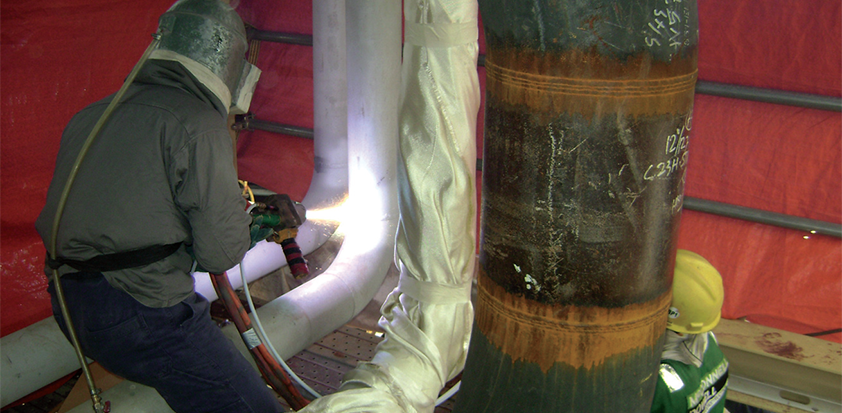
MTM Metalizing Pte Ltd
Frontline of perfection
The properties of metals such as steel means these materials have long been used in critical applications, and as such there is a need to protect these assets from external threats such as corrosion.
Although limited in the past, with the advancement of thermal spraying technology, metalizing, or the deposition of a metallic coating on a surface, has emerged as the best corrosion protection solution available.
Established as a joint venture with International Metalizing & Coating Inc (IMC) in the US, MTM Metalizing utilises IMC patented electric arc spray technology to compete in the Asian market for metalizing from its base in Singapore. The arc spray metalizing machines operated by MTM Metalizing remain manufactured by IMC in the US, and represent the state-of-the-art system for corrosion prevention. The company’s largest market sectors are the petrochemical and marine markets, although there is some crossover between the two for projects on assets such as FPSO’s.
With technology that can meet the most demanding of specifications for quality, durability, application speed, metalizing now delivers an unmatched service life with a reduced lifecycle cost and at a competitive price. In fact with deposition rates of more than 100 square metres per hour at 250 microns thickness, the system equals and exceeds airless paint systems. Likewise, any metal that can be put into wire form can be thermally sprayed offering increased flexibility, and the ability to create an instant alloy by applying different metals at the same time.
General manager, Bill Jordan explains how metalizing fits amongst the traditional methods of corrosion protection: “There are two main ways of protecting against corrosion currently employed in the market. The first is a barrier coating, which is essentially something similar to a paint, which serves to stop oxygen and electrolytes such as water reaching and corroding the steel. The second is a form of cathodic protection, which can be either an anode or a type of impressed current. At MTM Metalizing we are spraying up to 99.5 per cent pure zinc or aluminium, and as both materials are anodic, they offer the best of both worlds with the benefits of barrier and cathodic coatings.
“The reasoning behind the use of thermal spray coatings is due to the much longer life they provide compared to traditional coatings, particularly on assets that are subject to adverse conditions like high temperature or salt spray, where a thermal spray coating may last up to 50 years. As well as zinc and aluminium we can also spray metals like copper nickel Inconel and stainless steel. Some customers have requirements to use these types of alloys on their structures as this enables them to get the surface properties of one metal in combination with the material properties of a second,” he continues.
The latest advancements in IMC’s application technology means that MTM Metalizing is no longer restricted to coating in blasting and spraying chambers, but can also undertake spraying work on site, and even whilst certain structures are still operational. As the benefits of modern metalizing become more widely recognised, MTM Metalizing is also seeing an increase in specification for this type of technology from clients.
“A lot of it depends upon whether you take a short or long term view,” notes Bill. “Major multinational players such as Exxon and Shell are quite active in their uptake of thermally sprayed aluminium (TSA) for significant assets such as refineries and process plants which are intended to be operational for many decades, and therefore require the best possible protection. Similarly, operators like Petrobras are specifying this technology for their FPSO’s in order to reduce the repair and maintenance requirements for these assets in the field.
“One good example in the petrochemical industry is the challenge of corrosion under insulation, which can be seen in pipes and vessels where moisture gets under the insulation and causes corrosion. This can eat through the pipe and potentially cause catastrophic consequences, yet it is difficult and expensive to inspect. As such, a lot of oil companies have taken the step with corrosion under insulation programmes going on, and they see the value of investing in top quality processes, which means they don’t have to check the pipe for 20 or more years,” he elaborates.
As well as encouraging oil companies to take a more long-term view towards corrosion protection and consider the life cycle costs of using a process such as metalizing, MTM Metalizing’s other challenge is the shift of some projects to fast-growing areas like China. Despite this, the importance of Asia in terms of the petrochemical market means that the company still sees favourable opportunities in its home market, and surrounding areas. “Australia is a market of interest due to the huge amount of LNG and other projects coming on stream, and China continues to be significant going forwards despite the relatively fragmented nature of its marketplace with over 1000 individual shipyards.
“A major target of the business is to move into Korea, as in the past Singapore was a leader in the construction of FPSOs, but now we see the Korean market absorbing some of that work. There are already some companies offering TSA in Korea, but we see this as being a nice market for us to bring our expertise and superior equipment into,” concludes Bill.
MTM Metalizing Pte Ltd
Services: Metalizing