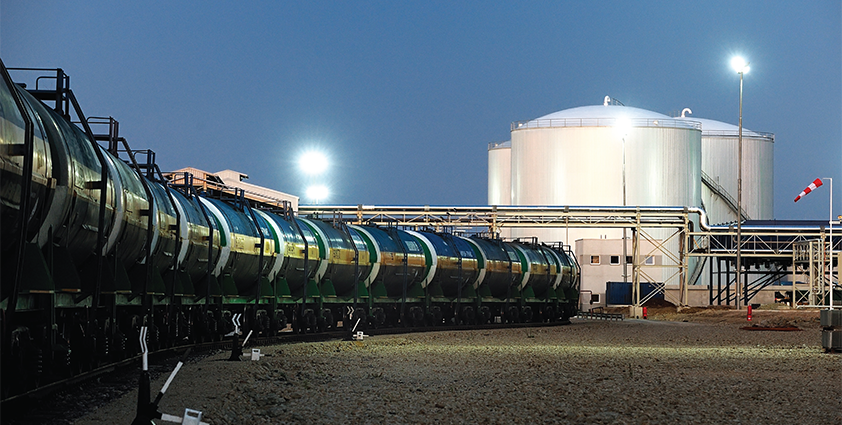
Baltic Chemical Terminal: A Strategic Hub for Liquid Chemical Fertiliser Transshipment in Estonia
Look east
Despite having only been present on the market since 2008, Baltic Chemical Terminal’s (BCT) location in the Port of Sillamäe in Estonia, only 23 km from the Russian border, is of key commercial benefit in the field of liquid chemical fertilisers transportation.
Having successfully achieved all required legal and financial documentation for the project, construction of the terminal began in 2007, withBCT loading its first vessel with 20,000 tonnes of urea ammonium nitrate (UAN) cargo in early 2008. This was followed by its first ammonia shipment of 11,640 tonnes, in the third quarter of 2009. Due to its close proximity to Russia, BCT’s activities are directed at the country’s fertiliser exporters and chemical producers.
In fact there are several favourable aspects to BCT’s location, not least that the Port of Sillamäe is the nearest and deepest port between the Russian Federation and European Union. With a depth of 13 metres it enables the largest vessels capable of entering the Baltic Sea through the Danish Straights to enter the port at any time. Additionally the Port is connected to Russia by rail, which serves to further enhance cargo flow, the port is also a private port, and its motivated and professional team means that fast decision making and fast execution are key to its success.
Certainly BCT appears to fall under the growing trend for Russian chemical companies to develop logistics operations in the Baltic State, handling liquid fertiliser shipments for CIS and EU producers. Expanding upon the services offered by BCT, Aleksandr Volohhonski, chairman of the BCT board, comments: “Essentially our operations are relatively straightforward – as a transhipment terminal we receive liquid fertiliser cargo, such as ammonia and UAN, by rail, store it in our tanks, and then load it onto the vessels. Depending on the trading policy and the time of year, the volume of cargo received from each company varies from month to month. At present we purely handle UAN and ammonia, as opposed to any chemical compound products.”
A modern and high-tech terminal, BCT’s target output is one million tonnes of ammonia and one million tonnes of UAN annually. The site’s total tank storage capacity of 120,000 tonnes means that it is capable of handling this huge volume of goods. This capacity is split between two ammonia tanks of 30,000 tonnes each, and three 20,000 tonne UAN tanks. Supporting these assets is a UAN railway unloading area with an unload speed of up to 600 tonnes per hour, ammonia railway unloading area with unload speed of up to 130 tonnes per hour, ammonia compressor room, and two pump rooms for ammonia and UAN. Additionally, a series of UAN and ammonia pipelines and two marine loading arms with a loading rate of up to 1200 tonnes per hour, completes the set-up. In case of any incident during the storage or loading and unloading phases, a fire fighting complex consisting of pump room and two fire water tanks of 600 cubic metres each, and emergency diesel generator forms part of BCT’s contingency plan.
Right from its inception, BCT has been built with expertise at its core, which as Aleksandr notes was a prerequisite in choosing suppliers: “We selected Dutch company Vicoma BV to carry out the basic engineering of the terminal, alongside Proton Ventures, which has a long expertise in the operation of ammonia terminals. For us it was very important to incorporate this type of industry knowledge into the design, to ensure the highest possible standards of performance once operational.” Several other Dutch companies were successful in the tender process, including Kanon Loading Equipment BV for the UAN and ammonia loading arms, European leader Flowserve BV in the supply of ammonia pumps, and Isotherm BV as the material supplier for the isolated ammonia complex.
Now entering its fourth year of operations, BCT’s primary focus is to continue to strengthen its offering through personnel training and up-to-date automated technology. As with any potentially hazardous industrial activity, safety – both in terms of personnel, the public and the environment – is BCT’s primary concern.The terminal itself was designed and built to meet Estonian Republic, Dutch, and EU safety standards through consultation with specialists in their fields.
“We have recently finished the last training programme with our personnel, as part of a year long training drive,” highlights Aleksandr. “Not only are our employees trained on a local basis and in the basic operations of the terminal, but they have undergone sessions with specialists from the UK and the Port of Rotterdam in Hollandon safety and general operations. Some of this training was carried out on-site and incorporating our local rescue services, which will be deployed in the event of an emergency. Certainly, in terms of training we have become proficient in safety, and this remains our core focus for any future development. Programmes such as this, as well as the high technical specifications of our facilities, mean that as EU standards develop in the future, BCT requires little investment or modifications to meet these requirements.”
As part of its environmental management system, BCT has adopted several commitments, including using the most secure technology available to prevent environmental pollution,and to use energy saving technologies where possible in the terminal’s operations. To ensure the successful implementation of these policies BCT is working to raise awareness of both staff and external shareholders in its importance of environmental issues, and to continuously improve the performance of the environmental management system, in line with developments in environmental legislation.
High professionalism of its workforce, and the advantageous long-term experience of its personnel in the field of liquid chemical fertilisers and cargo transhipment are just two of the strengths that BCT has to its credit. “Developments within the oil industry, especially in Europe, mean that there is a tendency to separate natural resources, and basic materials and the added services. This means that a lot of factories within Europe that work in ammonia production are either closed or facing low levels of activity because these products are dependent upon the price of natural gas, and not the price of the material ammonia. As the second liquid chemical fertiliser terminal in the Baltic States there is no longer a monopoly for these services in the market, and considering that we are the most modern terminal in the region, BCT is an attractive proposition for clients,” adds Aleksandr.
In December 2010, BCT reached the milestone of one million tonnes of shipped UAN cargo – a particularly considerable achievement in just three years of operations. Certainly BCT’s strategy of individual attention and consideration to each client’s activities, supported by its high-tech safe facilities has increasingly made its services a common step between liquid chemical fertilisers producers in Russia and the European marketplace. When you consider that ammonia transhipment terminals such as BCTare becoming increasingly rare across the globe, and the expected upturn in the liquid chemical fertiliser market in the next few years, the terminal’s future seems secure.
“In terms of throughput we are still a way off from our targeted output capacity, but considering the current lull in the fertilisers market we are satisfied with our market position, where we have established roots and attracted a strong portfolio of clients. This year we aim to consolidate our position by understanding better what our clients’ wishes are, and I believe apart from simply handling ammonia there are other aspects where we can bring added value to our customers. The design of our facilities enables us to meet any new requirements in the field of liquid chemical fertilisers, and beyond this we hope to expand alongside our clients into the shipping of different types of products – both basic materials and more complex chemical liquid formulas,” concludes Aleksandr.
Baltic Chemical Terminal
Services: Liquid chemical fertiliser transhipment