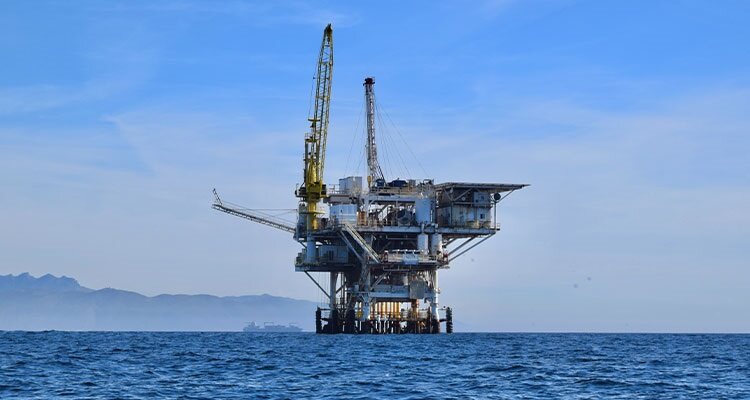
Paving the way for safer and more efficient operations in oil and gas By Al Rivero
Among many of the challenges that oil and gas operator companies face to maintain high production levels and continue lowering the manufacturing cost of end products, lifting price has become the primary driver.
With locations that have harsh environmental conditions and areas that put staff and equipment at high stress levels and as well as a relatively significant influx of new talents in the pool, the conditions are set for the need to augment operations with stable and reliable support technology. As a result, we are seeing the proliferation of drones and robots to assist with inspection and rounds, as well as increased tablets and augmented reality to support remote fieldwork. All these new advances in support technology also require a more robust infrastructure to uphold the higher bandwidth requirements.
Operators have turned to a variety of technologies to back these initiatives, and address the challenges faced in oilfields and plants. The key to unlocking actual operational gains and safety is accessing real-time data and analytics as part of a fully integrated solution for each site.

Relieving the stress on workers
Operations are situated in remote locations, far from average support teams, and can be challenging to reach when help and support are needed. Ultimately, this leads to costly shutdowns and safety risks, which amount to losses of almost $38 million to $88 million annually for oil and gas companies.
The explosion of new technologies and automation has provided companies with alternative options to increase productivity, while preserving worker safety from afar. Already playing a massive role in the sector, it is predicted that these will have a major impact in the future. System sensors, instruments, and equipment are connected. They can provide a full-spectrum perspective that increases visibility and real-time insights into identifying disturbances and site monitoring of equipment, vehicles, and staff constantly on the move.
Operators have also introduced autonomous systems to undertake dangerous and mundane tasks to remove the risk of injuries and fatalities. The discrete sensing capabilities of these solutions allow them to monitor and inspect hazardous industrial equipment and identify maintenance needs more accurately, relieving workers of stress and fatigue by completely removing them from the situation. This also frees workers up for tasks requiring much more skillful thought and attention. More intelligence is provided for informed decision-making thanks to the new data made available by the Industrial Internet of Things (IIoT) and robotics.
The greatest challenge in supporting autonomous solutions is connecting them for real-time optimization and complete visibility. To achieve and maintain peak productivity and efficiency, mission-critical applications must run on a communications network that offers reliable, agile, and adaptable connectivity that can thrive in diverse, evolving, mobility-driven environments. A wireless network operating in some of the world’s most hostile environments cannot afford downtime.
Achieving consistent wireless coverage
A remote and rugged terrain needs constant observation. This can cause issues with achieving a consistent network connection, as the core environment of an oil or gas production site can be unpredictable and often isolated. As a result of implementing more technology on-site, an enormous volume of data is produced by devices that enhance oil recovery and improve production. Effectively managing this data will become even more critical as the industry moves towards unmanned facilities.
A high-capacity wireless network that supports reliable, real-time data delivery to and from the array of onboard sensors within these autonomous systems is paramount. It can aid in the precise diagnosis of equipment problems and provide efficient fixes. Advanced wireless mesh networks are unique in delivering consistent, reliable coverage across any space, regardless of the environment’s size, topography, physical obstacles, radio frequency traffic, and weather conditions.
Operators often experience difficulties securing a reliable connection by conventional means, such as deploying Long-Term Evolution (LTE) or 5G technology. Public cellular networks often need more reliability, availability, latency, and security than mission-critical services in oil and gas require. As some mobile devices lack infrastructure capabilities, they can only connect to one access point at a time. This means that if an access point fails, all communication nodes connected to that access point are disconnected from the network, making all access points a potential risk for operational shutdown.
A mesh network comprising several nodes automatically transmits data via the fastest and most stable paths. Mesh networks can easily scale up and down quickly by adding or removing nodes. The data traveling across the web can be seamlessly rerouted depending on the bandwidth needs, signal strength, or competing traffic. Having a network with machine-to-machine connectivity is a huge bonus. With each mobile asset equipped with a node, the mobile robots remain connected to the network, with no dropouts experienced.
Unwavering connectivity
Each asset has an unwavering connection with real-time functions, such as remote monitoring and enhanced video security, always enabled, allowing for maximized production and safety on an oil rig or gas production site. By utilizing and installing wireless network technology in the hazardous environments of a robust production site, operators can achieve continuous connectivity for the entire plant and expand the range of activities its personnel can undertake.
For a list of the sources used in this article, please contact the editor.
Al Rivero
www.rajant.com
Al Rivero is VP of Sales (Global Energy) at Rajant Corporation, the broadband communications technology company that invented Kinetic Mesh® networking, BreadCrumb® wireless nodes, and InstaMesh® networking software. With Rajant, customers can rapidly deploy a highly adaptable and scalable network that leverages the power of real-time data to deliver on-demand, mission-critical business intelligence.