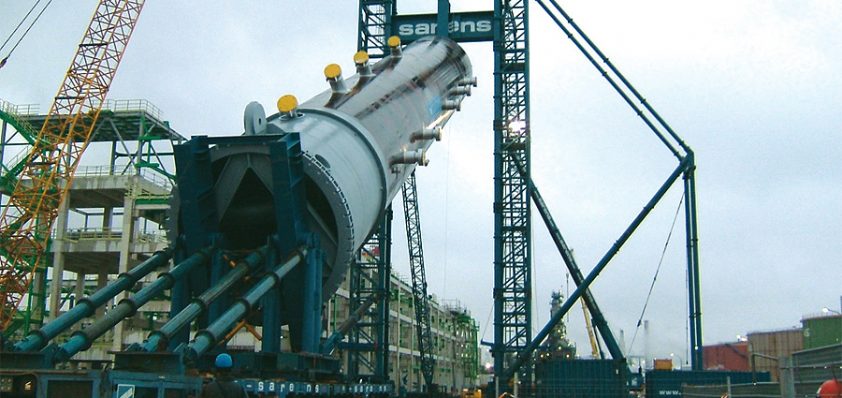
Sarens UK Ltd
Reaching new heights
No major petro-chemical operation can be completed without the use of state-of-the-art heavy lift cranes and associated equipment.
Sarens UK Ltd, a division of the Sarens Group, is among the industry’s leading heavy lift companies, operating with major oil and gas clients around the globe. The company has a fleet of 20 cranes capable of lifting up to 2000 tonnes, and a large number of selfpropelled modular trailers (SMPTs).
Paul Weston, project manager at Sarens UK believes that the company’s reputation in the industry is a key factor in its success: “Sarens UK originates from the old heavy crane division of Grayston, White and Sparrow, which was the largest crane hire company in the UK. Throughout our history we have built up a reputation that is second-to-none, with a safety record to match. We pride ourselves on being honest with our clients and giving them an excellent service.
“The petro-chemical industry is our forte, and is where the bulk of the very heavy lifts take place today,” Paul explains. “We have completed work for many of the major industry players, including Esso, BP, Shell, Texaco and Mobil. Additionally, in many of the contracts that we undertake in a refinery we do not work directly with the refinery, but rather with a company that manages projects for them. We work with clients around the world, but at present the bulk of the large heavy lift projects are in the Middle East and the Far East.”
The company offers an extensive fleet of stateof- the-art cranes, capable of meeting the most demanding requirements of oil and gas customers: “All of our cranes are purchased by Sarens, we get new models continually, and we are presently investing heavily in crawler cranes,” says Paul. “Our current crawler crane fleet is capable of lifting up to 1200 tonnes, and is in operation around the world, including Europe and the South Pacific. Additionally, our telescopic fleet comprises of 500 tonne, and 800 to 1000 tonne cranes, which operate for customers all over the world.
“Our range of lattice jib cranes is capable of lifting between 500 and 2000 tonnes,” he continues. “The 2000 tonne crane is currently engaged in a project in Kazakhstan, which is nearing completion. The operation consists of a major refinery build for a joint venture client called PFD, who are working for Chevron Oil on behalf of the Kazakhstan government. The project is worth more than $20 million, and we have around 65 people and a number of large, and small cranes at the site.”
Paul explains that there is a great demand for cranes throughout the industry at present: “The new cranes that we receive are going straight to work at the moment, they are each used for many months at a time, and we currently have full order books for a number of them. For example, when the PC9600 crane has completed the project in Kazakhstan it is going to Thailand to undertake some heavy lifts, of around 350 tonnes in a refinery, before going on to a nuclear plant in Finland for a 17-month project.”
Together with cranes, Sarens UK operates a number of self-propelled modular trailers (SMPTs): ‘We have over 500 SMPTs, which are trailers that are not driven, but rather the operator walks alongside with an umbilical and an operating panel to automatically control them,” Paul comments. “They can steer in any direction, with the wheels capable of turning through 360 degrees, they are self-propelled and self-steering, and can be joined together depending upon the weight you need to carry. The heaviest item that we have lifted with them is around 14,000 tonnes, which cannot be lifted with more traditional trailers.”
The nature of the projects undertaken by Sarens’ cranes means that safe working practices are essential: “Everything that we do has to be done safely, and in every part of our operations there are potential problems,” says Paul. “There is a great deal of work that has to go into any job before the actual lifts. We operate a fully equipped engineering drawing office with an up to date CAD system producing fully engineered rigging studies of all major lifts on a project. For example, if we go to a refinery to lift one 500 tonne vessel into place we may have to complete as many as 80 lifts before it in rigging the crane, and putting on the ballast and the jib sections. Each stage is planned to perfection, and all of our employees are trained and re-trained regularly.”
Paul explains that transportation costs continue to present a challenge to the business: “A great deal of our costs are taken up by transporting the cranes. When we move the 2000 tonne unit there can be up to 100 wagons accompanying it carrying up to 1000 tonnes of superlift ballast, and around 400 tonnes of ballast on the crane itself. The shipping of the cranes is very expensive, and we regularly find that around half of the total price of a mobilisation is spent on transport.”
Despite this, Paul is confident that Sarens UK can maintain its reputation as one of the leading heavy crane suppliers to the oil and gas industry, and can continue to expand: “I believe that we can continue to work internationally and increase our fleet, whilst maintaining our high standards and the reputation of our services. There is a lot of expansion in the industry at the moment, and these jobs require heavy lift cranes, so the future looks very good for us,” he concludes.
Sarens UK Ltd
www.sarens.co.uk