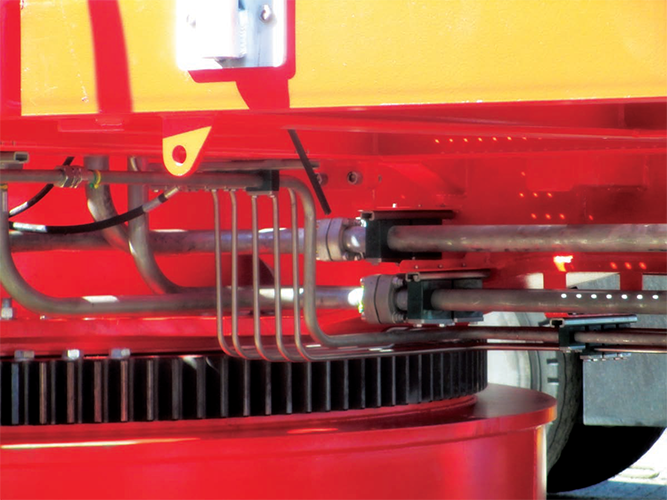
TME Hydraulics was founded in 1995 based in Ryton, Tyne & Wear.
Unstoppable force
TME Hydraulics was founded in 1995 based in Ryton, Tyne & Wear. The company’s unique mix of technical expertise and resources allows it to design, manufacture, test, install and maintain its customers’ hydraulic systems from the design concept through to spare parts and life time extension.
Today the business is focused on providing complete hydraulic services for customers in the offshore, marine and process industries. As an engineer led enterprise it undertakes bespoke design challenges in addition to regular service provision and system assembly.
Accredited to ISO 9001, TME holds a strong market position, recognised both for its quality and its strong health and safety policy and record. As part of the MKW Group the business has access to the facilities of its parent and sister companies, which enables TME to further extend its provision to include machining, fabrication and precision engineering. The MKW Group was established in 1976 and has maintained an across-the-board engineering capability that includes design, manufacture, testing, installation and maintenance, and project management.
In May 2014 the business became the UK authorised installer for the TM 37o Flare and retaining ring piping technologies from Tube-Mac. The contract is reflective of the growth of TME’s hydraulic installation capacity and brings a proven pipe coupling technology to the UK market, increasing the options for equipment builders, vessel owners and facility operators looking for secure, clean and cost effective pipe coupling systems. The benefits of non-welded technologies are significant, including the reduction in hot-work, weld procedure approvals and NDT costs. For hydraulic installations internal pipe cleanliness is of paramount importance and flushing of welded pipe to the desired ISO cleanliness level can be costly and time consuming. Using TM 37o-flared pipe with SAE flanges is a proven method of achieving clean secure connections with both time and cost benefits. Tube-Mac fittings are readily available in carbon steel and 316 stainless steel in metric and imperial sizes, and are suitable for use offshore with full material traceability.
The company recently made a large investment in a range of new equipment to support the growing hydraulic installation business. The recent purchases include a Parker EO2 Form F3 Work Station and programmable hydraulic pipe bending equipment, allowing TME to accurately form pipes up to 2″ on-site. Managing director Jerome Dardillac reported in July: “In purchasing new equipment the main consideration has been the ease at which equipment can be transported to site and set-up to be operationally ready at sites around the UK. With hydraulic pipe installation work scheduled in Aberdeen, Blyth and Darlington we need to deploy multiple teams fully equipped to each site. In addition to the equipment investment the business also organised training for technicians in Parker A-Lok products as part of our technician development programme.”
Specialising in 3D design and hydraulic calculations the company can manufacture modular and bespoke hydraulic power units, bespoke hydraulic test equipment, providing advanced manifold design, electrical control system design and ATEX certification. Systems can be assembled with a power range of 7.5kW to 500kW, with full testing at its facility. Utilising the skill base of its in-house design team, TME is able to successfully accommodate bespoke requirements and work with limited space envelopes. Each hydraulic system is assembled and tested within TME’s premises from where it maintains strict quality standards working within the constraints of project timelines.
The company’s workforce consists of experienced and skilled engineers specialising in bespoke manifold design with the ability to consolidate multiple valve stacks into a compact leak free manifold. Manifolds are designed using 3D CAD programmes, allowing interface connections to be easily checked and aligned, ensuring rapid and effective transfer from design to manufacture. TME sees the intelligent use of manifolds as a way to progress system designs and allow for further improvements in functionality within restricted space envelopes.
Not only does the business ensure that its own workforce remains at the forefront of the industry, hiring talented individuals additionally supported by continuous training, but furthermore it provides training for its customer base, working with in situ to provide detailed technical training in industrial hydraulics, which is delivered in a convenient manner via web casts and online learning to suit the compressed timetables of hydraulic professionals. Trainers are selected from an international pool of hydraulic engineers to ensure that teaching is relevant and specific to the subject and experience level of the trainees.
TME has carried out many industry high-profile projects including the installation and upgrade of the hydraulic control console for a ROV Launch and Recovery System in Rotterdam. The upgrade was to increase the functionality of the hydraulic control console using a console unit that was manufactured at TME’s Ryton workshop. This end-to-end project covered the scoping, installation, flushing and commissioning of the system and was completed safely and proficiently, on time.
Targeting expansion in Norway and subsea markets, TME attended the Underwater Technology Conference 2014 in Bergen, recognising the opportunity to reinforce contacts and discuss engineering capabilities for subsea applications. As a business with heavy involvement in the subsea sector from the design stage through to the service and refurbishment of established equipment it continues to seek new contracts to utilise its assembly capacity.
TME Hydraulics
Services: Complete hydraulic services for offshore, marine and process industries