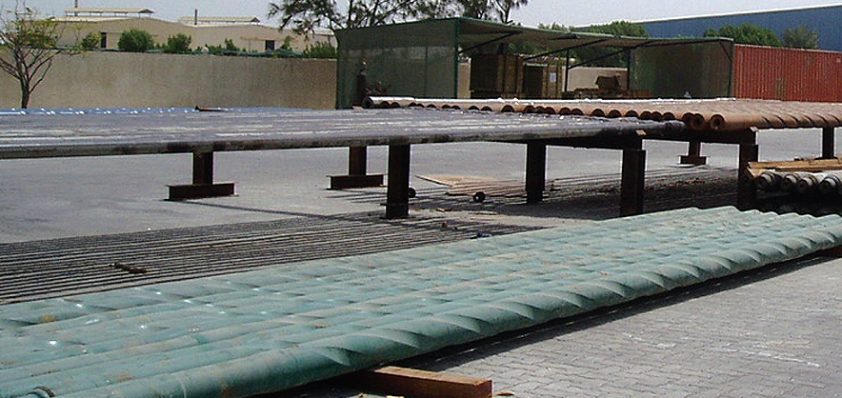
Protools
Tools of engagement
Protools, also known as Hunt Oiltool International Industrial Company L.L.C., is the leading provider of drill stem technology to oil and gas companies in the Middle East.
Located in Abu Dhabi, with consultation centres across the region, the company was created in 1997. The Emirates Al-Badie Group, also located in the UAE, owns 51 per cent of the business, with the remaining 49 per cent owned by the Norwegian company Habu Holding AS. Protools has established itself as a total provider of finding, developing, and managing the distribution of oil tools to major organisations operating in the region.
The quality of the company’s tooling design has been strengthened by the fact that it is the only major provider of drill stem equipment in the Middle East, and also by the comprehensive nature of its after-sales, support and servicing networks. Protools’ mission is to meet all the requirements of a company’s tool designs, even if this means creating a totally new piece of technology based on the blueprints and drawings of an operator’s development team. The business aims at providing these bespoke solutions rapidly, and at a competitive price incomparison to the market. To maintain the mutual trust it fosters with clients, Protools has concentrated on the total life-cycle (TLC) costs in the manufacturing and repair of drill stem products. To this end, the company has developed a Total Competence Centre, which focuses on manufacturing products that have guaranteed long-term strength and reliability.
To illustrate the popularity of Protools’ products and equipment, it is important to look at the companies it counts as satisfied clients. The organisation continues to provide drill stem solutions to the Abu Dhabi National Drilling Company, KCA Deutag, Weatherford UAE and Yemen, Noble Drilling, Odfjell Well Services, Egyptian Drilling Company, Baker Inteq, Yemen Drilling, and many other businesses with offices operating in the Middle East.
Protools is accredited to a number of quality standards, most notably ISO 9001 and 14001, API Specification Q1, and OHSAS 18001, as well as holding a Tenaris NKK License, and being a Certified ARNCO 300 XTTM Hard-bander.
The company receives all of its raw steel that it uses in creating its products from Ascometal in France. This allows Protools to complete a range of services at its site in the UAE that are designed to help the petroleum industry improve efficiency and increase productivity. The organisation’s commitment to the TLC of its equipment means that it has a comprehensive range of maintenance and repair services. These include both dismantling and mantling, cleaning, straightening, testing, welding, hardbanding, and repairing torque connections.
These services can be applied to all of the technology Protools creates at its factory. The business specialises in manufacturing equipment designed closely to a client’s specifications, to turn their vision into a reality. For example, Protools make a quality range of both slick and spiral drill collars, made from modified steel. The slick model has a normal rolled steel surface, whereas the spiral version is designed to allow mud to circulate around the drill collar body to prevent sticking. Equally, Protools is a renowned producer of Kellys, made from selected bars of chromium molybdenum alloy steel, which has been specially formulated for drilling tools. These Kellys come in both square and hexagonal forms, specific to a customer’s needs.
The company’s product development team has also manufactured a large range of heavy weight drill pipe solutions. Protools conventional range of drill pipes has one wear pad for different sticking circumstances – and this means that the pipe is best applied to vertical holes. The Tri- Spiral range is designed for high angle drilling, and has characteristics that reduce torque and drag, as well as increasing buckling resistance. For rougher drilling environments, the company has created the rigid Spiral Wate range of drill pipes that are more adapted to the top of the drilling collar, and are ideal for weight transmissions. Equally, the Wiper Wate design has a better cutting removal function in the horizontal section, which improves the performance when drilling at different directions.
Alongside the various heavy weight drill pipes produced by Protools, there is also the option for the manufacturing of short radius drill pipes. These are produced from bars of steel or aluminium, and range between 30 and 31 feet in length. Aluminium is available as an optional material as it has a better performance in regards to fatigue. However, this makes it sensitive to catalytic corrosion, meaning that the pH level of the surrounding mud must be controlled at the location. As the pipes are lighter, rotary torque is greatly reduced, in addition to an overall better resistance to buckling, and increased sliding performance. The organisation has also created two unique types of drill stem subs: lift subs are manufactured from materials that are heat-treated and machined to the exact specifications of the drill collar it will be joined to, and rotary subs have a protected layer of phosphate coating to minimise galling on the initial installation process.
The Protools research and development team has also been progressing the designs of its casing scraper technology. This equipment removes all mill scale, burrs, cement sheath, mud cake and foreign matter from inside the wall of the casing, which forms a smooth and clean surface for the proper seating of packers. The width of the scraping blade is arranged so that the tool scrapes a complete 360 degrees of the casing as it is lowered into the well. Protools’ casing scraper can be described as a two row, six blade tool, and it is the simplest and most rugged scraper designed throughout the history of drilling in the oil and gas industry.
Protools is planning to embark on an extended period of growth within the oil and gas industry on an international scale. The company applies its comprehensive knowledge of the market’s drill stem needs to offer a total package to its clients, which includes an extensive aftersales programme. Protools’ emphasis on working closely with customers to develop a solution that meets their exact requirements has consolidated its already firm position in the offshore tooling market sector.
Protools
Service Drill stem technology