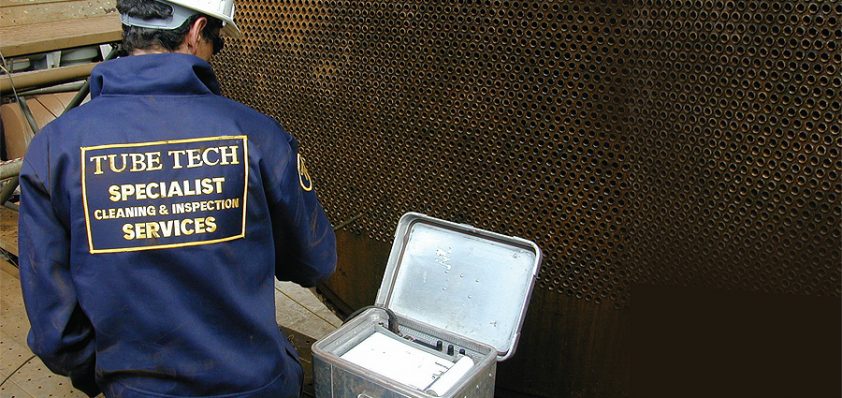
Tube Tech
A clean sweep
Tube Tech International was established with the aim of challenging the traditional stigmas attached to cleaning contractors, by providing innovative, market-leading cleaning services that meet the most demanding requirements of any industry sector throughout the world.
Today, the company is one of the most respected industrial cleaning businesses in the world, using state-of-the-art technology such as online cleaning, 3D graphics and virtual reality techniques, to solve the most challenging cleaning problems.
Mike Watson, Tube Tech’s managing director, elaborates: “I formed Tube Tech to find a niche in the market, with a view to challenging traditional opinions of cleaning contractors. As a result, the ethos of the company from day one was to substantially improve traditional processes. We always go out of our way to solve the most difficult problems worldwide, regardless of size, type of deposit, and industry.”
Mike elaborates on the importance of good information sharing between the client and contractor: “This means plans, photographic and even video details of plant dimensions, systems previously used and type of fouling characteristics expected. Once as much information as possible on the current problem has been gleaned from the client, a safe, effective and efficient cleaning approach can be instigated. The heat exchangers and pipe work that we clean are the arteries at the very heart of a refinery. This means that the refinery managers, and ultimately the shareholders, rely on them to be cleaned by a highly skilled professional with the competence to undertake the job.
“Refinery downtime can cost many millions of dollars per day, so it is vital that we can rely on our highly trained staff,” Mike continues. “Skilled operators with the correct knowledge and experience can reduce a ten-day job to five or less, or achieve 100 per cent cleanliness instead of the traditional 50 per cent. The importance of information sharing cannot be stressed enough, if a client tells us the heat exchangers have soft sludge and they are blocked with concrete-like deposits instead, they should not be surprised if the job takes longer or it can only be cleaned to 50 per cent. Likewise, if the tube sizes are incorrectly stated and the onsite utilities are inadequate, then the job cannot go to plan.”
Tube Tech’s emphasis on innovative, state-of-the-art R&D processes means that it leads the way in cleaning technology: “We have in-house R&D capabilities, which is relatively unheard of for a cleaning contractor,” says Mike. “For a company of our size we are truly committed to showing our clients that we can consistently introduce new and radical technology. For example, the majority of cleaning contractors in the world will have around five key cleaning systems, whereas we have 43 different technologies. The luxury that our clients have is that whatever their problem, we ensure we are aware of every cleaning product available, and what it can and cannot do.
“We operate unique 3D computer graphic design facilities, which help us illustrate to our clients our new cleaning ideas and processes to solve their particular problems,” he continues. “Additionally, we have a unique, world’s first virtual reality (VR) system, in which a client can visit our offices, put on a VR headset and gloves and interact with our cleaning technology. Clients can walk through the virtual cleaning system in a representation of their own heat exchanger or pipework to understand how it operates. This is particularly useful in dangerous jobs such as critical path upstream and downstream refinery shutdowns and even nuclear de-contamination projects, where high levels of contamination are involved.
“Following this initial process, if necessary we create a life-size, or scale replica of the tube, heat exchanger, furnace or pipeline at our facility, and then shoot video of our team using a mock-up of the cleaning system,” Mike says. “If the client has carbon or calcium scale in the tubes, we will replicate it with concrete or something harder, and then demonstrate how we will clean it. It is important that we go as far as we possibly can to develop a life-like scenario, which gives customers considerable confidence in their success when applied on site.”
Throughout its history, Tube Tech has continued to set industry standards for innovative cleaning methods: “We were one of the first companies to achieve online cleaning, which means that the client does not have to shut the refinery down at any stage,” Mike explains. “We were asked to complete a difficult cleaning job and we suggested that it could be undertaken online, which was believed to be impossible. After introducing the customer to the 3D animations, live mock-ups and video examples, we not only completed this extremely difficult task, but also reduced cleaning times from three days to one.
“Further to this, we are the only company to date that has ever cleaned a flare line at a refinery online,” he continues. “The flare line is the pipe through which most of the waste gases produced at the refinery pass, often reaching anything from several hundred metres to several kilometres in length. If it gets blocked or severely restricted, the whole refinery can come to a standstill. Usually, the cleaning of this pipe requires the whole plant to shut down, affecting production substantially and losing considerable amounts of money. We successfully cleaned the flare line online, whilst it was still running and occasionally flaring, which we believe is a world first.”
Continuing, Mike stresses the importance of health and safety in the company’s operations: “It is exceptionally important in every aspect of our work. We go overboard with safety, simply because in solving the most difficult problems, we operate in some of the most dangerous and demanding environments.
“Additionally, we are often asked to clean tubes, pipes and vessels containing very dangerous chemicals, such as hydrochloric, sulphuric and even hydrofluoric acids, which will erode metal,” Mike comments. “We often clean toxic chemicals, such as Mercury which, when cleaned with water jets, creates both an airborne and potentially harmful vapour, as well as an unwanted contaminated waste. To reduce the risks in these jobs we use remote-controlled and semi-automated equipment so that the operator is as far away from the spray as possible.
“We have also developed a method of cleaning that protects the environment,” says Mike. “On offshore oil rigs, the drill string pipes get blocked with mud that has low-level radioactive waste in it. Traditionally, they are cleaned with shot blasting or water jetting, which again creates secondary waste that is unfortunately washed out to sea. We have a system that will clean these drill pipes dry, eliminating dangerous water sprays and secondary waste.”
Mike looks to the future with considerable enthusiasm: “The current state of the cleaning industry has not moved on a great deal, so the potential for our developmental approach is huge. We aim to continue trying to convince refiners to improve lines of communication, archive plant information accurately and discuss methods to improve the accessibility and cleaning potential of refineries before construction. We also want to make them more aware of the importance of simultaneous cleaning and inspection procedures, as well as the introduction of groundbreaking technology. We have been growing by between 30 per cent and 50 per cent per annum in recent years and hope that our unique approach means we can continue to expand,” he concludes.
Tube Tech International Ltd.
www.tubetech.com