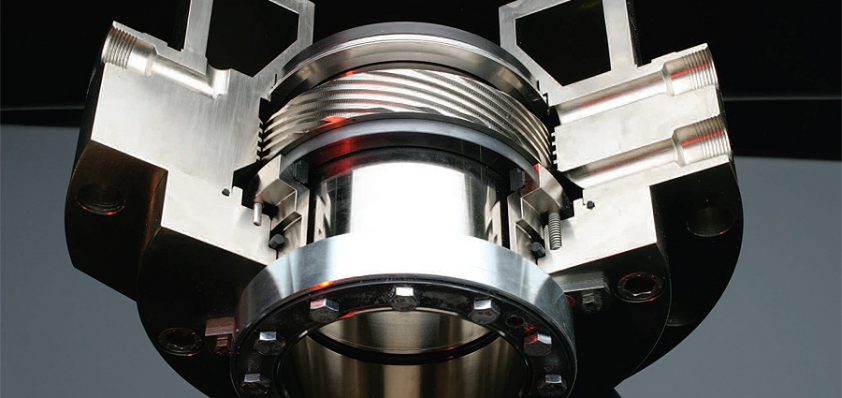
EagleBurgmann Industries UK
The seal deal
EagleBurgmann Industries UK, is part of the EBI Alliance, one of the top suppliers of sealing technology in the world.
For the last 120 years, the company has been supplying products ranging from highlycomplex dynamic sealing systems to static seals for all applications in many industrial sectors all over the globe.
Burgmann products are synonymous with reliability and quality, whether they are for pumps, compressors or mixers in the water and waste utility, the chemical and petrochemical market, the oil and gas industry, pulp and paper production or in power stations. The continuous improvement process at all levels, constructive ideas, technical innovation and an expanding global sales and service network are cornerstones of the company’s success and guarantee both operators and end users the high availability and efficiency of their plant and equipment.
Under the name EBI (EagleBurgmann Industries – the worldwide alliance for sealing technology) – Burgmann Industries, together with Eagle Industry, the Japanese mechanical seal manufacturer, and its owner Freudenberg, a family company offering its customers technically challenging product solutions and services, has laid the foundation for a highly promising worldwide co-operation. The basis of this arrangement is an intensive and trust-based relationship that notably strengthens the global competitiveness of both partners and makes them one of the leaders of sealing technology on the world market.
The global presence of EagleBurgmann’s operations is a significant contributor to the company’s success, because customers want suppliers in close proximity, who can offer speedy solutions to their problems. As EBI has presence all over the world, it can offer an indepth package of services in almost any location. The services on offer range from simple stuffing box packing to the complex high-tech seal, and is reinforced by the backing of EagleBurgmann’s ‘Total Seal Care’ modular support offering, which allows each customer to put together exactly the right service package based on individual needs and requirements.
On the basis of the modules chosen by the client, EagleBurgmann draws up a comprehensive, customised service concept. It assumes responsibility for a specific area of activity right through to providing a comprehensive in-plant seal service.
An example of how a concept of this type evolves is the service agreement EagleBurmann formed with the Mider Refinery in Leuna, Germany. As early as the facility’s project phase, the operator pursued a rigorous strategy of outsourcing for all operational areas, but especially where services were concerned. As regards mechanical seals, the refinery operator was looking for a manufacturer not only capable of supplying and repairing them but also of offering further advantages for the facility’s operation by raising service life, assuming inventory management, and engineering tasks involving what are known as ‘bad actors’. In 1997, having supplied just 39 per cent of the refinery’s seal units at the time, Burgmann took over the servicing of the facility’s entire complement of installed seals, and to this end opened an on-site service centre. By way of this forward-looking fixed-cost concept, Burgmann guarantees Mider annually reduced costs for the maintenance and repair of mechanical seals. This in turn provides a secure and reliable basis for cost planning and additional savings over the entire contractual period.
Since the service agreement came into effect the refinery’s overall expenditure for mechanical seals has been cut by 47 per cent, repairs by 20 per cent and the costs for the 20 most costly ‘bad actors’ by 44 per cent. Repair times in the service centre have been halved from ten to five days. This success is down to close co-operation with the refinery operator, the pump manufacturers, and EagleBurmann’s competitors in the seal sector as well. In addition, customised software has proven itself in enabling Burgmann to log and analyse all repairs and costs relating to the refinery’s mechanical seals.
EagleBurgmann solutions are formulated with a clear objective: Making its customers more successful. This means the company has to create innovative, economically rational and easy-to-use seal solutions that help to fulfil the highest requirements in terms of environmental protection and safety, which are designed to increase customers’ efficiency and productivity.
The technical knowledge, creativity, motivation and performance of EagleBurgmann’s workforce makes a major contribution to achieving these objectives and making customers more successful – and on the company’s extensive website, the staff are highly praised: ‘no matter where or in what respect, our achievements are down to our staff. Their ideas, working spirit and identification with the company have put us where we are today, namely at the head of the field. As an integral part of our company, each and every employee shares responsibility on the path to achieving our common goals.’
Creating a culture of success needs a modern style of management, which encourages employee involvement and acceptance of personal responsibility, plus a performancerelated remuneration system and intensive vocational and advanced training. All these are pursued at EagleBurgmann, to ensure that its employees continue to enhance the company’s performance and augment its global profile as a reliable, competent partner for high quality and technological leadership.
EagleBurgmann
www.burgmann.com