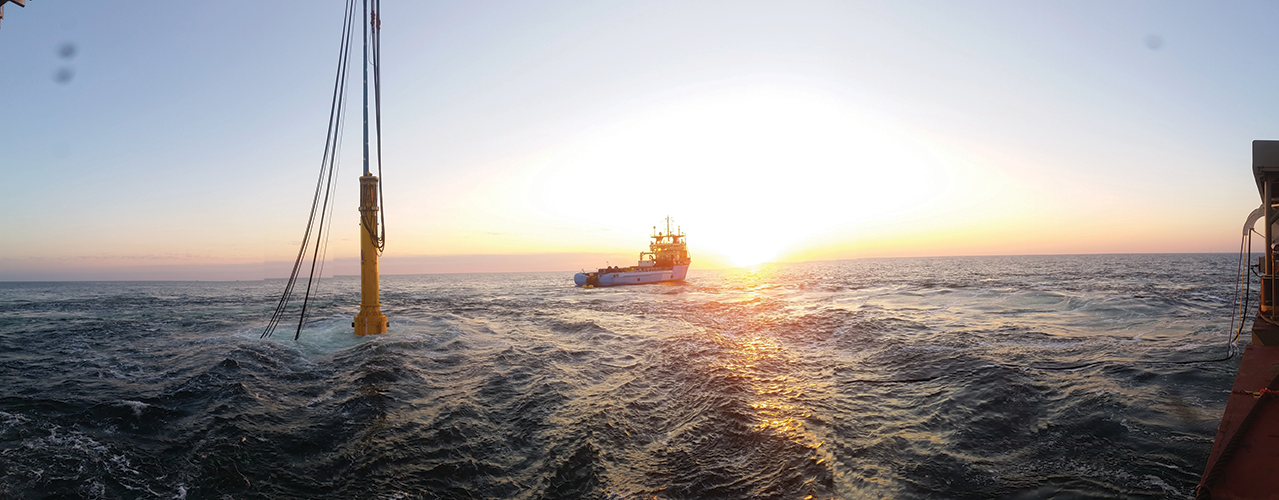
Large Diameter Drilling Ltd
A template for the future
Large Diameter Drilling Ltd (LDD) is a global provider of marine foundation solutions. With expertise spanning across nearshore and offshore industries, its team is passionate about providing the best solutions for each project. Through the company’s engineering and contracting track record, it has reached an established position as a leader in the delivery of marine foundation solutions across the globe. The expertise and passion to solve problems drives it to design, build, manufacture and operate a range of equipment to meet project specific challenges. Its teams’ focus is getting it right first time, on time, every time.
The core strength of LDD comes from the quality of its design and engineering team, something that has been an essential part of the business from the very beginning. This has manifested in recent developments, which senior contracts manager Mark Richards discussed: “To make construction of offshore wind turbine foundations more efficient and to lower the overall cost, an installation method was conceived where foundation piles were installed in the seabed in advance of the delivery of the jacket structure.” The previous method implemented among the subsea industry was by laying the jacket on the seabed and then pinning it with foundation piles. However, the accuracy required for three or four piles placement makes it a precarious challenge, and one that has to be achieved in deep water.
LDD has managed to find a solution to this, and Mark shed some light on the advancement: “Working closely with our client Offshore Windforce, LDD developed a pre-piling template (PPT) that comprises a large steel space frame, with four pile guide towers. In each of the guide towers we use hydraulically controlled guide rollers to control pile position and verticality very accurately. The rollers are powered and controlled by subsea hydraulic power packs, which in turn are controlled via umbilical from a programmable logic controller (PLC) based interface in a control cabin on the deck of the vessel. The PPT is lowered towards the seabed, placed in the correct orientation, and then set down. The system then levels the PPT using powerful hydraulic rams, controlled using input from sensitive inclinometers. Once the PPT is level, the four foundation piles are placed in the guide sleeves, using a range of survey and hydraulic ram sensors to control the accuracy of the driving. To mitigate noise each guide tower is fitted with pipework that distributes air into the water column, this generates a curtain of bubbles which helps dissipate the noise.” The next stage once all the piles have been driven in is to remove the frame and reuse it.
The PPT was designed to help one specific client of LDD but it is hoped that the concept will be utilised for many others in the future. Mark presented some of the key strengths of using this method: “It has a proven track record in installing these multiple pile arrays within very tight tolerance, reliably and efficiently. The systems we designed have a high level of redundancy built in and this has meant that the PPT has operated reliably in the very harsh subsea environment over a large number of cycles.” There are promising results from the field so far, which Mark explained: “Operations are going well, more than 50 per cent of the jacket foundation piles have been installed and post installation survey shows them to be within tolerance. This has been confirmed recently by the installation of the first jacket into the piles we installed, without a hitch. Our crew offshore is supporting the operation and maintaining the system throughout the fieldworks.” The success of this will be further developed as the company works on the three-slot version of the PPT for triangular jacket structures.
LDD collaborated with other Acteon companies in order to fully achieve this, which Mark was able to shed some light on: “Our sister company UTEC NCS Survey worked closely with us from the start to deliver an accurate, reliable and user friendly survey system which works with the hydraulics, control and instrumentation system on the PPT. MENCK GmbH provided two MHU1200 hydraulic impact hammers to drive the foundation piles and systems for noise mitigation.”
The company has also benefited from a longstanding relationship with Armada Group. It is a key local supplier to LDD, and is on hand to provide mobilisation of hydraulic driven devices. Like LDD, Armada Group recognises the need for regular travel to Rotterdam in order to advertise technical capabilities to Dutch contractors, which are considered to be some of the best in the world for the sector. Mark praised the relationship between the two companies: “They support us in our job – designing and supplying the hydraulic mechanisms and fittings that we require for the complex frames we produce. The Armada group is very attentive to our needs, and quick to respond, which is very important to the finished result.”
The future of LDD looks bright – it has clearly invested with a focus on research and development that has resulted in breakthroughs like PPT. Whatever a company’s needs LDD has the capability to ensure the delivery of pile installations, even in difficult seabed conditions. LDD will no doubt continue to find innovative ways for the industry to progress.
Large Diameter Drilling Ltd
Services: Marine and sub-sea foundation installation