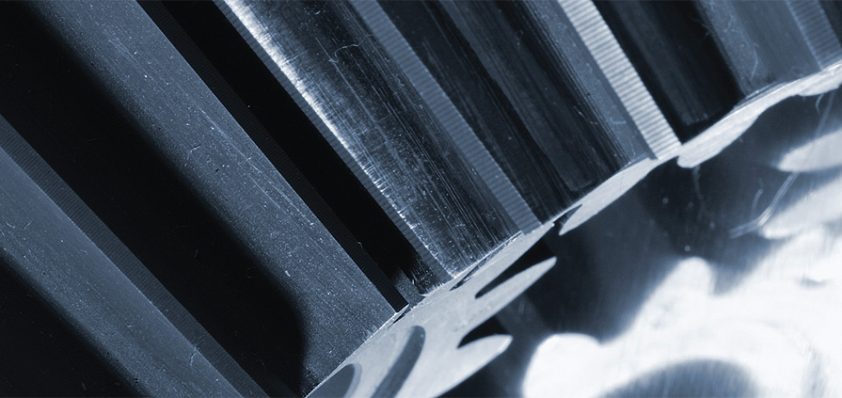
Stork Gears and Services
Geared for growth
As an integral part of the technical services division of Stork NV, Stork Gears and Services is a specialist repair company that boasts a significant amount of experience in the field of gearboxes and gear technology.
Since its formation, the company has proven its credentials in the manufacture, repair and modification of gearboxes for a range of clients in numerous industry sectors. As well as the apparent quality of its products, the business has also acquired a reputation for short turn round times for even the most complex of projects, and a group of employees with undoubted industry know-how.
As a result, Stork’s client portfolio is impressive in terms of calibre and size. Having been the chosen repair and maintenance operator for several original equipment manufacturers (OEMs) for many decades, the company has attracted prominent customers in a number of market segments. These include wind and energy, FPSO, petrochemical industry and offshore, shipping and dredging, the steel industry and storage and transhipment companies. To illustrate further, Dubai Drydocks, Bergsen AS, SBM and Bluewater Energy service make up some of the organisation’s maritime customers, while bluechip names such as E-on, Shell and Corus are important industrial sector clientele.
As an independent repair company, the organisation’s skilled staff have become accustomed to overhauling a wide variety of gearboxes and related drive types. Given the nature of the market sectors that the company is active in, the need for fast response times and minimal downtime costs is prominent. This is recognised through gearbox support that is offered on a 24 hours a day basis, with staff working in continuous shifts, seven days a week.
The repair procedure begins when the company receives a service request from an offshore supply vessel that has suffered severe onboard gearbox damage. Within 48 hours of the request, a qualified engineer from Stork will have visited the site to determine the degree of damage, the general size of the job in hand, as well as the approximate cost. By the fourth day the damaged parts of the gearbox are transported to Stork’s workshop, which is fully equipped with state-of-the-art equipment and innovative tools.
Within eight days of the service request, the gearbox will have been carefully dismantled, at which time Stork’s service department will determine its overall condition. An inspection report is then compiled alongside a thorough damage analysis, which is sent to the customer together with a quotation and repair advice. The fifth step, which is completed within a month of the initial damage, is the gearbox repair and manufacturing or purchasing of spare parts. Once the product is fully assembled, it undergoes a series of thorough tests to ensure it complies with high, internationally recognised standards. The complete gearbox and full documentation is then handed over. The whole process usually takes no more than 40 days; if that seems like a lengthy amount of time then consider that the average construction time for a brand new OEM-built gearbox is eleven months.
Of equal importance is the ability to pinpoint potential failure or gearbox damage in the first place – it is one that Stork has displayed in abundance. Root cause failure analysis is a key identifier of gearbox problems and prevents future problems and downtime issues. Oil and vibration analysis are combined with visual diagnosis, and are usually used to monitor plant machinery and to control the causes of machine failure.
Gearbox lubrication is also key to the condition of the product and to maximising its lifetime potential. While it may seem like an obvious concept, a great deal of gear and bearing problems are directly linked to contaminated or insufficient oil. Detailed analysis is particularly important in the search for wear modes and the uncovering of potential lubrication problems. The use of vibration analysis is also a trusted method of determining the condition of gears, bearings and the causes of machine failure. Stork’s on-site tests detect a variety of potentially hazardous defects, including abrasions, alignment anomalies, looseness and areas of resonance.
A further element to the company’s impressive product and service offering is the production of gearboxes for maritime and industrial applications. Stork prides itself on its knowledge as an OEM at the highest level by developing new gearboxes, which utilise cutting-edge technologies. After a client has passed on its requirements, the company’s engineers discuss design and appropriate calculations. Production drawings are then made, from which the gearbox is developed. This expertise, which has been executed on countless occasions, enables Stork to design, manufacture and deliver what are arguably the finest gearboxes on the market within a period of just three months.
The various areas of capability that are afforded to clients are carried out by specialist segments of the company, which encompasses service, machine, gear cutting and laser cladding departments. This depth of know-how, combined with a proven track record in satisfying the most demanding of customers, has seen Stork secure a leading position in its sector – one in which it is likely to stay for many years to come.
Stork Gears & Services
Services Gearbox repair, maintenance and production