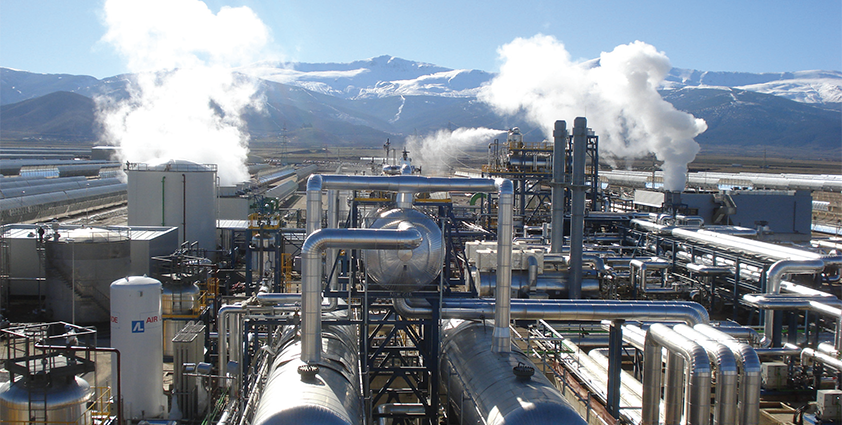
Flowserve Corporation
Power partner
Solar thermal power generation Diverse market studies from SARASIN, Greenpeace or IEA show a forecast of 400 to 900 solar thermal power plants worldwide until 2020. Also, Governments worldwide are forcing the development of electricity generation from renewable and alternative sources of energy. At present this is a high growth market that has significant future potential.
To achieve higher temperatures mirrors are used to concentrate solar radiation. The main concentrated solar power (CSP) technologies currently available are the parabolic trough technology, power tower systems and dish systems. The basic principles are the heat gain where the heat is accumulated from the sun in the system, the heat transfer from the absorber to the heat exchanger and the heat storage, which enables the use of solar power for base load generation as well as peak power generation. Common operating fluids are synthetic oil, a liquid mixture of nitrate salts or pressurised steam. The composition of the mixture of nitrate salts is 60 per cent weight of sodium nitrate (NaNO3) and 40 per cent weight of potassium nitrate (KNO3). The melting point of the nitrate salts is 221 °C.
Parabolic trough technology
Parabolic trough power plants use long parallel rows of parabolic reflectors that concentrate the direct solar radiation onto an absorber tube located along the focal line of the collector. The mirrors with a parabolic shape focus the sun at 30 to 60 times its normal intensity, and the heat transfer fluid (HTF), usually synthetic oil, is circulated through the absorber pipes reaching temperatures as high as 400 °C, which generates steam with a heat exchanger to drive the steam turbine generator of a conventional power block. Without storage the system is able to generate power when the sun is shining.
Solar power tower systems
Solar power towers use an array of flat, moveable mirrors, called heliostats, to focusthe suns rays upon a receiver located at the top of a tower. The receiver collects the heat of the sun in a heat transfer fluid, which is used to generate steam for a steam turbine for the production of electricity. The plants use molten salt to transfer and store heat. Molten salt is used in solar power tower systems because it is a liquid at atmosphere pressure, its operating temperatures are compatible with usual steam turbines and it is non-flammable and non-toxic. It also processes high thermal conductivity allowing temperatures to reach 600 °C.
The advantage of this system above the parabolic trough design is the higher temperature. The efficiency of heat engines increases with the temperature of the heat source. Furthermore, high temperatures also make heat storage more efficient.
The mirrors are more complex because a tracking system is necessary that follows the position of the sun. Each mirror must have its own dual axis control, while the parabolic through design does not require tracking on a second axis.
Molten salt heat exchange storage
Molten salt heat exchange storage technology allows the generation of electricity at night and on overcast days using the stored thermal energy in the hot salt tank. With the current technology, the storage of heat is much cheaper and more efficient than the storage of electricity. Pumps circulate the cool liquid salt nitrate of min. 290 °C from a cold tank through the receiver or heat exchanger to a hot tank. The molten salt, which has been heated up to 400 °C or 600 °C, flows through a heat exchanger for steam generation back to the cold tank.
Flowserve Corporation
One of the world’s leading single-source providers of flow management products, offers the most comprehensive package of control valves and pump products for the concentrated solar power Industry. From molten salts to heat transfer fluids, Flowserve has proven control valves and pump solutions that are both highly reliable and highly efficient.
Flowserve’s Villach Operation, based in Austria, has delivered control valves for the most famous solar thermal power plants in Spain, such as ANDASOL 1+2, EXTRESOL 1+2, MANCHASOL 1+2, SAMCASOL 1+2 and GEMASOLAR. The Villach Operation develops and manufactures top quality control valves in ANSI and DIN design up to 48”, class 150 to 2500 and up to DN 400, PN10 to 400. For customers, Flowserve control valves offer superior performance in liquid and gaseous services, while at the same time permitting easy, fast and inexpensive maintenance.
For the control loop of the heat storage medium Flowserve has developed special valves to meet the high requirements on sealing components, operation and reliability. The excellent performance of Flowserve control valves guarantees an optimal process control.
Control valves for solar thermal power plants
Due to reliability and harsh operating conditions control valves have a critical role in solar thermal power plants. Synthetic oil used as heat transfer fluid is extremely amenable to leaking, therefore a bellow seal with safety stuffing box is recommended to seal the valve stem. A shroudless design is preferred for this application.
Control valves to be used for molten nitrate salt service are specially designed because the media is corrosive, and under certain conditions, abrasive. Also, the process runs at high pressures and temperatures. Salts precipitate out during the process, and they can be present in crystalline form. The type of control valves are usually globe control valves, butt welded with extended spool. Flange connections are to be avoided.
Depending on the operating temperature suitable materials to be used for the body are Cr-Mo materials like A 217 WC6, A 217 WC9 or A351 CF8M.
Extended bonnets are needed in order to keep the packing temperature within admissible values and to allow insulation of the valve body. Guiding bush and stem shall be in Alloy 6 to avoid galling. To reduce dead room a double stem guided design is preferred, and trim material is stainless steel like 316 SS with full contour in Alloy 6 for harsh operating conditions. Screwed seat ring with metal-to-metal sealing is not recommended. At high temperatures molten salt is a strong oxidizing fluid. Carbon or graphite are not suitable for oxidizing fluids, therefore these materials are not acceptable in nitrate salt service. Special metal gaskets are used for the bonnet, cage and seat ring. The packing system is modified to separate the fluid from direct contact with the graphite.
Special tailored control valves allow draining of the pipe system. These are modified angle type valves, flow over with contour in the seat. The contoured seat is optimised for flow to close and guarantee good control behaviour at extreme low loads of below ten per cent. The seat leakage will remain low over a long period of operation because the sealing area is separated from the vena contracta and is therefore not exposed to a high flow velocity. A multi-step trim will avoid cavitation at high difference pressure.
Flowserve Corporation
Services: Flow management products