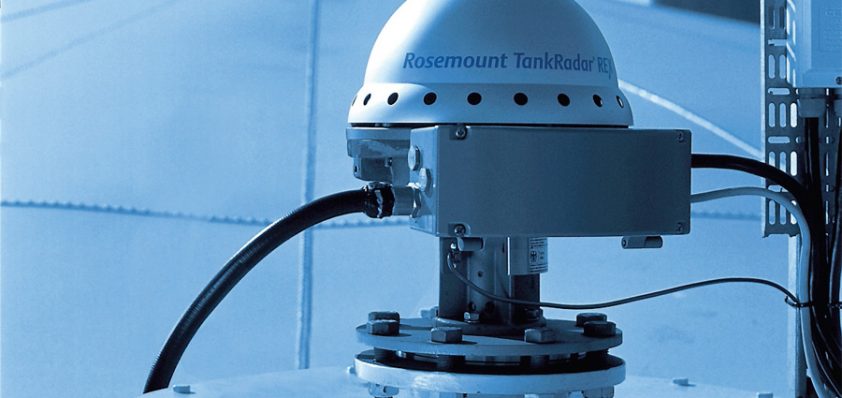
Rosemount Tank Radar
Safety first
As with all operations in the oil and gas and process industries, the safety of both the facilities and operating personnel are the paramount concern for companies worldwide.
This is no more apparent than in bulk liquid handling plants and processing facilities, where the safety integrity level (SIL) requirements according to the IEC 61511 standard are rapidly becoming the common framework for the improvement of safety standards. At these sites, the chief danger lies in the accidental overfill, and subsequent explosion of handling tanks. Rosemount Tank Radar, an Emerson company, manufactures advanced radar level gauging technologies to protect against these dangers.
A major factor behind the attention towards such safety issues was the Buncefield incident, which occurred on December 11th 2005. The Buncefield Terminal was one of the largest in the UK, and a strategic part of the fuel supply for the south of England. The incident, which resulted in an explosion that inflicted major damage to the surrounding area and injured 40 people, was caused by a tank being overfilled and the subsequent vapour that escaped combusting. The investigation into the accident revealed that the mechanical tank gauge fitted to the tank failed to indicate that the gasoline level was rising as the tank was filled, and also the independent Hi-Hi level switch failed to trigger the warning alarm.
As a result of this incident, an investigation board issued a set of recommendations that not only applied to facilities such as Buncefield, but to a wider range of sites that are exposed to the risks of fire and explosion. Chief among these recommendations was the need for all facilities worldwide to develop and work to a common methodology for assessing SIL requirements in tank plant operation and design in accordance with IEC 61511. This is a safety standard, entitled ‘Functional safety – Safety instrumented systems for the process industry sector’.
Essentially, IEC 61511 sets out rules of good practice in the engineering and design of systems that ensure the safety of an industrial process through the use of instrumentation. It has two key concepts – the safety life cycle, and safety integrity level – that are essential. The former is used to evaluate the risks in a specific process, whilst the latter is a measurement of performance required for a safety instrumented function.
To protect against further incidents like Buncefield, and in accordance with the guidelines set out in IEC 61511, operators and equipment manufacturers are developing and using advanced automatic tank gauges (ATGs) to protect against overfill of storage tanks. Traditionally, ATGs have been used in large storage tanks for a number of applications, including inventory management, custody transfer, operational control when filling or emptying tanks, and loss control and oil movement calculations. Furthermore, when operating as part of a plant’s overall safety system, ATGs are connected to alarms to give warning of critical situations.
Rosemount Tank Radar is the world’s leading developer and manufacturer of advanced radar based tank gauging technology. Since its establishment the business has pioneered the use of ATG systems, delivering its first TankRadar for tankers in 1976. Today it employs approximately 440 people, and has successfully delivered more than 100,000 TankRadar gauges.
The company’s excellence in proven radar technology, combined with its unique attention to its customers needs, has seen it set the industry standard for reliable, accurate and maintenance-free tank level gauging for all applications. As a leader in its field, the business works closely with all of the major oil companies on a worldwide basis, and has been responsible for many world firsts including the first ever radar technique for level gauging, and the first radar technique for custody transfer calculations.
The Rosemount TankRadar Rex RTG 3900 radar-based ATG product is one of the few in the world that meets the demanding requirements of the IEC 61511 standard. Chief among these requirements is the ability to perform a failure modes, effect and diagnostics analysis (FMEDA), where failure rates, safe failure fraction and other parameters are calculated for use in the design calculations. The safe failure fraction is a percentage measurement of the fraction of failures that lead to a safe state, and the fraction that will be detected by diagnostic measures and result in a defined safety action. A reasonable requirement for modern ATG systems is a safe failure fraction of at least 80 per cent.
The TankRadar Rex RTG 3900 is specifically designed for refineries, tank terminals and the petrochemical industry, and is one of the most accurate systems for custody transfer, process control, inventory control, and filling tanks without the risk of overflow. Available with a wide range of antennas for different applications, the system measures to a precision of 0.5 millimetres and can be fully integrated into existing systems.
Radar tank gauging technology has been the accepted standard since the early 1980s, with the first high accuracy radar for land based application in storage tanks being delivered in 1984. Since then, the market share for radar gauges has increased continuously, and is today well over 50 per cent.
There are a number of benefits of radar technology, all of which combine to make a highly efficient and accurate system. Chiefly, the key driver is that radar gauges are renowned for their higher measuring reliability and accuracy. Also, whereas standard servo type gauges require moving parts that are in contact with the contents of the tank, radar technology has no moving parts and does not need to come into direct contact with the substance being measured.
Another success factor of radar technology, in particular the Rosemount RTG 3900, is the ability to easily integrate the product into older, existing systems. For example, the RTG 3900 can use the currently installed fieldbus by emulating a gauge supplied by the original system vendor. This makes itpossible to replace old mechanical or servo gauges with modern Rosemount 3900 gauges without the need to replace any field cabling or master system software.
Overall, the introduction of radar gauging equipment, combined with the standards and methodologies setup by IEC 61511 has vastly improved the safety levels at processing plants worldwide. The contribution of Rosemount cannot be underestimated, with the business leading the way in the development of the latest technology and ensuring that the highest safety standards will remain for the coming years.
Rosemount Tank Radar
Services Radar systems