To fully realize the element’s energy potential, we must solve hydrogen’s embrittlement problem.
Hydrogen has long been touted as the fuel of the future. It’s clean, abundant, and promises to revolutionize everything from transportation to energy production. But here’s the thing that a lot of people don’t realize: hydrogen is also a troublemaker. Through my work as a materials engineer, I’ve seen firsthand the complexities of this elusive element and have taken part in efforts to combat its more troublesome traits.
Hydrogen, at its most basic, is a single proton – a small, lightweight atom. It’s incredibly mobile, able to sneak its way into metals and cause all sorts of problems. It will mess with the structure of materials, particularly metals like steel and aluminum, leading to something called ‘hydrogen embrittlement.’
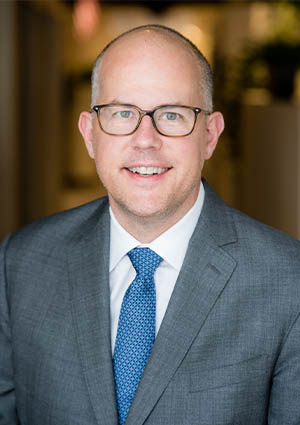
Hydrogen finds the weak spots – grain boundaries, precipitates, other little defects in the metal structure – and once it finds them, it settles in, weakening the bonds between atoms. When that happens, the metal becomes weaker, more prone to cracking and breaking. It’s the kind of thing that can turn a perfectly functioning pipeline, engine, or storage tank into a ticking time bomb. Before you know it, cracks start forming, and eventually, something breaks.
This is a major issue in the hydrogen industry right now, especially for companies building hydrogen-powered engines. For years, the approach has been to modify existing engines – those designed for gasoline or diesel – to run on hydrogen. But the materials in those engines – like cast iron or aluminum – were never built to handle hydrogen. In a cast iron engine block, for instance, hydrogen will find its way into the spaces between the iron and graphite, weakening that interface. Over time, this creates cracks that, under the pressure and heat of an engine, can lead to catastrophic failure.
But hydrogen embrittlement isn’t just a problem in engines. It’s a major headache when it comes to hydrogen storage and transportation, too. Think about hydrogen pipelines or storage tanks. These things are under extreme pressure – sometimes hundreds of times the atmospheric pressure. That pressure drives hydrogen into the metal walls of the pipeline or tank, where it can gradually weaken the material. And if you’re cycling that pressure – going from low to high, repeatedly – that just makes things worse. You’re essentially inviting hydrogen to penetrate deeper into the material, creating tiny cracks that can grow into big problems over time.
That doesn’t mean we need to throw out the existing materials and start from scratch. The solution lies in tweaking them. Take cast iron again. If you understand where hydrogen is going to cause the most trouble – those weak interfaces – then you can start thinking about ways to counteract it. One strategy is to add elements like tungsten to the mix. Tungsten, when added to steel, segregates to the grain boundaries and strengthens them, essentially providing a protective barrier against hydrogen’s effects.
This is where integrated computational materials engineering (ICME) comes into play. Using this kind of physics-based digital modeling shows us how materials behave across different scales – from the atomic level to the macro scale – and helps us predict how they’ll perform in real-world conditions. It’s not trial and error anymore. With ICME, you can simulate how hydrogen will interact with a material before you even make it, saving years of experimentation.
This is how QuesTek Innovations designed Ferrium M54 for the US Navy. Hydrogen embrittlement is a big concern for the jets that ride on aircraft carriers because of the salty, hydrogen-rich environments their landing gear operates in. We were able to see, computationally, where hydrogen would cause problems and design a solution that made the steel tougher and more resistant to embrittlement.
This is just one materials solution for hydrogen-hopeful industries. There are others. For instance, coatings can be developed that will block hydrogen from getting into the material in the first place. By coating the surface of a material with something that repels hydrogen or prevents it from dissociating into atoms, you’re already ahead of the game. Another strategy is to add ‘traps’ to the material – tiny features in the metal structure that capture hydrogen before it can reach those weak interfaces. These traps act like sponges, soaking up the hydrogen and keeping it from doing damage.
This is all to say that hydrogen embrittlement is a solvable problem. We’re not reinventing the wheel, but we are taking a deeper look at the materials we’ve been using for decades, figuring out where their weaknesses lie, and making them stronger. This is the kind of innovation that will make hydrogen a viable energy source for the future – not just in theory, but in practice.
By Jason Sebastian
Jason Sebastian is Executive Vice President of Market Operations at QuesTek Innovations LLC, a pioneering materials engineering firm that empowers innovators by resolving materials-based challenges. The company’s Materials by Design® technologies, including its groundbreaking ICMD® Materials Design and Engineering Platform, have enabled new products and new thresholds of performance across a wide range of industries, including aerospace, automotive, and energy.