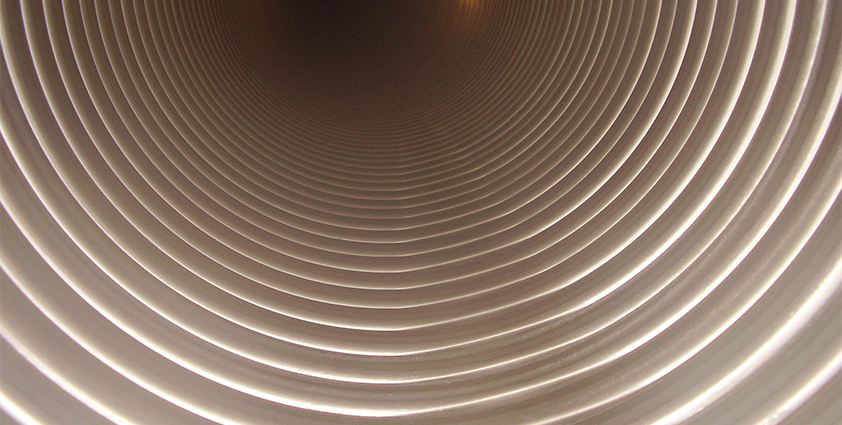
Safeclean
A clean sweep
In 2009, Overflateteknikk and Avfallsteknikk merged to form Safeclean. The two companies previously worked in the offshore market – Overflateteknikk dealt with cleaning of offshore production facilities, while Avfallsteknikk provided waste management services to the oil companies.
Combining expertise in these two related fields, the merger allowed the new company to offer a complete maintenance and cleaning service, including the disposal of waste. Based in Høyanger, on the westcoast of Norway, Safeclean employs 25 people to operate the waste treatment plant at its base in Høyanger and to serve the offshore cleaning market.
The merger allowed the company to facilitate additional services to a much larger market, since it now offers treatment services in Høyanger for equipment used onshore. The main focus for Safeclean is still its cleaning services to offshore production facilities. Jon Refsnes, managing director of Safeclean, elaborates: “Our service involves the removal of different types of hydrocarbons and scale; we especially focus on the hard parts of the scale. To begin with, we provided our services solely to smaller offshore projects, but we are now moving into treating much larger systems, such as an entire offshore production unit. As we involve waste management solutions in our portfolio, we provide a truly unique service. This year we have treated the whole production plant at the Statoil Hydro Oseberg C platform. We are now discussing treating all the equipment from the well area until the export system in one operation, saving time and money. Such a comprehensive operation has not been carried out before.”
The company uses its own made chemicals and equipment in the cleaning operations. “This is one of our greatest strengths,” explains Jon. “We have formulated chemicals that are perfect for our operations. Our clients know that we are experienced in the development of chemicals and equipment and that when we provide our services, they are based on the long experience of personnel from each company, in their own specific areas.
“Offering a tailored solution means the company can work very closely with its customers. We are now able to work directly with the operators. We have a specific focus in the market, which is to treat low radioactive types of scales (NORM). Our main strength is definitely that after we have cleaned the equipment, we can bring the waste onshore and take care of the waste by reducing the amount of hazardous waste to a minimum.”
He goes on to describe the company’s treatment of NORM waste: “Up until now this has been carried out through mechanical operations. This is especially the case when cleaning separators, which traditionally have been cleaned manually. We run a cleaning in place (CIP) process, which allows us to get the equipment 100 per cent clean by only using CIP-technology without doing any manual work on the items.”
In terms of efficiency, the company is focusing on streamlining its operations, both to increase the quality of its services and provide cost savings to clients, and to improve health and safety for its employees. An efficient business is a safe one. Jon elaborates: “The main goal for us also in the future is to achieve sufficient levels of health and safety for our employees and those of the companies that work with us. If we improve our efficiency and can achieve a completely clean surface that will mean a longer time until maintenance is required the next time.
“Focusing on the competence of our people and working systematically with our quality assurance system is ensuring that we can improve our services for the customer. We have also got quality accreditation assigned by the Norwegian government that states that we are fully equipped to clean enclosed systems.”
Implementing these more efficient processes, Safeclean carried out a major project for oil giant, StatoilHydro. “That project was a particularly important achievement for us, because we cleaned the whole process plant in one operation carried out in only three days. This fast turnaround time meant that we could provide StatoilHydro with a big saving in terms of time and also the low number of people involved in the process, which in turn cuts cost and leads to improved efficiency.
“We see many opportunities for our new concepts in the industry because nearly every one of the current installations encounters or will encounter a set of typical problems, especially in terms of scale issues in produced water systems. There are also problems with heavier hydrocarbons and so we see a huge market in that area. As there has also been a particular focus on the NORM waste area within the oil and gas sector, there are discussions going on in Norway of reducing the level of classification. This will mean that nearly all the equipment will need to have undergone thorough cleaning before it can be brought back onshore.”
Looking to the future, Jon forecasts a strong future for Safeclean as he explains: “We are continuously working to develop new methods, both on the chemical side and in terms of new equipment and processes. We want to be a main player in the onshore arena, and to take care of all the equipment, which is coming onshore. In addition to this we aim to treat the offshore systems on different oil platforms. We know that UK platforms have a problem in terms of scale created by produced oil/water, and I think it will be interesting for us to enter the UK market.”
Safeclean
Services: Cleaning and maintenance