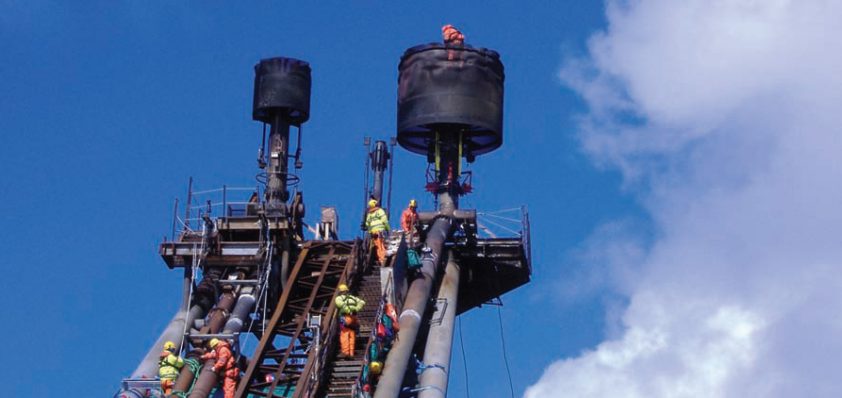
EM&I: Innovating Asset Integrity Management for Offshore Oil & Gas
Delivering integrity
Over the last 37 years, the EM&I Alliance has positioned itself as an industry leader providing asset integrity management, inspection and specialist repair and maintenance services.
EM&I established itself in the Aberdeen market by supplying specialist NDT services to fixed jacket type installations in the North Sea. Since then the business has undergone quite a transformation, not least by establishing a global operations base active in all the major locations for offshore oil and gas exploration and production including; Asia Pacific, Europe, Africa, the US, Canada and Brazil.
Today, EM&I provides comprehensive asset integrity management services, a wide range of non-intrusive inspection services and specialist in-situ repair and maintenance, focused on floating production type assets. This suite of services has been developed around the simple concept of ‘No Drydock… Safely’. Elaborating upon this approach, chief operating officer Alexander Constantinis explains: “We are helping our clients to avoid having to send their floating productionassets to drydock – the financial savings of which present a very clear business case. Often, prescriptive regimes require asset owners or operators to send these assets to drydock once every five years, but our holistic range of services is designed to help them avoid doing that.”
A central component of the service offering is EM&I’s O-AIMS (Operating Asset Integrity Management System). “This is a suite of engineering services that we have developed through close co-operation with our oil and gas major clients over the last 15 years,” describes Alexander. “O-AIMS is an extremely diverse offering. At one end of the spectrum we worked closely with an oil and gas company to develop its highest-level philosophy and strategy statements describing how asset integrity is managed. At the other end we regularly deliver cost effective criticality based inspection plans describing how, when, and what to inspect on the client’s asset. The purpose of O-AIMS is to ensure compliance with regulatory and our clients’ own corporate standards, but also to help clients understand the risks that an operator of these types of facilities carry, and the remedial action needed in order to mitigate those risks.” In the wake of major global incidents, the demand for asset integrity management services of this nature has grown as oil and gas companies place greater demand on their supply chain to ensure they are compliant with corporate and regulatory standards – this is now being widely extended to include assets that they don’t own or operate themselves.
By providing a clear overview of key asset integrity threats in a prioritised manner delivered through a clearly presented integrity status reports, EM&I provides its clients not only with this understanding, but also a clear focus for the inspection and maintenance spend on the crucial areas of plant. EM&I’s system organises the various components through a criticality based assessment into; safety, business and environmentally critical elements. This in turn enables them to be managed in terms of overall integrity importance.
Likewise, EM&I can carry out fitness for service calculations using a risk based approach to defer, or even prevent, intrusive inspection on particular items of plant. By gathering an understanding of the condition of plant, for example a pressure vessel, from the outside by way of specialist inspection techniques, EM&I is able to build up a sound case to safely defer intrusive inspections – challenging prescriptive manufacturer based recommendations. Preventing shut-downs, or at least reducing their frequency and duration can represent savings of many millions of US dollars a day in lost production costs.
Whilst EM&I relies on tried and tested techniques to achieve these client led objectives, the business has a strong focus on innovation. Through continuous dialogue with its clients it attempts to identify recurring challenges and aims to develop an innovative response. A significant portion of EM&I’s annual expenditure is devoted to innovation and its team are busy working on a number of different client led initiatives, including the ability to retrofit an Impressed Current Cathodic Protection (ICCP) system onto several of its client’s Floating Production Storage Offloading (FPSO) assets whilst on station. For those not familiar with such a method, an ICCP system on a Floating Production Unit (FPU) is designed to prevent corrosion to the hull and associated structures by way of an electric field. Many of the world’s FPSO fleet use sacrificial anodes. Alexander explains that these are better suited for installation on non-floating production hulls such as those used as tankers thus allowing replacement during the regular dry-docking cycle or by divers – something not easy to achieve for a floating production asset.
“Our technique uses a specially modified hot tap tool to create a hole in the side of the vessel, under the water line, whilst it remains on station allowing us to install the specially designed anodes for the ICCP system from the inside of the hull without the need for diver intervention,” he reveals. “We have already carried out successful validations at the UK National Hyperbaric Centre, and have visited two FPSOs to carry out advanced survey work, so we are now looking to secure the first order to prove the system. This will represent an industry first and, from our analysis of the market a huge wealth of opportunity for the business.”
As this article went to press EM&I had just received some exciting news regarding the formalising of a relationship with Inversa Systems in the form of a Strategic Technology Alliance. The agreement focuses on a highly innovative technology, developed and patented by Inversa Systems, called Backscatter Computed Tomography (BCT) which provides imagery previously impossible to obtain. BCT uses back scattered radiation to create an image of internal defects within critical infrastructure. The technology has the unique ability to inspect components of almost any material, in detail, non-destructively and non-intrusively with only single-side access required. EM&I is proud to partner with the exciting and creative team at Inversa in offering exclusive worldwide use of this technology to its oil and gas clients. “BCT is one of those rare technologies that represents a ‘game changer’ in non-destructive and non-intrusive inspection,” explains Alexander. The system will enable previously impossible repair or replace decisions, the detection of pitting and corrosion through insulation, as well as catching defects early while they can be economically repaired – all on items of plant that previously required intrusive techniques and large shut-down intervals to assess condition.
EM&I is behind the creation of a recently launched a Joint Industry Project (JIP) entitled HITS (Hull Inspection Techniques & Strategy). The JIP is expected to bring together Operators, Classification Societies, Regulators, Equipment Manufacturers and Inspection Contractors to define the objectives of the Operators hull integrity strategies and to then determine whether these strategies can be translated into practical, effective and compliant hull integrity and inspection plans. Alexander comments, “This JIP is focussed on finding out what data is needed to assure hull integrity, how best to obtain it and whether this will assure class and the regulators.” He goes on to say, “A key objective is to develop clear guidance on hull structural integrity requirements and strategies. Following this we hope to identify and develop selected inspection methodologies and test them in the field, resulting in recommendations along with a cost benefit analysis for implementing an optimised hull structural integrity strategy.”
EM&I’s focus on floating production type assets has also not been without careful thought, as Alexander explains, “In order to tap into deeper reserves, floating production and sub-sea focussed developments remain the viable options, representing a cost effective method for extracting hydrocarbons from previously inaccessible locations. The rate of growth in the floating production sector remains exciting with FPSOs continuing to dominate 81 per cent of forecasted global Floating Production System (FPS) spend.”
In terms of how EM&I intends to continue to capitalise on these opportunities, Alexander concludes with his vision for the next few years: “Our marketing challenge is to convince our clients to see the value proposition in our complete range of services – whilst we regularly face stiff competition, there are few organisations we come across offering our combination of engineering and hands on site based services. We have built a great reputation in being able to deliver this, and we will continue to strive for excellence in all aspects of our business.” One area where EM&I continues to excel is health and safety. The organisation achieved its fourth RoSPA (Royal Society for the Prevention of Accidents) Gold award in 2011 and is determined to achieve its fifth in 2012.
Alexander adds, “We believe there is a very strong growth potential for EM&I in the foreseeable future. With our momentum in Asia Pacific driving the business and significant growth potential in West Africa and South America we are well placed to deliver.”
EM&I Alliance
Services: Asset integrity management