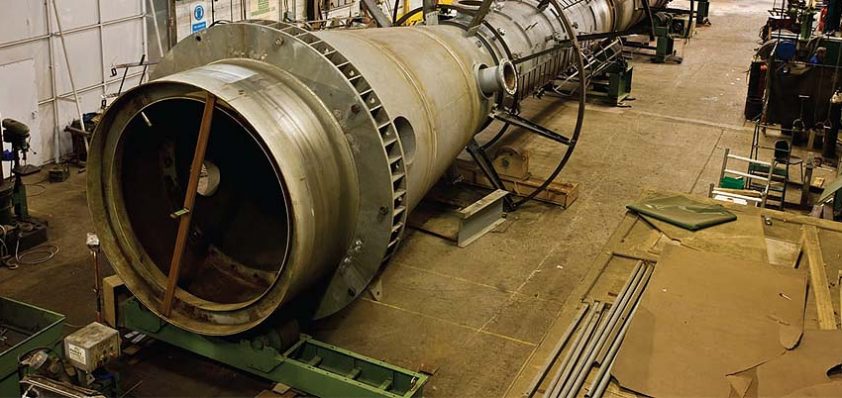
The Evolution of Radley Engineering Ltd: From to Present
Engineering opportunities
Radley Engineering Ltd was founded in 1972 by brothers John and Thomas Radley in Dungarvan, Co. Waterford. Today, Radley Engineering Ltd employs 255 people, and is one of Europe’s leading specialists in the design, manufacture, fabrication and site installation of high quality stainless steel, carbon steel and exotic materials.
Vision, mission and value proposition:
The company’s vision is to be a leading global provider of specialised engineering solutions that will bring value to its clients.
The success of Radley Engineering has been driven by a set of core values:
- Safety – The safety and health of all employees is the most important value held by the company and will never be compromised.
- Integrity – The company will behave ethically, honestly and will work together to achieve organisational goals. It will honour its commitments and accept responsibility for its actions.
- Environment – A commitment to sustainability and to acting in an environmentally friendly way.
- Teamwork – it works to inspire, support and assist each other’s efforts towards individual and shared goals.
- Respect – It treats individuals with respect and sensitivity and values their contribution.
- Performance – It is dedicated to satisfying its customers’ needs and exceeding their expectations.
Greg Conaty, Technical Director, outlines the companies’ value proposition to their clients: “At Radley’s we create value for our clients by playing a key role in transforming ideas and inventions into innovations that, by definition, create value for all our customers and supply chain partners. Our market sectors include Oil & Gas, Mechanical, Pharmaceutical, Bio Pharma, Power Generation and Special Architectural Projects.”
Greg goes on to outline the Radley Engineering Ltd mission statement:
- To safely and consistently deliver specialised engineering solutions for its targeted market sectors.
- To deliver a high quality, comprehensive, professional service and take full responsibility for the realisation of customers’ investment plans.
- It will deliver operational excellence in every corner of the organisation and meet or exceed its commitment to the communities it serves.
- It is dedicated to creating an atmosphere of optimism, teamwork, creativity, resourcefulness and its dealings with everyone will be conducted in an open and ethical manner.
- All of its long-term strategies and short term actions will be moulded by a set of core values that are shared by each and every employee.
Site Facility:
The state-of-the-art site facility, in Dungarvan, is set against the backdrop of the Comeragh Mountains on a ten-acre site that consists of:
- Carbon Steel Pipework Fabrication – Dedicated 2,000 Sq. Metre workshop c/w 4 overhead gantries.
- Stainless Steel Pipework Fabrication – Dedicated 1,400 Sq. Metre segregated compound for pipe & fittings.
- High Purity Pipework facility – Dedicated 2,000 Sq. Metre Cleanroom to ISO Class 10/1000/10,000 servicing the pharma, bio pharma and medical market sectors.
Radley’s purpose built facility is also capable of:
- Welding (Automatic & Manual Processes)
- Machining
- Polishing
- De-Greasing & Cleaning
- Passivation
- Shot Blasting & Priming
- Painting & Powder Coating
- Heat Treatment
- NDE
- Vessel Repair & Refurbishment
Products include:
- Pressure Vessels
- Subsea Drilling Risers (Approved/Qualified welding procedures)
- Storage/Heating/Cooling Tanks
- Pipework Systems and Installations
- Heat Exchangers
- Condensers
- Reactors
- Process Columns
- Modular Design for Skids & Structures
Subsea Drilling Risers:
Radley Engineering Ltd continues to invest in new technologies and welding techniques. This commitment to research and continuous improvement has resulted in Radley Engineering successfully achieving approval for weld procedures for Subsea drilling risers. Approval of its weld procedures has been granted by some of the largest exploration companies in the world. Greg explains: “We have now secured several subsea welding contracts for 2015. The tubes which are free issued to Radley Engineering by the pipe manufacturer are welded in a tightly monitored and controlled environment. The tube material grades are highly specified chrome martensitic, F22 and 4130, both manufactured to client’s specification and working to extremely high pressures on the seabed. Radley’s are the first company in Ireland to achieve this welding procedure approval. All weld procedures are completed by our highly qualified and experienced coded welders.”
Radley Engineering Ltd is committed to future investment in new equipment and machinery for the production of the units and hopes to expand its client base in the Oil & Gas market. Existing clients include Phillips 66 / ConocoPhillips, Shell, Statoil and Worley Parsons.
Welding Capabilities & Materials:
Radley Engineering Ltd is also one of Europe’s leading specialists in the welding of exotic materials. Its welders are fully trained certified specialist welders in various materials including:
- Stainless Steel (Austenitic)
- Carbon Steel
- Low temperature Carbon Steel
- Hastelloy alloy (C22 / C276)
- Aluminium
- Monel
- Duplex
- Super Austenitic Duplex
- Titanium (Grade 2)
- Incoloy
- Cupro Nickel
Design & Documentation:
Radley Engineering is the industry leader in computerised vessel design and modelling using both 2D and 3D applications including Auto Desk Product Design Suite (Inventor and Autocad), Autodesk Plant Design Suite, PV Elite and Finglow. This allows Radley’s to design vessels to ASME VIII, PD 5500, EN13445,API650 and TEMA standards. Radley operates a Quality Management System certified by the National Standards Authority of Ireland (NSAI) under ISO 9001:2008. Radley’s commitment to quality, inspection documentation and design standards ensure that client’s specification requirements are continuously met in full.
Special Architectural Projects:
Radley Engineering is proud to be associated with a number of high profile projects including ‘The Spire of Dublin’, ‘The Heron Tower’ in the heart of London and the Waterford City Suir Cable Stay Bridge. This is a clear indication as to the flexibility of its workforce and its design capabilities.
Greg concludes: “As the company looks to the future, we will continue to maintain our excellent relationships with the existing supply chain from client, EPCM and contractor in our current market sectors. We will forge ahead to develop new relationships within the subsea oil and gas markets as well as the UK nuclear power market where we are talking with EDF. This is an exciting time to be working at Radley Engineering Ltd and with the next generation of Radley’s, now in key positions within the company, the future looks bright.”
Radley Engineering Ltd