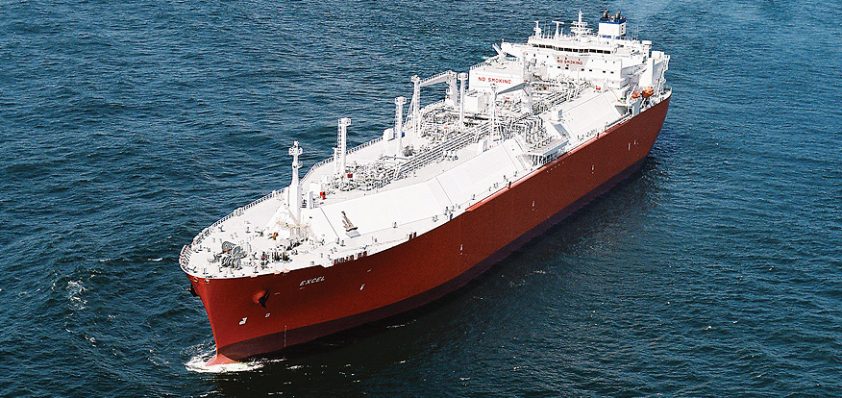
Exmar: Leading Innovation in LPG, LNG, and Offshore Shipping
A buoyant future
Based in Belgium, Exmar has a history dating back to 1829 and is a global specialist in liquefied petroleum gas (LPG), liquefied natural gas (LNG) and offshore shipping services.
The company’s main activities revolve around the ownership and operation of a modern gas carrier fleet, transporting liquefied gases such as butane, propane, anhydrous ammonia and petrochemicals to industry. With a distinct heritage of innovation in the oil and gas realm, Exmar works closely with a wide variety of partners to create ideal solutions for clients all over the world.
Dirk Carpentier, technical director of the company, outlines its background and fleet operations: “Exmar is actively committed to LPG, ammonia and LNG shipping as well as offshore oil and gas applications. We have a large composition of vessels consisting of four very large gas carriers, 16 midsize LPG carriers and nine LNG ships. Two of these are conventional LNG carriers and seven have re-gassification capabilities on board, whereas four are under construction. We transport large amounts of LPG and ammonia worldwide both on the basis of long-term charters and on the spot market. In addition, we have invested in ten pressurised LPG ships, of which seven have a 3500 cubic metre capacity and the remaining three a capacity of 5000 cubic metre – they have all been built or are under construction in Japan.”
Through highly experienced crew management and in-house technical know-how the company is continuously developing its fleet capacity and abilities to accommodate and increase service to the industry. This continuous spiral of development has lead to many successful collaborations with other expert organisations.
One of the organisation’s latest alliances has been with Excelerate and Black and Veatch, to create a floating liquefaction, storage and offloading solution. Dirk highlights the benefits of working with others from the industry: “We have a tripartite agreement working towards this new solution. Black and Veatch is helping with the technological side of the project; Excelerate, as a gas trader, is bringing in its know-how of gas movement; while Exmar is adding the knowledge from the marine side. This project is developing nicely and we have clear ideas of how we want it to look now.”
Exmar has been responsible for the creation of a number of original concepts for offshore oil and gas procedures and constructions. Exmar’s OPTI-EX is a production semi-submersible capable of operating at water depths up to 3000m. The mission of the OPTI-EX is to provide field operators with a flexible production facility for early production/long duration well tests and full field developments. The modular design of the production facilities and the equipment specification allow for the production of a broad range of reservoir characteristics. In addition to the ability of the facility to accommodate a broad range of oil specifications the OPTI-EX has additional gas handling equipment that provides even greater utility to operators as from day one. In keeping with the mission of being both a short and long term facility the OPTI-EX was designed with the understanding that the flaring of gas should be limited as much as possible. To this end, the OPTI-EX not only has the equipment to export gas but also to re-inject for gas-lift.
With a single deck for easy access and customisation, simple construction, re-usability and a quick start-up facility, the OPTI-EX caters to the requirements of the often-volatile oil and gas conditions. Designed to provide an economic solution for gas fields, deepwater oil and gas developments and to reduce project execution risks – this Exmar own-design provides hull stability and topside versatility for the market.
Dirk talks European Oil and Gas through the company’s most recent innovation in re-gassing: “Methane natural gas is normally shipped in liquid formation in temperatures of minus 160 degrees. We are expanding in LNG carriers and the re-gassing ships, and as such we are developing with Excelerate to secure access to key markets by creating various discharge points through either buoys near the coast or high pressure loading arms at quayside. To demonstrate, re-gassing buoys are connected to a pipeline system, which in turn is connected to a domestic gas system. They work by lying just under the waters surface until needed when they can be pulled onboard through a hole in the ship’s bottom – the buoy is linked to a high-pressure line that allows the ship to start re-gassing. This system has advantages in that by discharging high-pressure natural gas directly into the pipeline network, the need for a separate regasification plant onshore is bypassed – ships are able to re-gas from a remote location.”
Linked to this are Exmar’s ‘Energy Bridge’ regasification vessels (LNGRV) which are on long-term contracts to Excelerate Energy (USA) and which, in using this mooring technology, are able to provide an alternative to onshore LNG import terminals. By using the system mentioned above the vessel is able to regasify LNG on board and discharge the high-pressure gas directly into the consumer grid system, bypassing the conventional land-based terminals. The first of these vessels Excelsior with a capacity of 138,000 cubic metres was delivered in 2005 from DSME. Since then a further three have been added to the fleet while four more are currently under construction. At present two sets of buoys are fully operational, the first set (one buoy) in the Gulf of Mexico has gas volumes in excess of 500 million cubic feet per day, while the other set based in the Northeast Gateway can deliver up to 800 million cubic feet per day. This system is expected to continue to grow in popularity as onshore storage grows scarce.
Ship-to-ship transfer has been another area of emphasis for the company and its partners, continuing the mission to reduce the need for docking facilities during project operations. Ship-to-Ship transfer involves a number of safety risks and is subject to strict regulation. Exmar’s mission was to design and build, in the shortest time possible, a safe and simple system to allow transfer between any standard LNG carrier and an LNGRV in a side-by-side configuration, in relatively calm weather conditions.
Three sets of two 15 metre, eight inch hoses are fitted through Y-spool pieces to a 16 inch manifold line and hang freely between the two vessels with protection saddles in way of handrails. Multi-layered composite hoses have a very high safety factor and safety rupture mechanism where failures do not propagate through the whole thickness in case of a local defect. An emergency release connector is also fitted to achieve the utmost in safety provision. Exmar approached this task with its practical experience, taking on a challenge that many had failed to complete. This development enhances the possibilities for LNGRVs by enabling them to take on cargo in open sea near the offloading buoy – connecting the organisation’s two main concepts of regassing remote buoys and ship-to-ship transfer.
Dirk notes: “The first time we completed ship-to-ship transfer was in the Gulf of Mexico where a total of 20,650 cubic metres of LNG was successfully transferred. We have just finished a project in Argentina, continuously refilling our own ships, as well as others, using our technique. In alliance with Excelerate we are unique in the field for this technology, and this milestone innovation provides enhanced operational flexibility for the regasification vessels.” Most of the vessels have embarked on long-term contracts with Excelerate.
With a portfolio spanning the world, Exmar’s environmental policy is of immense importance. LNG and LPG are generally recognised as energy sources with considerably less environmental impact than traditional energy sources such as coal and oil, but even so, as a major marine operator the company has a responsibility to the environment surrounding its areas of business. Exmar endeavours to support sustainable growth by attaching the greatest importance to the quality of its fleet and services, the safety of personnel and equipment, as well as the protection of the environment. The company works in line with new technological developments in shipping to reduce environmental impact, with emphasis on saving fuel and using non biocidal foul release coating systems for underwater hulls.
As a forerunner in the industry, Exmar aims to remain one step ahead of forthcoming legislation by embedding continuous improvement and risk management policies into day-to-day procedures. The company is gearing up for ISO 14001 certification by partaking in Environmental Aspect and Impact assessment in the fleet and putting an Environmental Management Action Plan for Shipmanagement of LPG and LNG carriers in place. Already complying with low sulphur regulations and holding a green passport for new ships in anticipation of IMO draft guidelines, the company is proactive in the maintenance of safe working environments for both personnel and nature.
Further to offshore shipping operations, Exmar is able to offer a range of additional comprehensive services and ship management facilities. The business provides a variety of insurance and travel solutions in conjunction with subsidiaries such as the Belgian insurance broker Belgibo and Travel Plus travel agency. Formerly known as Tecto, Exmar Shipmanagement offers decades of experience and expertise in the management of a whole range of ship types including LNG carriers, LPG carriers, chemical tankers and floating units for both storage and accommodation.
Supplemented by procurement services, technical marine consultancy and assistance, sale and purchase inspection, and plan approval, Exmar is the ultimate all-rounder for those working in the oil and gas industry. With a distinct mission statement to provide ship management and ancillary services to ship owners and operators in order to achieve the highest possible reliability at a fair operating cost, the company’s maintenance philosophy is focused on the long-life of ships. Highly technical employees apply this philosophy to prevent the breakdown of machinery and equipment which results in costly off-hires and expensive repairs; ensure safety, quality and efficiency; optimise manpower, machinery and money resources; control spare parts stock on board and to protect customers assets for the long term.
The dedication to providing professional, quality services runs throughout the company, at every level of employment. Staff are thoroughly trained from basic workers to European officers, with Exmar providing courses on bridge resource management, manned model ship handling, simulator training and evaluation courses, to name but a few.
Whilst Exmar has its headquarters in Antwerp, it also has offices in London, Houston, Paris, Shanghai, Tripoli and Luanda, and last year saw the company reach a turnover of over 500 million dollars. With the organisation’s rate of development and innovation, coupled with the backing of its partners around the world, its influence in the market is set to grow. Dirk outlines Exmar’s experience of the current industry conditions: “We have to accept that we are in a worldwide crisis and there has been a downturn in some areas of the business. However, I think by continuously searching for opportunities and taking initiatives in other areas such as floating liquefaction, this can be overcome.”
The company’s strengths have always been in its knowledge of the oil and gas industry; how it works, what equipment is needed and the diverse conditions in which it operates. Being able to deploy its technical and commercial staff to work on shipyards and offshore projects makes it a popular, trusted option for shipping companies. Variety is a further advantage for Exmar, with its numerous affiliations with partners and co-owners leading to a diverse range of expert deliverance; for example, the OPTI-EX semi-sub platform is being finalised in Houston and Corpus Christi in the US, while at the same time a new high specification accommodation barge is being built in the Cosco shipyards in China for establishment in West Africa later in the year.
Dirk concludes with his vision for Exmar’s future: “We want to continue development from our current position in the market. I think we will see further involvement in projects linked to gas on-board regasification and floating liquefaction developments. But you have to look quite far into the future to predict where you will be; lead times for floating equipment are still in the region of three to four years. We have interesting operations and contacts throughout the world, at the moment for example, we have a team of staff out in Shanghai involved in newbuildings and engine developments – we are well positioned for worldwide growth.”
Exmar
Services Oil and gas shipping services