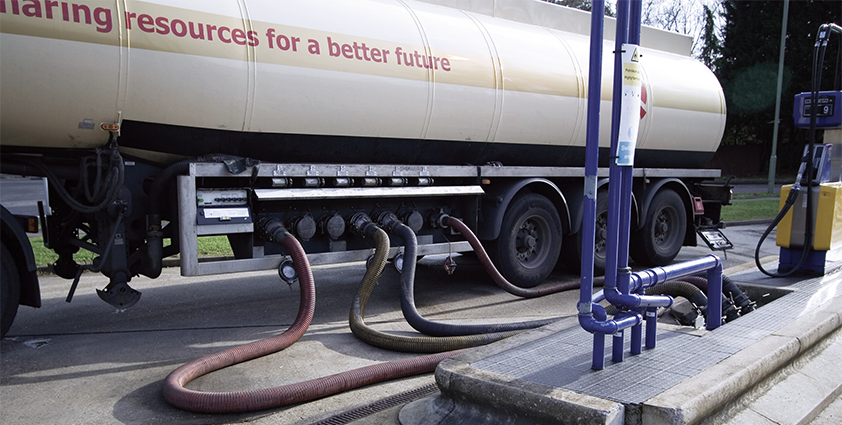
Optimize Service Station Supply with Implico’s OpenTAS RDM System
Timing is the decisive factor
Efficient service station replenishment thanks to integrated software
The biggest challenge to deal with when supplying service stations with oil products is timing. When deliveries are made too early, then valuable logistic resources are squandered. But when deliveries are made too late, the service station will have insufficient supplies and the relevant gas pumps need to be closed. On the market there are many IT subsystems promising to cover the individual aspects of service station supply. This leads to patchwork solutions, which are very complex to implement. They have high maintenance costs and, above all, are inflexible.
The solution is an integrated complete system that covers all the production steps of service station replenishment. Implico offers exactly such a system: OpenTAS RDM (Replenishment & Delivery Management). It maps the overall process chain, from order acceptance, to route planning and supply to invoicing; highly automated, fast, secure, flexible and with low maintenance. OpenTAS RDM offers all the functionalities to optimise and automate the complete service station supply.
Order management (ASR)
Orders placed on time, ensure on time delivery. Order timing and volume depend on available stocks and forecasted sales. Thanks to its integrated approach, OpenTAS RDM offers the flexibility and accuracy required for effective order management.
Manual order taking is still very common. The service station tenant controls the stocks and orders by phone. But when it comes to automatic order taking OpenTAS really plays on its strengths; the integrated OpenTAS ASR functionality (Automatic Stock Replenishment) is exceptional. The module runs as a background service, continuously monitoring the service station inventories and sales, ready to recalculate or generate orders.
Based on the stocks available the ASR module can calculate when, at a certain prior sale, the stocks will be depleted. Its high prognosis security is achieved by referring a multitude of historical data. Included here for example are actual previous sales. OpenTAS ASR takes into account site-specific sales profiles, including fluctuations by time of the day, as well as special events like public holidays and sitespecific events like road works or special promotions. Thanks to all this information the system can calculate the optimal and most efficient point in time for a new order. This guarantees a highly reliable sales forecast and a best in class order accuracy and flexibility. The resulting orders are immediately visualised in the Truck Dispatch Workbench, ready to be scheduled.
Planning & optimisation (TDW)
Whether the order is manually entered or automatically conveyed from the OpenTAS ASR module, the key challenge for delivery planning and optimisation is to find a cost-effective balance between demand and available resources. The TDW functionality (Truck Dispatch Workbench) offers the ideal system support for efficient delivery. Thanks to its advanced optimisation algorithms, and by making best use of the ASR order flexibility, OpenTAS TDW minimises the cost impact by always choosing the best split load partner(s). Calculations show that companies using OpenTAS managed to improve their drop-rates, reaching values that competitors can only dream of.
Delivery planning needs to meet two key customer targets: cost efficiency and customer service level. But it also needs to be accurate to ensure it can be executed as planned. OpenTAS RDM provides a real-time solution, allowing the user to adjust the plan based on the latest information like recalculated ASR orders or updated truck availability. This results in an accurate delivery plan and minimises process issues like product returns, product runouts or invoicing errors. The TDW module always keeps the overview, and allows pro-active course correction before issues occur. It gives the user full visibility, real-time accuracy and maximum responsiveness.
Execution (PDA)
The route plan generated by OpenTAS TDW is transmitted to the driver’s PDA. In this way the driver gets his detailed trip instructions as well as an overview of other upcoming trips. The system offers the customer maximum visibility of the trip execution process. The control center is always informed about the truck status and activities. Thanks to the PDA connection, the dispatcher knows when the driver starts, when he reaches which depot or service station etc. These PDA status feedbacks are visualised in the Truck Dispatch Workbench, allowing a timely adjustment of the plan e.g. in case a truck is delayed in traffic. If starting or unloading takes longer than planned, the plan is changed immediately. Like this the disposition is always informed in a timely manner, when for example an additional vehicle is needed.
Reconciliation and reporting
During the OpenTAS trip reconciliation process, load and delivery data are checked, matched comand completed before sending them into the ERP business workflow. Standard reports are provided via the OpenTAS report engine; additional customer specific reports can be created. The results are provided in real-time and in various formats.
Conclusion
OpenTAS RDM is specifically designed for managing the complete service station supply chain. This advanced end-to-end solution is different from any other product on the market because it seamlessly integrates and automates the full process, always providing the user with real-time visibility based on the latest information. The system reacts immediately to changes and adjusts the orders to meet real-time changes – highly flexible and therewith always in time. This results in higher performance and quality, and minimises logistic cost.
Service station replenishment of Coop Mineraloel
Significant oil companies, especially in Europe, are already successfully working with the Implico solution. One of the first was Coop Mineraloel AG (CMA) in Switzerland. CMA assigned Implico with the integration of all the logistical processes concerning the gas station supply into one system, including merchandising and supply of oil products. The company operates around 165 service stations in Switzerland, with a strong upwards trend. “With the introduction of SAP and OpenTAS, we have achieved a level of automation for the business processes that enables us to further pursue our growth within the service station market.” This is the positive verdict of Walter Eberle, director of CMA.
Supply of 330 service stations
Implico was chosen to implement SAP and OpenTAS at Topaz, integrating 330 service stations and five depots. Topaz is Ireland’s biggest Fuel Supplier with the largest network for services stations in the country. The project was finished in the second quarter 2010. Topaz opted for the following OpenTAS functionalities: depot integration, inventory management, route planning with OpenTAS TDW and reconciliation. However, the decisive factor for choosing OpenTAS was among other the detailed tank truck- and compartment planning function of OpenTAS TDW.
Implico
Contact
Berit Huyke, Implico
Phone: +49 (0)40 / 27 09 36-0
Fax: 040 / 27 09 36 – 46
Email: berit.huyke@implico.com