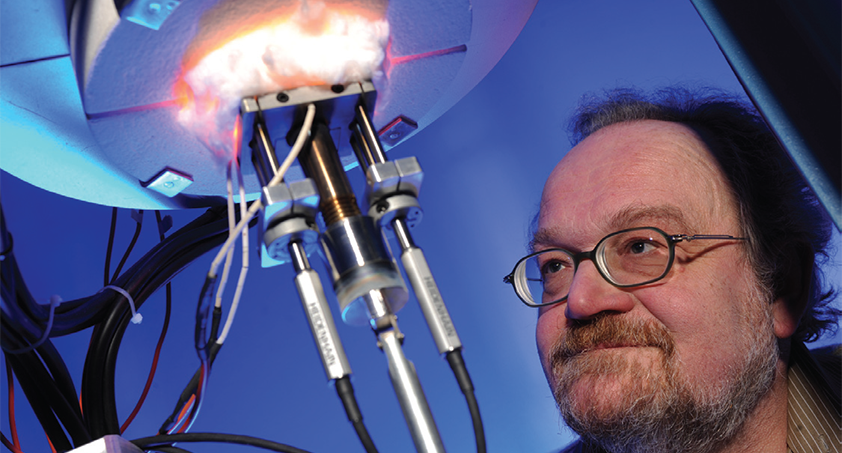
Schmidt + Clemens Group
Allied to the market
For more than 130 years the name Schmidt + Clemens (S+C) has been associated with first-class specialist steel solutions, particularly the production of high alloy tubes and components for petrochemical applications.
Now into its fourth-generation, S+C remains a family run and-owned company but has expanded outside of its headquarters in Germany to operate a portfolio of eight production companies worldwide. This includes sites in Brazil, Spain, Malaysia, Saudi Arabia, Czech Republic, and the UK, which gives S+C the largest production capacity in its market.
The S+C group has a worldwide reputation as a manufacturer of static castings as well as centrifugally cast tubes and components for the petrochemical and chemical industries. Feedstock materials, which are produced in the petrochemical industry from crude oil and natural gas, are experiencing increasing demand worldwide as raw materials for further development in the chemical industry. As a result petrochemical companies have to increase their efficiency, meaning that furnaces now operate at over 1000°C and under high pressure.
“S+C has achieved its status as market leader through innovations in its special alloy product lines and continuous developments in centri-casting technology,” explains Ursula Petrat, corporate director of business development. “We work closely with customers to gain a better understanding of their problems, then we evaluate what their technical needs are and provide a solution. Our role today goes beyond just producing tubes as we consider ourselves as a solutions provider in terms of helping the customer achieve their objectives more efficiently.
“S+C is famous for its pre- and after-sales service where we offer advice on material selection associated with process gains, detailed design support, and input on modifications, essentially to improve the value delivered to the customer. We want to help customers achieve the promised benefits by combining their strength in terms of their understanding of their industry, requirements and technologies with our technical and process knowledge,” she continues.
This approach has also seen the company achieve a reputation for rapid response and replacement of tubes and components in the case of emergency deliveries. This year alone S+C has assisted four customers with such requirements, helping them get their plant back on track quickly. This ability stems from the company’s worldwide production network, which can pool manufacturing capacity when required to rapidly deliver in an emergency scenario. S+C has also branched into installation services at the behest of its customers. This includes supply, fabrication, installation, inspection and commissioning from one source for equipment such as radiant coils for crackers or reforming plants.
The real strength of S+C though lies within its research and development (R&D) capability. With the highest R&D budget within the industry, the company is continuously improving and inventing new alloys to address customers needs. Coil material is rigorously tested within its pilot plant, a unique asset in the industry, where the alloy is tested under real-life conditions to ensure performance.
S+C’s market has slightly different demands, which the company then caters for in its alloy selection. For example, the ethylene sector is looking for higher operating temperature, extended run length of the tube so it requires less maintenance and longer coil life which equates to more output. “In response we have developed new alloys like Centralloy HT-E, with inherent anti coking properties, a unique material for steam cracking furnaces, as it forms a protective oxide layer which is unaffected during cracking and de-coking cycles. Centralloy HT-E is designed for use at unprecedented high operating temperatures,” describes Ursula.
So far this year S+C has introduced two new products to its portfolio including Centralloy G45Mo, which it considers to be well suited to the oil and gas market due to its mechanical and corrosion resistant properties. “This new alloy has excellent resistance to a multitude of corrosive media under both oxidising and reducing conditions,” confirms Ursula. “It has resistance to pitting and crevice corrosion, mineral acids like nitric as well as sulphur and acid mixtures, and contaminated mineral acids, so it really has superior strength against all different corrosive media. At the moment we have utilised it in geothermal applications, but we see it as ideal for oil and gas activities due to the harsher operating environments and the increased prevalence of sour gas. As such, we think that the corrosion resistant alloys we produce will be used more and more in this market.”
Having strongly established itself in the petrochemical market, S+C is looking evermore at branching into the oil and gas sector where it sees the opportunity for corrosion resistant centrifugally cast tubes in applications like flowlines, umbilical’s and manifolds. “This industry does not currently use a lot of centrifugally cast material but we believe that in harsh and sour environments these robust products offer economical lifecycle costs,” enthuses Ursula. “There is a lot of cladded pipe material in the oil and gas market and we would like to introduce solid corrosion resistant alloys like Duplex stainless steel, and nickel based materials, where applicable, to add value.
“One of the other advantages of our production process is that we can manufacture all dimensions of tubes and to very tight tolerances of diameter and wall thickness. The centrifugal casting process also has a very low propensity to internal defects in the wall of the pipe as the forces remove the impurities. Perhaps of greatest interest though is that there has been no failure of centrifugal cast pipes in service to date, which creates a strong argument for their use in safety and process critical applications,” she concludes.
Schmidt + Clemens Group
Products: Specialist steels and components