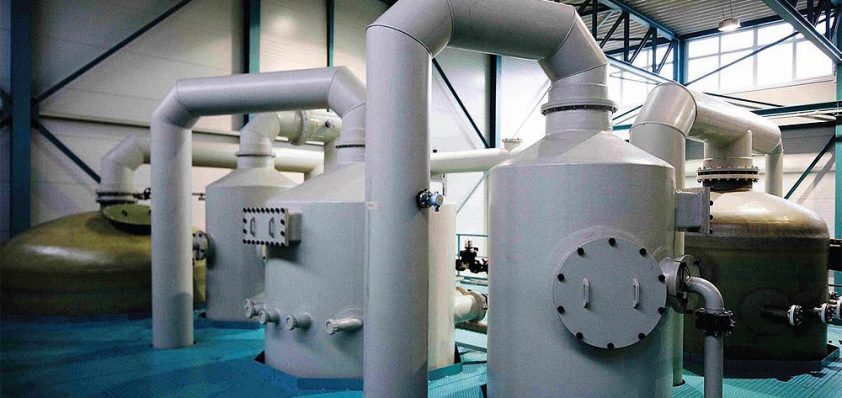
Batrec Industrie AG: Leading Mercury and Battery Recycling Solutions
Clean spirit
Batrec Industrie AG is a recycling company headquartered in Switzerland and operating on a worldwide scale.
Focused on the economic, environmentally friendly and sustainable disposal of hazardous waste, it has specialist interest in batteries, mercury and the reactivation of carbon. Twenty years ago Batrec entered the market as the first battery recycler in the world, and remains the technology leader. Although today, batteries are free of mercury, at that time the product contained 500ppm, and a process was established to recover that mercury. This led to the construction of the mercury recycling centre, and the beginning of the company’s interests in the specialist field.
In November 2011 the company made a large 12 million euro investment into a new plant focusing on the removal of mercury. The element is present in many of the world’s natural gas fields and process plants with brazed aluminum heat exchangers, including LNG facilities and nitrogen rejection units, which are particularly susceptible to corrosive attack by mercury, and assets often require a complete removal of mercury as a result. As a solution, a mercury guard acts as a capture agent, absorbing the mercury from the natural gas in production.
“We treat batteries from the Swiss market and special batteries from abroad that are high in mercury. We are also able to process and treat lithium batteries. It is common in drilling devices and primary lithium batteries throughout the oil and gas industry and represents a big problem,” explains managing director Dieter Offenthaler. The company’s main partner in the mercury removal process is Johnson Matthey, a leading specialty chemicals company. “We developed the plant and capacity together with Johnson Matthey, who were the first ones to bring the product to market. It has been a growing partnership since the beginning. They deliver all their guards to our plant, where we decontaminate and recover the mercury before the next stage of the process. We are able to deal with every kind of mercury waste coming from the petrochemical industry,” he continues.
Batrec has interests in the reactivation of activated carbon from wastewater treatment or air purification applications. The product is decontaminated, reactivated and put back on the market. “We are also capable of treating mercury-contaminated carbon and are recognised as the only plant in the world able to reactivate this kind of spent carbon,” says Dieter. The business is focused on the highest quality, safety and environmental standards. The hazardous waste is turned into valuable raw material that can be returned to the production cycle.
“Our main market, particularly for activated carbon is central Europe as the transportation restrictions do not allow a larger footprint. However, for mercury and mercury loaded carbon, our market is worldwide. As well as our partnership arrangement with Johnson Matthey, we also work directly with the big petrochemical companies. Although our competitors have larger capacities, our plant is specifically designed for the treatment of mercury guards, and we can guarantee the lowest mercury content in the output material, as well as handling the sulphur products that are associated. Importantly we can give a second life to the carbon from mercury-loaded carbon,” Dieter points out.
The operational success of the new plant has been a major milestone for the business over the last 24 months. The scale-up investment was made around the pilot furnace in the battery plant, and was fully designed by its own engineers. Operational for a period of two years, it is now performing at full capacity and the business has eliminated the initial glitches. For a business that has a turnover of 15 million euros, the 12 million euro investment was particularly important. “It is a growing market as the catalyst is becoming more common. It is a significant issue for the companies that have mercury in natural gas.
“The biggest challenge that we are confronted with is not a technical one. It is to build trust with customers across numerous regions such as Asia, Australia and Latin America, and to move the waste from those locations to our plant. We have recently been dealing with imported material from Oman, which was the first importation from a Middle Eastern country. We have been confronted with numerous paperwork issues and developing solutions to address the competence in shipping, negotiation and communication with the authorities. We fully take care, on behalf of the customers, of all the necessary paper work to legally export waste around the world to our plant. To better attend, commercially and administration wise all these challenges on the benefit of both its customers and Batrec, an experienced work force has been contracted recently, ” says Dieter.
As a technologically driven business that operates in an extremely niche market, its competence and know-how is in-house, and as the business grows organically it passes this knowledge across the spectrum of employees. The company has established plans to increase the size of its plant further and produced designs that increase the capacity for the mercury process from 1000 to 3000 tonnes, and to double the capacity for dealing with activated carbon to 6000 tonnes. Dieter explains: “We can add another two furnaces with a very small investment, tripling the capacity for mercury. It is a reaction to what the market is demanding. Mercury is a growing issue that represents the future for our business. Our main focus is to provide a mercury solution for the petrochemical industry, so our next step is looking towards ensuring that investment permission is received for increasing the capacity.”
European legislation prohibits the export of mercury and stipulates that liquid mercury coming from the petrochemical industry in Europe must be safely stored and not sold on within Europe. However, as a Swiss based organisation, Batrec is not part of the EU, so it can sell the recovered mercury into allowed uses. “We are however, governed by what our customers choose, and for the customers that request it, we offer a stabilisation solution to them, transferring the mercury into an amalgam or sulphide prior to reaching a dedicated landfill salt mine in Germany. So for our clients requiring the mercury to be safely withdrawn from the market, we can offer this, or if desired, we can also reuse it in safe and accepted forms. Our long-term vision is to significantly grow within the mercury market and to be recognised in the petrochemical sector and in the industrial world in general as a mercury specialist. Technically, we are capable of covering the full range of mercury issues for our customers, and as we increase our capacity we can become a major player in mercury recycling for the industry.
“We are part of Veolia group and as such are able to offer the full package for the petrochemical industry. We have a very close relationship with Veolia ES Field Services Ltd. in the UK, which is a specialist in handling, transporting and treating hazardous waste from anywhere in the world. Working together we are able to provide customers with a full package service that includes the labelling, containerisation and transportation of the material to our facility, which essentially eliminates the requirement for hands on involvement by the customers,” Dieter concludes.
Batrec Industrie AG
Services: Recycling of batteries, mercury and carbon reactivation