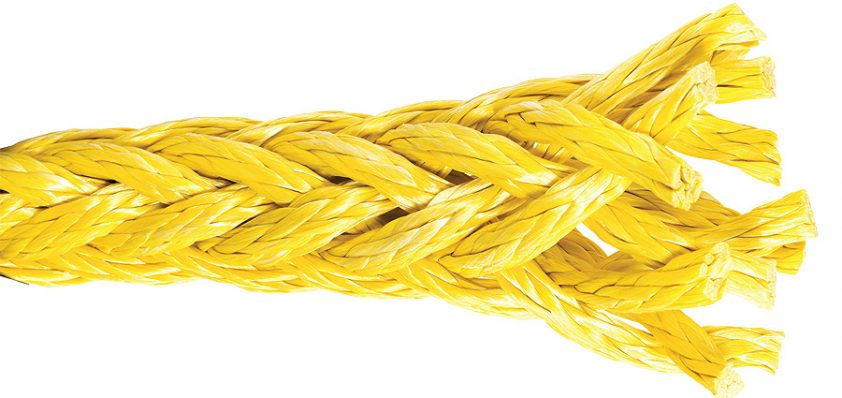
Puget Sound Rope
Full of fibre
Puget Sound Rope is a market leading business specialising in the development and manufacture of high performance synthetic fibre ropes used in the most demanding applications.
The company’s patented Plasma and BOB ropes offer strength equal to steel wire size for size, yet is 90 per cent lighter, providing considerable advantages and ideally suiting the current trend for ultra deepwater operations in harsh environments.
“Puget Sound Rope (PSR) forms part of The Cortland Companies, a diverse group of businesses focused on the development, manufacture and sales of high performance market-leading products,” says Sam Bull, vice president of The Cortland Companies. “The group produces a vast range of products including hydraulic/electrical umbilicals, fibre optic cables, electrical cables, synthetic fibre ropes and strength members. Our technology covers a wide range of industry sectors; including aerospace, medical, offshore oil and gas, seismic and ROV applications. Our broad technical capabilities and manufacturing diversity puts us in a unique position to offer solutions for the demanding needs of deep water operations”
Sam elaborates on Puget Sound Rope: “We see PSR as a rope manufacturer with a difference. Despite being a relatively small business, in recent years it has been at the forefront of developing and manufacturing unique, high performance fibre rope solutions. These offer considerable advantages over more traditional steel wire products, especially in deep and ultra deep water applications, where the self weight of steel wire seriously diminishes the effective payload weight.”
Through continuous development of innovative rope solutions, the company aims to demonstrate the importance of such products to the industry: “The key driver for us is to gain full market acceptance of fibre rope, particularly for the offshore deepwater lifting market,” continues Sam, explaining the advantage of fibre ropes in comparison to more traditional steel wire ropes. “The major limitation of steel rope is the selfweight of the steel. This becomes a serious problem, both in limitations on manufacturing and transportation and the impact on payload capacity when used in deep water. Fibre ropes are virtually weightless in water and can be fabricated to any size and length.
“Another less obvious advantage is the impact on vessel size and power requirements,” he says. “For example, a 125Te payload in 3000 m of water the steel wire lift line alone would weigh 200Te in air, whereas the fibre lift line would weigh 20Te. Correspondingly an active heave compensated winch with steel would consume 4.5Mwatt compared to 1.8Mwatt for fibre.”
PSR’s Plasma fibre is based on Honeywell’s Spectra HMPE (High Molecular weight PolyEthylene) material. The process involves realigning the molecular structure of the Spectra under a combination of precisely controlled tension whilst the fibre is immersed in a pressurised liquid bath at elevated temperatures. The resulting Plasma fibre is an ultra strong, robust, low stretch lightweight rope. BOB (Braid Optimised for Bending) is a blend of HMPE and LCP (Liquid Crystal Polymer) Vectra fibres that provides excellent long-term creep resistance and superior cyclic fatigue performance, particularly in bend-over-sheave applications. Both ropes come in 12 strand, and 12×12 strand constructions.
These fibre options, together with the unique patented design of the 12×12 construction, make it one of the world’s leading fibre ropes for dynamic applications: “The 12×12 takes 12, 12 strand ropes and braids them together, producing a totally torque neutral rope that is very easy to splice and repair,” Sam explains.
The 12×12 construction offers other important attributes, especially when working in deep water. “Importantly, the rope can be made in any length needed – in theory we could make a rope that reaches to the moon without the need for bulky end to end splices,” Sam enthuses. “Furthermore the design of the rope makes it very easy to inspect, repair and PSR regularly trains vessel crews to splice in the field. This is a huge advantage to our customers. For example, if a steel rope breaks or is damaged during an offshore operation the entire rope must be discarded and a new one used. Where as a fibre rope can be quickly cut and spliced together by any of the trained crewmembers on board. This saves the customer considerable amounts of money in terms of carrying spares, and in vessel downtime.”
PSR recognised in the early stages of development that without a suitable winch system designed to work with the fibre rope the chances of gaining market acceptance was extremely slim. In 2002 PSR teamed with ODIM AS in Norway to develop a suitable solution and a joint industry project was established with the remit of building and demonstrating a FRDS (Fibre Rope Handling System). This resulted in the development of the ODIM ‘CTCU’ (Cable Traction Control Unit). The acceptance of the CTCU and BOB lift line followed three years of intense development and testing of both the fibre rope and the winch.
The CTCU traction unit consists of individually driven sheaves specifically designed to handle the rope’s frictional and load elongation properties. The system was subjected to extensive factory and barge testing in a local fjord culminating with a successful field demonstration pilot project at the Ormen Lange gas Field in Norway during 2005 proving the technology for offshore applications.
The effectiveness of PSR rope designs has been proven in a number of important projects and has been successfully used in many record breaking and challenging operations. This includes salvage work on the SS Persia sunk in 3000m water depths and recently the BOB rope in conjunction with the ODIM CTCU was used by Subsea 7 to complete their installation contract on the Independence Hub in the Gulf of Mexico. “The Independence Hub work was an extremely important project for us to participate in,” says Sam. “It was the first real, major offshore oil and gas development project to use a fibre rope traction winch and synthetic ropes as the lifting line and represents the true dawn of market acceptance for this technology.”
The Independence Hub work required the installation of over 100 items in water depths in excess of 2500 metres. The ODIM CTCU system loaded with 3500 m of 56 mm 12×12 BOB rope was mobilised on the SS7 offshore construction vessel the Toisa Perseus in September 2006. The range of lifting tasks planned included the installation of mudmats, lowering and stabbing of umbilicals, installation of spool pieces, manifolds, jumpers and a subsea tree. To date the system has been extremely successful, both in completing the assigned tasks and in demonstrating the combined capabilities of the CTCU and BOB rope solution and has completed over 170 lifting operations.
Reflecting on the achievements of the company and the successful application of its products Sam is confident that Puget Sound will be at the forefront of synthetic rope technology for many years: “Fibre rope offers many advantages over traditional steel wire. In recent years our focus has been on improving the performance of our products and demonstrating their capabilities. We will continue to build industry confidence in these solutions with the aim of gaining full market acceptance in the future.”
Puget Sound Rope
Industry: High performance fibre ropes