemical industry. If these are continuous processes, they are always connected with level and pressure controllers for the reaction vessel and thus also with the associated control valves that transfer the product or the process gas from the reaction vessel to the downstream processes.
A representative example of such processes is the hydrodesulphurisation (or ‘HDS’) in the petrochemical industry, in which mineral oil products are desulphurised by hydrogenation (reaction of the sulphur compounds with hydrogen). HDS processes are absolutely indispensable in refineries due to today’s strict environmental protection regulations, since almost all important mineral fuels such as diesel fuels, fuel oil and also petrol consist exclusively of hydrogenated components.
The feedstock is preheated together with gaseous hydrogen and fed into the reaction vessel. The catalytic reaction takes place at pressures of up to 200 bar and temperatures of up to 370 °C.
Since the downstream processes take place at considerably lower pressures, extremely high demands are placed on the control valves used for the blowdown of the product:
- high pressure ratio up to x = p/p1 = 190 bar/200 bar
- cavitation and partial evaporation of the product.
- corrosion resistance to the H2S and ammonia content resulting from the hydrodesulphurisation.
- resistance to blockages due to solid particles, in particular with respect to the catalyst.
Multi-stage valves are absolutely necessary for this application. Ideally, the trim of a multi-stage valve is designed to maintain same pressure ratio xi at each control stage. This leads to individual rated flow coefficients on each stage, which necessitates greater effort for the design and the processing of the valve trim, but will pay off with regard to the service life and operational safety of the control valve.
In addition to the pure fluidic design of the valve trim, the solid contamination of the process fluid must be considered for HDS applications, i.e. the valve may not ‘clog up’ due to the solids contained in the product.
The maximum size of a spherical particle, which (geometrically regarded) can pass through all the bottlenecks of the valve can be taken as a good measure of the permeability of a valveto solids. Since the 1st stage always is the one with the smallest rated flow coefficients CV, it naturally forms the critical bottleneck of each multi-stage valve.
The cross-section of any flow passage can be estimated from the Bernoulli pressure equation to be approximately 27.8 mm² per rated CV. The optimum shape of a throttle point with regard to the ‘permeability’ to solids is naturally a circular cross-section – an area of 27.8 mm² results in a diameter (and thus also a maximum particle size) of 5.9 mm.
The newly developed MS-design, where a flow channel in the shape of a semi-circle is milled into a multiple-guided plug stem for each stage (fig. 1), ideally implements these requirements in a robust and functionally reliable multi-stage trim.
The respectively used milling bit is defined according to the KVs value of the respective throttle stage, thus optimising the shape of the throttle point when the valve is 100 % open (fig. 2). The actual characteristic curve of the valve, which closely approximates to an equal percentage characteristic, is then created by the CNC controlled milling depth.
Apart from the design and shape of the control stages, the protection of the sealing edges is of particular significance for the lifetime of the valve. The following requirements apply to this area:
The sealing edges of throttle element and seat ring must be specially protected against damage by cavitation and erosion.
With regard to the permeability for solids, the sealing seat itself may not form the bottleneck in the valve.
Both features are achieved by means of overtravel. In the closed position a closed sealing line forms between seat ring and valve plug – the seat leakage rate can be even Class V. The throttle openings of the individual control stages open only after exceeding the overtravel (fig. 3). At this moment, however, the free flow crosssection at the sealing seat is already a multiple of the cross-section of the first throttle stage, means the flow velocity at the sealing seat is that small that damage to the sealing edges is ruled out. As long as the valve overtravel is larger than the maximum particle size of the first control stage, this automatically ensures that the sealing seat does not form the bottleneck for solids.
Lothar completes the explanation of his invention by outlining: “Due to the rather simple geometry of throttle body and seat ring, MS-type valve trims can be manufactured in all materials – even in tungsten carbide or ceramics – thus giving rise to a wide range of uses in all critical relaxation processes”.
Looking to the future, ARCA Regler is preparing to exhibit its technologically refined, safe, reliable and cost-effective solutions to clients and peers at Achema, the world forum for chemical engineering and the process industry, from 15-19 June in Frankfurt, Germany this year. “With our group of companies we will be based in Hall 8.0, booth Number G94, where we will exhibit DN 700 valves and other inventions such as our Moonshine Trim,” concludes Markus.
ARCA Regler GmbH
Services: Control valve solutions