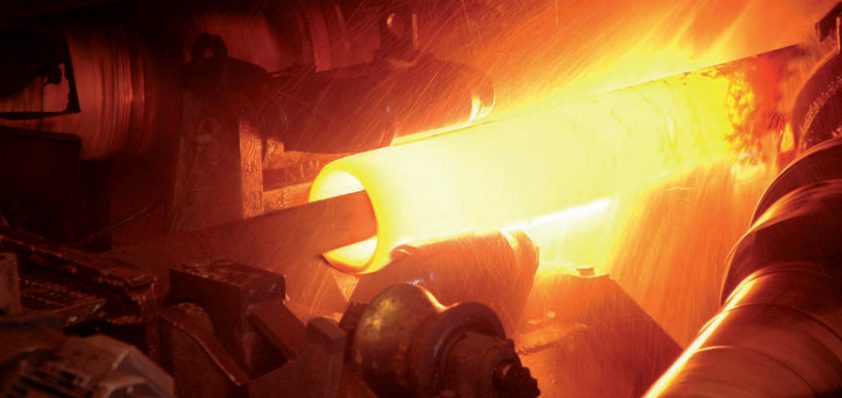
Ovako
The specialists
The Ovako name is built upon a long heritage of Nordic steel production knowhow, with the forerunners to the business today having been founded over 300 years ago
Over the last century in particular the structure of the business has changed significantly, but always with a focus on the production of high quality products led through its head office Sweden. During these years the long steel products were consolidated through a number of companies, three of which were broughttogether in 2005 by their respective owners to create the current Ovako Group. Then in 2010 the business was acquired by private equity investor Triton and refocused to three main product lines – bar, bright bar, and tube and ring products.
Through all products bearing steel manufacturing and components has been a key application, and these customers remain an important segment of the business today. The Group is also utilising the same capabilities of its steel production to target more high demand sectors such as mining, automotive and oil and gas. Having been more active in the oil and gas sector in the 1980s and 90s, Ovako is now strongly re-entering this market with both its tube and ring, and bar products.
“Our belief is that the combination of very good steel and our tube and ring rolling capability means that we have the ability to tap into markets that are of interest to our potential customers,” begins Björn Olsson, vice president of marketing and sales in the tube and ring division. “Based upon recent tragic incidents in the oil and gas field, there is a much higher focus on quality products, and we believe we can contribute to those clients looking for demanding specifications from their steel materials. Likewise, as the industry moves into harsher conditions offshore and into deeper and colder areas of the world, we see that our steels fit many of those requirements for reliability and safety.”
Part of the reason why the company positions itself alongside these high demands so well is that quality, in both its products and processes, is already deeply rooted in the business. Ovako is not a high volume or bulk product manufacturer, but a specialist in niche product areas and special applications. Furthermore, the business maintains its own steel production built upon a knowledge of steel attained over the course of three centuries, which not only offers the flexibility of a complete in-house manufacturing process, but also enables Ovako to develop steel for specific specialist applications.
Elaborating on one such area Björn says: “For many years we have been working on ultra-clean steels, the top end of which is the isotropic quality. It is the cleanliness of the steel that is one of the main contributors to good performance in rough conditions. You can then add whatever alloys are required to produce qualities such as hardness, but it is the actual base steel matrix that determines performance. This is what we focus on, and therefore we avoid non-metallic inclusions as much as possible, utilising those that we have to in a controlled way to create these isotropic qualities. Aside from the ultra-clean range, we are also able to optimise other parameters through our in-house steel sources as we have a number of different metallurgies within the Group.”
Today Ovako Tube & Ring is investing substantially in the modernisation of its tube mill in Hofors, as part of a continuation of an earlier investment made in 2007 to expand its size range. The business is now taking this further in order to improve its processing and ensure greater efficiency in the rolling sequence. “By increasing efficiency we will be able to become more active in the market with a better capability to reach market prices as they stand today,” explains Björn.
“As a more niche producer, we do not have the equipment to produce high volume, and therefore lower cost, items. Therefore we have to identify other ways in which we can maximise our operations, such as through the design of our own process equipment. Having been creating tubes in our plants since the early 1900s, we have a long history of tube rolling knowledge, which we use to develop technologies that specifically benefit our operations. A lot of commercially available equipment is based on greenfield units, which does not necessarily complement our set-up. By modernising our mill continuously over the years we have utilised our resources in the best possible way,” he adds.
As well as improvements in efficiency, the modernisation will enable Ovako Tube & Ring to offer tubes of a slightly smaller diameter than it does today. With the tube mill remaining operational during the programme, the works have had to be carefully planned to best take advantages of the summer shut down periods in gaining access to the whole mill, without disrupting production. Investments have also been made into other areas of the division including the opening of a new ring rolling plant at the same Hofors site in 2010, and further works to construct another ring rolling unit to begin operating in 2013. This will see Ovako Tube & Ring’s size range drastically rise from three-metre diameter to four-metres, something the company believes may boost its offering to the world’s energy markets.
Indeed, global energy demands are booming, and therefore Ovako is keen to contribute towards this with its knowledge and expertise of steel products. With the market still relatively unstable at present, the company is taking advantage of the opportunity to tap into new customers and capabilities in those areas where its offering may be of benefit. As one part of this, the oil and gas industry is certainly a market of great interest to the Group as a whole over the next few years.
Ovako
Products: Long special steel products