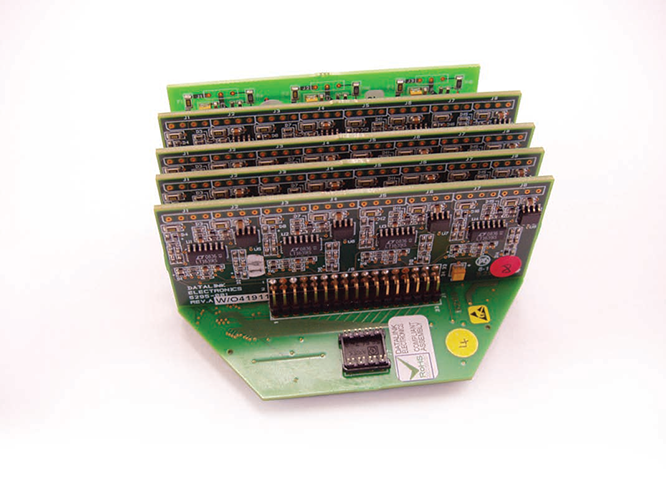
Datalink Electronics Ltd
A complete solution
Working within heavily regulated industries, Datalink Electronics is using its extensive knowledge to design and manufacture certified electronic solutions.
Founded in 1984 with an electronics manufacturing capability by four Hawker Siddeley engineers, Datalink Electronics has developed over the years to offer complete electronic design and manufacture solutions for a wide variety of applications. Work at the beginning of the millennium on MRI systems prompted the company to employ greater engineering capabilities and shortly after that the decision was made to start building a design team. Technical director, Dr Jim Allen explains: “Over the years we have established our design team with the intention to develop products for other people. We have found that having a strong design team, backed by our manufacturing facilities, gives us a very capable business.”
What sets Datalink apart from its competitors is its unique approach to regulation. With the depth of knowledge and expertise present within upper management, particularly within the oil and gas, and medical sectors, the company is well placed to deliver its services within highly regulated industries. “We have found that by working within these two areas we can establish a strong business,” highlights Jim. “Other people don’t like to touch these areas because they can be very complex and very heavily regulated because of safety.” In terms of the oil and gas industry the company is specifically set up to manufacture according to ATEX certification for the use of products in environments with an explosive atmosphere. “ATEX certification not only covers the design of the products but also the quality management that has to be put in place for manufacturing that product,” says Jim. “We’re currently building 30-40 different products for a number of customers that are all ATEX certified.”
Extensive experience in design and manufacture has also given Datalink a strong position in the market. “With a strong design team and a manufacturing capability behind us, once we have designed equipment we can rapidly get it to market because we can do everything in-house under one roof,” expresses Jim. “Our specific focus on electronics also means we can rapidly develop instrumentation for any application from existing frameworks. We have a deliberate policy of handing over the IP generated during a project so that our customers are free to exploit the knowledge and know-how that has resulted from the development process.”
Datalink clients range from pipeline inspection and cleaning companies, to valve suppliers and ATEX certified PC products. “We design a lot of instrumentation devices that go onto, or into, pipelines in order to monitor and track pigs, log data to assess integrity, or monitor other equipment that’s being used within,” adds Jim. One particular system, which is now being used worldwide, is a patented sensor for assessing the thickness of debris on the inside of pipes. The device is ATEX certified, and is scalable to be used within pipes from eight inches upwards. Jim explains: “It’s an essential tool in that when a pipeline has been cleaned by a pig, or chemically, you can never be fully sure that all the debris has been taken out. The equipment allows our customer to assess whether the pipeline has been adequately cleaned for it to operate at its optimum.” Other systems developed for the oil and gas industry include acoustic and ultrasonic tools for detecting leakage from valves in highpressure pipework, pipeline mapping systems and handheld monitoring tools to diagnose faults or assess the condition of plantwork.
The nature of the business operating in the development of instrumentation to support plant maintenance has protected it from the recent decline in the oil industry. Despite noticing significant effects on employment in the areas it is working in, Jim notes that: “The projects we’re working on are carrying on, perhaps because people have realised that with lower demand for oil and gas they can take a breather and start looking at the condition of the plant & pipework.” Challenges come from other directions for Datalink. As Jim continues: “Working in electronics there is the ever present challenge of the rate at which technology is advancing. Whilst presenting challenges however, it also opens up a number of opportunities. When I began my career in pipeline inspection, data would be stored on large tape recorders, with long download and processing times, now a USB stick can save it all and information can be processed far quicker.” With the rate that the technology is moving, Datalink has opportunities opened up to it that weren’t even available a short period ago, and this ongoing process is a major driving force for the company.
Looking forward, Datalink is very much focused on maintaining its current strategy and position in the market. “We want to continue engaging with the industries that we work in to make sure we are always working on a number of innovative and creative projects,” highlights Jim. “Looking even further ahead, we are thinking about other highly regulated markets where we may be able to apply our knowledge.” With extensive experience in electronics design and manufacture within highly regulated markets Datalink has established a strong business. By making a habit of fully understanding not only industrial, but also geographical legislature the company looks set to achieve further success in those areas which demand increasingly high standards.
Datalink Electronics Ltd
Services: Design and manufacture electronic solutions within highly regulated industries
Issue 122 July 2015