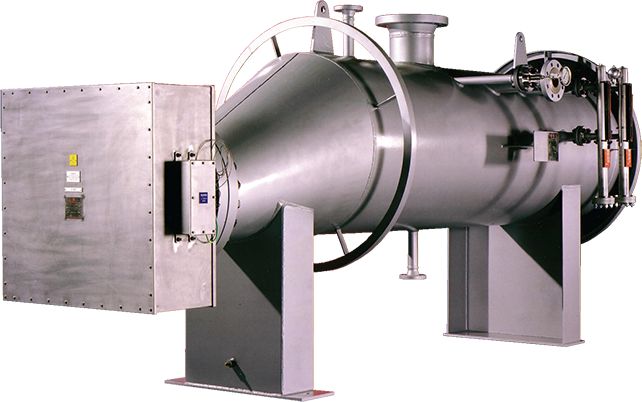
Exheat Ltd
Hot property
A family run business, Exheat began life in 1991 and has since become recognised as one of the world’s leaders in the design, engineering, and manufacture of electric process heaters and control systems.
Today this Group comprises of four separate entities – Exheat Ltd, which undertakes manufacturing, sales and engineering for the UK, European, Russian and US markets; Exheat Pte Ltd, which covers sales and engineering in the Middle East and Asia; Ex Service Pte Ltd offering global aftersales support, commissioning, maintenance, technical support, replacements, training, and on-site repairs; and Exheat Industrial Ltd, which provides a standard range of products designed for original equipment manufacturers (OEMs) and the industrial sector.
As just one element of this Group, Exheat Ltd employs a staff of 160 across two manufacturing sites in Watton, Norfolk. By way of an introduction to the company’s core markets, marketing director Robert Smithers says: “We are present in a vast spread of markets such as oil and gas, petrochemical plants, power generation, refineries, utilities, food processing, pharmaceutical, marine, and manufacturing. As a Group, our product focus sets us apart from our main competitors, which have diversified into other areas, we only design and manufacture heating systems for hazardous area or explosion proof applications.
“Within the oil and gas sector, generally we supply to engineering companies (EPCs) or the fabricators of skid packages. Key to our success is our ability to engineer our heating systems to comply with all regional design and safety standards. Being an electrical pressure retaining system, the design must meet stringent safety requirements for hazardous areas classified zones.”
Particular applications of these products include heating of heavy or extra heavy crude oil to reduce its viscosity, preheating of natural gas before pressure reduction, and pre-heater and super heater for fuel gas conditioning. “All process heaters are different, as typically clients will need to heat their medium to a specific temperature whilst also meeting the strict certification and client specification requirements,” notes Robert.
“These process requirements are calculated with our in-house design software to determine the heating duty required for the application. We can then use this to develop an optimal design that meets all design codes, safety and certification standards. This is where our experience in engineering is vital, manipulating the design to provide an efficient and cost effective solution.”
He continues with how this expertise is serving the business well in the current market: “Typically we will assist clients that are tendering for contracts at the FEED stage even if the project doesn’t go ahead. We are able to do this efficiently with our in-house design software. This also gives us the advantage when a project is signed off, as we can quickly make technical changes to quotations with flexibility and speed. The challenge for us is not the manufacture of the equipment, but the engineering and procurement. On average we may work with around ten to 15 suppliers on one heater and control panel, which means meeting deadlines, as well as quality control, leaves very little margin for error. This is compounded further if when mid-way through the procurement phase the client changes the design.”
Recently, Exheat Ltd has introduced a new standard range of hazardous area Cast Aluminium line heaters, which provides an effective heating solution for constant and varying flow liquids or gases. This eliminates the requirement for a costly pressure vessel in high-pressure applications. Incorporating electric heating elements and an indirect process heating coil imbedded within marine grade cast aluminium, this design combines excellent heat transfer properties with low surface temperatures.
In support of new product development activities such as these, Exheat Ltd has also invested in a new research and development (R&D) department. “We have invested heavily in R&D to look at new technologies and manufacturing techniques to help bring cost savings and delivery time reductions to our customers. This new department will enable us to introduce new innovative designs and improve the current range of standard products. Over the next three months we have two new ranges due to launch, which are currently in the testing and approvals phase. These products will be focused on air heating for enclosures, and fan assisted heaters for spacing heating areas classed as a hazardous zone,” elaborates Robert.
R&D has also played a key role in the introduction of Exheat Ltd’s new 3D design software, which is due to go live in July 2011. Capable of interfacing with all current systems, this software will being a much higher level of detail to the company’s proposals, enabling revisions to be made instantly. It will also help reduce engineering time through automated drawings, handle all documentation, improve departmental work flow in managing all in-house approvals, and eliminate any human error in BOM inputs.
As a business that has been consistently growing for some time by investing extensively in its various resources, Exheat Ltd ensures that it remains well placed to fulfil upcoming opportunities within its work scope. As an indicator of this, earlier this year the company successfully supplied fuel gas heaters, CIP tank heaters and glycol heaters to Petrobras’ new semi-submersible unit – platform P-56. Exheat Ltd’s success has also been more widely recognised with the company achieving rank 70 in The Sunday Times’ 2010 Profit Track 100 league table, which lists Britain’s 100 private companies with the fastest-growing profits. Following on from this, Exheat Ltd’s five-year strategy is now based around continuing to improve its internal efficiencies in order to handle any further growth in the business as a result of its upcoming product development drive.
Exheat Ltd
Services: Electric process heaters and control systems