How Leeward Renewable Energy (LRE) is driving advancements in sustainable energy production
With a large collection of 30 wind, solar and energy storage facilities across the US with a total generating capacity of over three gigawatts, Leeward Renewable Energy (LRE) is a high-growth renewable energy company. At its current pace, LRE expects to commercialize over 1.5 GW of renewable energy projects within the next year. The organization is a portfolio company of OMERS Infrastructure, a global infrastructure investor and investment arm of OMERS, one of Canada’s largest defined benefit pension plans. As passionate renewable energy advocates, the LRE team is focused on building sustainable solutions for clean, renewable energy, while empowering communities through energy independence, job creation, and lasting partnerships. We interviewed Jason Allen, Chief Executive Officer, to learn more about LRE’s scope of operations.
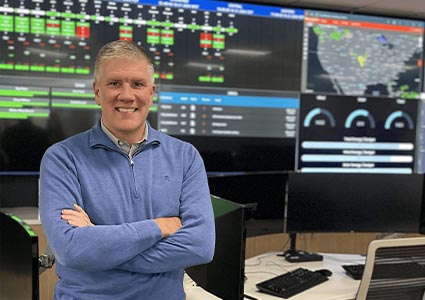
“As an independent power producer, our focus is on three core areas: onshore wind, solar energy, and storage. We pursue a high-growth strategy across a balanced portfolio, with one-third of our operations dedicated to each segment. This diversification ensures complementary generation profiles and enhanced reliability. Although there are several companies in the US with similar offerings, we have now been in this industry as a company for over two decades, during which we have honed a unique approach to project development and the type of customers we serve. Over the past 23 years, we have witnessed significant advancements in renewable energy technology, enabling us to evolve from a wind-centric organization in the early 2000s to repowering the majority of our original wind assets today while also expanding into solar energy and battery storage. Our long-standing relationships and personalized approach with landowners and off-takers have ensured a seamless transition, as they are familiar with our company and the way we operate. These established relationships have allowed us to differentiate ourselves in the market.
“We are looking to add approximately 1.5 gigawatts of new generation per year and, with the strong financial backing of OMERS, we can adopt a long-term view in our development program, the technologies we invest in, the way we design our projects, and how we manage safety. Our final key differentiator is that we are specifically focused on domestic content, including US labor and steel. We prioritize ethically and domestically made and sourced materials, partnering with companies that share our commitment to quality and sustainability. This year, about 75 percent of our projects utilized domestic content, and we aim to increase this percentage over the next couple of years,” Jason elaborates.
Digital twins
Jason tells us more about how LRE is incorporating artificial intelligence (AI) technology into its operations. “Over the last three to four years, we have seen a massive improvement in the technologies available to us. There are a few major areas of our operations where we use both data and AI to improve our performance. First, on the operating side of the business, as a 3.5 gigawatt (and soon to be over four gigawatt) operating platform, we generate a significant amount of data that is physically impossible for individuals to track and make meaningful sense of. To address this, we overlay detailed data management and analytic systems that can process the data and use machine learning to identify potential issues when they are still small. This allows our engineers and technicians in the field to address these issues before they become safety concerns or impact efficiency or generation.
However, it is within construction that we have seen the greatest innovation recently. Through a partnership with Terabase Energy (Terabase) we are using AI on our construction sites and working together to develop AI systems. The first system we use improves how we monitor our construction projects, which is crucial because we will have approximately 12 projects under construction by the end of the year. Before our partnership with Terabase, the process was labor-intensive and time-consuming, requiring significant manual oversight in the field. Now, we utilize drones to efficiently monitor productivity and equipment on construction sites multiple times a week, allowing our team to focus on higher-value tasks. We also use a digital twin concept that overlays the as-built drawings, which show every piece of equipment on the site, so the drones can then pick up when equipment appears at those locations and perform automatic productivity counts. This enables us to see a time lapse of how the sites are being built and track the production schedule.
Drone technology
“The third aspect we are considering from an AI standpoint is the robotic installation of the modules. In the past, this work was done by a person, but as the modules have become larger and heavier (they can weigh up to 90 pounds), it now takes two or three people to install them, which has become a safety and ergonomic issue. By utilizing robotics to move the modules, we are able to undertake a significant portion of this work while improving both the safety and productivity of our construction sites.
“Finally, we are integrating AI with drone technology to perform flyovers at our operating wind, solar and storage sites. This technology can conduct infrared scans on solar sites to identify potential issues, as well as enable us to view tracker performance and detect cracks in modules. In a site that spans a thousand acres with a sea of modules, it can take a person a significant amount of time to inspect the site thoroughly. With the use of drone technology, we are able to perform a full flyover in the course of a day, which provides us with a concise map of any issues on our sites,” Jason continues.
Besides making LRE’s monitoring processes more efficient, technology plays a key role in ensuring the safety of the company’s employees while on the job. “As long-term operators and owners, we prioritize the safety of not only our own employees, but of every single person who sets foot on one of our sites. If anybody gets hurt on our sites, regardless of who they work for, it impacts our commitment to safety, which goes beyond what is required by the Occupational Safety and Health Administration (OSHA). We can have over 3,000 service providers working on our sites who are not LRE employees. By bringing all these providers under the same umbrella and partnering with the same companies repeatedly, we are able to collectively develop a safety plan and ensure that we have aligned safety cultures and expectations. This allows us to take a much longer-term view when it comes to managing safety on our sites.
“Our mantra is that if everybody does not go home in the same or better condition as when they arrived at work, we have failed as an organization, regardless of how well the site ran or how much money we made. This mindset has started to take hold with the different companies we partner with. By being hands-on in the field and asking employees what challenges they are facing, we have been able to make significant improvements. For example, the implementation of robotic installations has allowed us to shield employees from exhaustion and from the sun by providing them with a tent and fans while the robots handle the heavy assembly. Our employees appreciate this effort to improve their safety and working conditions, and we strive to inspire this attitude across all our facilities,” he ends.
By valuing long-term partnerships and investing in advanced technologies that enhance employee well-being, LRE is safely leading the way in shaping America’s sustainable energy future.