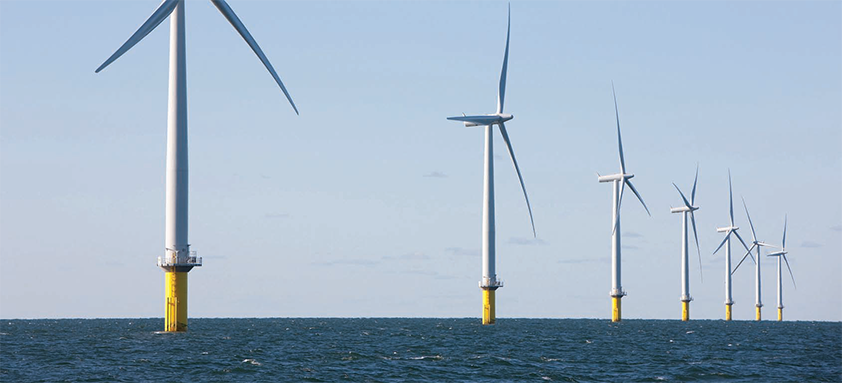
ITW Densit: Leading UHPC Innovations for Oil, Gas, and Renewable Energy
Strength and protection
For the last 30 years, ITW Densit has been delivering technical solutions based on its unique Ultra High Performance Cementitious(UHPC) products.
Marketed under the Densit® product umbrella, these solutions are applied worldwide in industrial strengthening and repair across four main sectors; renewable energy including wind, wave and tidal, wear andabrasion, industrial flooring and pavements, and oil and gas.
The Densit name itself is derived from the high density of these products, whilst the ITW moniker was added in 2012 following Illinois Tool Works’ 2007 takeover of the business. Byco-operating with its sister companies ITW Densit has seen a number of benefits from this relationship. Firstly it provides the company with global access to its market as ITW has operations based all over the world, many of which are already well connected to local industry. Furthermore, it also means ITW Densit can offer more complete solutions to its customers by drawing on the expertise of other ITW companies in materials such as polymers, adhesives and epoxies.
For its own part ITW Densit already offers amore unique scope of service than the majority of its competitors. “We combine our specialist materials with installation services in a package deal for our customers,” elaborates Thorbjørn L. Lindmark, business development manager at ITW Densit. “In comparison our competitors tend to supply either materials or installation services only. Another thing that sets us apart is our long reference list. We have carried out projects all over the world from the North Sea to the South China Sea, and proven our materials in many different conditions and environments.”
Looking at both sides of the spectrum from greenfield to brownfield projects, one notable example was a campaign of corrosion protection and structural strengthening of conductors for Shell in Brunei spanning 2006 to 2012. The aim of this work was to halt the ongoing corrosion of the conductor casing, and strengthen sections that had potentially been under attack therefore reducing the structural capacity. Turning to another part of ITW Densit’s market, on the 19th October 2012 the company completed its work on the London Array project – currently the largest offshore wind farm in the world. This project entailed the offshore and onshore grouting of 175 wind turbines and two offshore substation foundations.
On both of these projects the company utilised its Ducorit UHPC product, which has been especially developed for demanding grouting applications. As such it is well suited to the oil and gas industry for use in structural subsea and well integrity solutions, and renewable energy markets. “Ducorit has been used for offshore wind foundations since that industry began,” describes Thorbjørn. “It has also been used for large high voltage substations, which are often jacket-like structures, and this is where there is a clear parallel to the oil and gas sector. For that market we have done some platform installation projects and quite a lot of upgrades, as well as strengthening works. Because we pump our material with no welding or hazardous processes required, production can continue whilst we carry out the installation, which minimises downtime for operators.”
In terms of the material itself Ducorit offers a number of advantages over the ordinary Portland cement which is often employed in the oil and gas industry. “Ducorit has a fast development time, offering outstanding fatigue and compressive strength properties once set. The material itself has a very low water content of only around six to seven per cent. This water is completely consumed within the mixing process, which means there is no free water in the final product and very little air. This obviously contributes to the high density of the product.
“Ducorit also offers protection against corrosion, such as chemicals, acids and chlorides penetrating the material. This is particularly important for well integrity applications where we can use our material to top up between the inner and outer casings of a corroded conductor for example, and extend the lifetime of the well,” he continues.
These properties are gained from the composition of the material, which consists of four main elements. The first is a special grade of finely ground cement, which is currently only available in Aalborg. This acts as the binding material and also contributes to the main compressive strength of the Ducorit once set. This is mixed with even smaller microsilica particles, which helps to increase the density of the material. The final product also contains a superplasticiser, an artificial material developed in the 1970s, which makes it more fluid for handling, and an aggregate such as quartz sand to gain specific required properties.
Despite having achieved so much already with Ducorit, and its other existing products, ITW Densit is continuing to push further with an aggressive programme for the development of new materials. The company has already achieved increasingly lower temperature limits for its UHPC products going from ten °C to five, and now just one °C. This means that ITW Densit can work in all but freezing conditions, and year round in most offshore areas of the world.
“One aspect we are pursuing at the moment is to try and achieve an even faster strength development time. This will mean that the client can utilise the asset even sooner than is possible now. It also means that we are less dependent on weather windows when working offshore where a 40 or 48 hour window is very different to a 72 hour one. This also increases uptime and presents opportunities for faster installation,” highlights Thorbjørn. “These directions are based on customer requests from main contractors, and dialogue also with some of the major utility companies and operators. We always develop new solutions using an outside-in approach. By gaining intelligence from the market we can use this to fuel our development. Another example of this is the actual equipment we use to complete the works. There is a growing demand for faster installation so we need to achieve higher pumping and mixing rates accordingly. Therefore we have doubled the size of our bags, meaning that in the same amount of time we can double the flow of material, as well as upgraded the size of our mixers,” he continues.
Although the biggest areas of ITW Densit’s business at present are wind, and flooring and pavements, the oil and gas side is fast growing. In accordance with this, the company’s oil and gas division was moved from Malaysia to ITW Densit’s head office in Aalborg, Denmark. This enables ITW Densit to better utilise the research and development capability of its other divisions to provide the best possible solutions into the industry. It also offers greater transparency, and more efficient customer service worldwide.
“One interesting thing we see is that although everything we do is produced in Aalborg, and concrete is an extremely heavy material to ship, our customers still see the value in purchasing our solutions for use worldwide. With our oil and gas offices previously located in Malaysia a lot of our references, and experience, were gained in the Asia Pacific region. Today we are looking a lot closer to home and focusing on markets such as the British and Norwegian sectors of the North Sea,” notes Thorbjørn.
ITW Densit is confident about its ability to tap into these areas in the light of the stricter demands of both operators and certification authorities. This means that project contractors have to look towards higher performance and quality materials in order to meet these. “There is a growing acceptance that solutions such as ours can actually assist in saving on other materials. Essentially if you have a connection or foundation that is built out of ordinary Portland cement then you will need greater quantities, and usually also more steel, to reach the same strength capabilities as our products. The market is realising that our materials offer a much greater value proposition, and therefore the scope for these in the market looks very strong,” concludes Thorbjørn.
ITW Densit
Products: Ultra High Performance Cementitious products