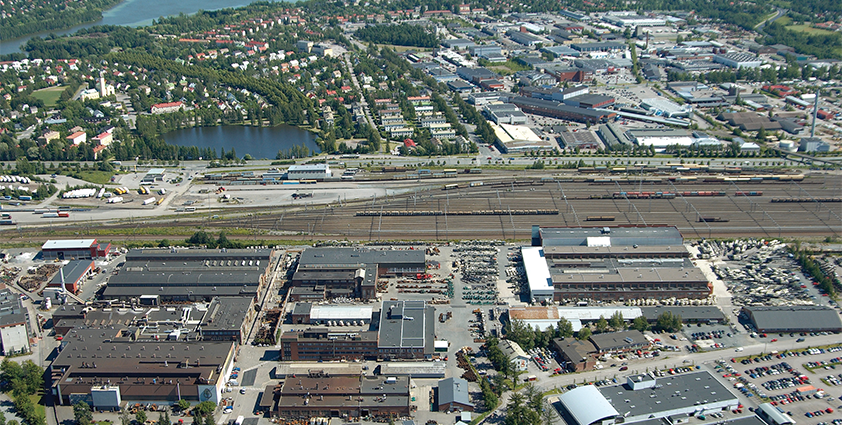
Metso EMC
The strong point
Capital investment into machinery and equipment is just the beginning of a lengthy procedure for companies in the oil and gas industry.
Every day brings increasing costs associated with maintenance, repair, upgrades and expansion whilst the processing itself requires a great deal of safety, security and reliability checks to maintain optimum quality. Metso EMC (Engineered Materials and Components), a business unit of Metso Corporation, has focused on the research and development (R&D) of products to help improve the efficiency of this process.
At its facilities in Tampere, Finland, Metso EMC engineers materials solutions for a wide variety of oil and gas industry applications to meet the demands of clients such as Shell and Saudi Aramco in countries throughout the world. With its sister company, Metso Automation, Metso EMC has introduced new materials solutions for valve components to enhance their critical properties (including strength, corrosion resistance). As the world’s fifth largest manufacturer of valves for the oil and gas sector, Metso Automation’s products are generally recognised as market leaders for demanding cryogenic, nuclear and oxygen recovery applications.
Manager for sales and marketing Jarmo Lehtonen talks about why the company has become such a success: “The key strengths of the Metso EMC business unit are materials technology competence, especially for demanding applications, and a wide range of available production technologies including castings, weld cladding and P/M HIP (powder metallurgical hot isostatic pressing). Due to the strong R&D and engineering resources we possess in conjunction with Metso Corporation, we are able to create and tailor material solutions for a wide variety of applications.” In Tampere Metso EMC employs 235 people, of whom about 40 are involved either in R&D or engineering. Its production facilities include a 12,000 tpa steel foundry with complete heat treatment, NDT and machining operations (5-axis CNC machining centers for hydroturbine parts manufacturing). It also has a well equipped material testing laboratory.
The company’s R&D involves many aspects and large financial investment. However, as the goal of Metso EMC is to support its clients in their operations, perhaps the most important element is customer and partner co-operation. It prides itself on having in-depth knowledge of its customer’s operational environments and using this understanding as a base foundation from which all development is carried out. Metso EMC also engages with universities and research institutes around the world to support this practical work with a theoretical approach.
“For the oil and gas industry the key issues in material and component deliveries are always reliability and quality,” says Jarmo. “In addition to strict manufacturing process controls this means special procedures such as corrosion, stress and fracture mechanics testing, and non-destructive testing (NDT) to guarantee long-term reliability of our items.”
The reliability of Metso EMC’s products was utilised in Shell’s Qatargas 4 offshore LNG project in 2008-2009. Non-ferrous, nickel-based super alloys, such as Inconel 625, are needed in offshore LNG process lines because of their non-magnetic material and corrosion resistance properties. On the other hand, castability of nickel-based materials like Inconel 625 is not always adequate for near net shaped components, such as big valve bodies. The P/M HIP process offered multiple benefits in manufacturing of these components:
- Refined, non-porous microstructure (no slag inclusions etc.)
- No need for separate heat treatment (HT is a part of the HIP process)
- Improved strength properties over the castings (see enclosed chart, P/M HIP vs. cast material)
In recent years one of the most promising solutions to come out of Metso EMC’s R&D is metal-to-metal, or bimetallic, materials. These have been manufactured using powder-HIP to possess incredibly high durability characteristics, meaning bimetallic components have a dramatically reduced maintenance requirement and greater lifecycle than their steel counterparts. As this is relatively new technology, the largest power-HIP bimetallic products thus far have been nine tonnes but ongoing development will see this increase to meet the same 30-tonne standards set by cast items.
One example of the bimetallic capability is in oil company Neste Oil’s oil refinery plant in Naantali, Southwestern Finland, where Metso’s materials technology know-how has been utilised to gain a significantly longer lifetime for the raiser pipe of the oil refinery cracking plant.
Naantali refinery uses a TCC (Thermofor Catalytic Cracking) process for cracking the crude oil. An integral part of the TCC process is the 78 metre high raiser pipe, which is used for the regeneration of the catalyst material. Due to the high temperature (> 600 °C) and high catalyst flow rate (~ 40 m/s) intense local erosion takes place, especially in the bottom part of the raiser pipe where turbulence is the strongest. Due to homogenous microstructure, the originally used welded claddings in the raiser tube were locally eroded after operating periods of just a few months.
Metso’s solution to the wear problem was to replace the original welded claddings with an 18 mm thick high-temperature erosion resistant coating in the inner surface of the raiser pipe. The MMC (metal matrix composite) coating is produced using the HIP (Hot Isostatic Pressing) method. The coated raiser pipe components are manufactured and delivered in four to five metre long pieces, which makes their easy assembly and on-site installation possible.
The first delivery to Neste Oil was made in 2003, and since then Metso has received four repeat orders. The lowest 20-25 metres of the raiser pipe, which is most vulnerable to wear, are now covered with Metso’s coating, and as a result the whole plant functions better.
“Our technology strategy is based on the development of three key types,” Jarmo explains. “First, material performance technology concerned with wear, corrosion, elevated temperatures, mechanical behaviour and cryogenic applications. Second, the development and engineering of materials and, third, related manufacturing technologies based on foundry and power-HIP technology, cladding, and other coating techniques. The development of bimetallic materials has reduced special emphasis in recent years because its applications in the oil and gas, mining and metallurgy industries are wide.”
Ultimately, the reason for its R&D is to enable Metso EMC’s customers to gain the most efficient solutions with the best value for money. The use of advanced engineered components means that, although the initial cost might be greater than normal, the total cost of ownership throughout its lifecycle is much lower due to fewer maintenance and repair requirements.
In 2010 Metso Corporation received almost six billion euros of new orders, a 36 per cent increase over 2009. Net sales grew 11 per cent in the same period as well, rising from 5016 million euros in 2009 to 5552 million in 2010, whilst the actual backlog of orders at the end of the year was 18 per cent up on December 2009. This equated to total operating profits before interest, taxes and amortisation of 491 million euros, nearly 100 million euros greater than the previous year.
These results came at a time when the financial crisis was biting its hardest, displaying the success of Metso Corporation’s wide-ranging abilities and products. It also puts the company in a good position for the future, allowing it to continue its development projects whilst capitalising on a regenerating world market. As Jarmo highlights, Metso EMC has plenty to keep it busy right now: “Currently we have large supply programmes for hydro-energy applications, nuclear systems and demanding valve applications, including superaustenistic and nickel-based superalloy components being used in oil and gas projects and desalination plants.”
The next few years will be unpredictable as the economy recovers, but as Jarmo previously mentions the company is already planning ahead. One such new area of interest for Metso EMC is Big Science projects, which offer interesting possibilities for European high technology companies. Using its special known how in powder metallurgy, Metso EMC supplied components for the particle accelerator of CERN’s Large Hadron Collider (LHC), which was started up in September 2008. The most important part of the multi-billion LHC project is the particle accelerator located in a 27-kilometre-long ring-shaped tunnel. Metso EMC has supplied totally ab. 2900 end covers, needed at both ends of the dipole magnets from which the accelerator is made of.
Nonetheless, the core of Metso EMC’s and Metso Corporation’s business is not only to produce new technologies but products that are of a high quality. Jarmo concludes by placing this focus at the leading edge of the company’s future: “We believe that increasing requirements for quality and, in some cases, improved performance requirements support our strategy of being the number one supplier for demanding components solutions. More demanding environmental and stress corrosion requirements, higher loads and increasing temperatures are pushing material development forwards. We intend to continue developing solutions for these needs well into the future.”
Metso EMC (Engineered Materials and Components)
Products: Special materials and components for oil & gas industry