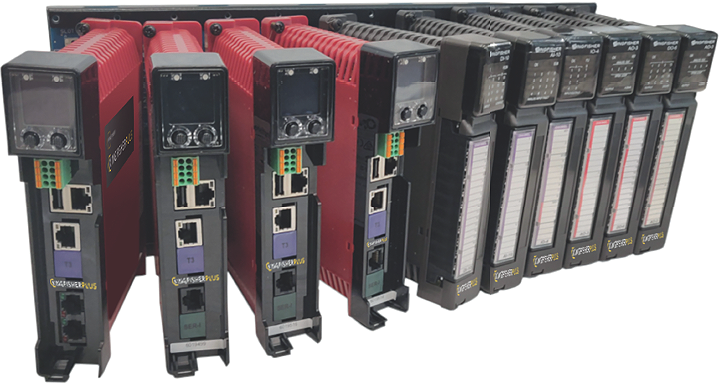
Under scrutiny
AS THE ENERGY INDUSTRY DIVERSIFIES – OFTEN BY CONNECTING SMALLER POWER GENERATION ASSETS TO THE MAIN GRID – A PROBLEM HAS ARISEN. TRADITIONAL REMOTE TELEMETRY UNITS (RTUS), USED TO MONITOR POINTS WHERE LARGE GENERATION PLANTS CONNECT WITH THE GRID, ARE OFTEN OVERSIZED FOR THESE SMALLER ASSETS. MATTHEW HAWKRIDGE LOOKS AT WHY SMALLER, MORE ECONOMICAL RTUS WILL BE ESSENTIAL FOR A DIVERSIFIED ENERGY MARKET
Diversification of the energy sector is a double-edged sword. On the one side, there is a huge benefit in the reduction in reliance on fossil and nuclear fuels as well as the creation of market opportunities for new investors and new consumers. On the negative side, many of the alternative energy sources – like Solar power plants and wind turbines – do not have the same level of control as traditional plants.
This requires precise monitoring and control at every interconnect to the grid, increasing the demands for data by the grid’s operational systems.
RTUs (Remote Telemetry Units) have long been used in the energy sector for managing power distribution. But, the economic impost of installing a large, traditional, power grid RTU, for system management, at every one of these small interconnects is a challenge for the industry. Smaller RTUs can meet this challenge.
What impact have renewable power generation plants had on existing systems?
Wind, solar, hydro, biomass and wave solutions for power generation have all added significant sources to traditional networks in recent years. Renewable energy now produces a growing proportion of most developed countries’ total energy output – recently exceeding 20 per cent for the first time in the UK.
Compared to large coal, gas and nuclear plants – where a single point of entry to the system carries the bulk of supply – operators now need to manage a much wider portfolio of assets, with much smaller demands at each location. This has resulted in a need for smaller RTUs.
Why is there growing demand for smaller, smarter RTUs?
A typical power station is around one Gigawatt (1GW). The RTUs to monitor the connections between these facilities and the power grid are not suitable for the vast range of smaller, renewable options – such as solar, biomass and wind – where supply power is measured in kilowatts. At these smaller-sized power connections to the network, the asset monitoring and control RTUs used for a full-scale power distribution would be overkill.
Operators require smaller, but still capable, RTU solutions that have been proven in power monitoring and control in parallel markets. We’ve seen growing demand for our RTUs which can be cost-effectively deployed, but still provide operators with the data they need.
TBox RTUs, for example, have been used for decades to monitor power consumption at critical assets. RTUs allow telecommunications operators to monitor the incoming supply from the main grid and any local backup generation or backup storage at their facilities. In the event of a grid failure, RTUs help them decide what actions need to be taken to ensure continued operations of the critical telecommunications network.
Using an RTU in the renewable sector
Our TBox RTUs are being used on wind turbine towers in Greece, monitoring production, rather than consumption, at each tower. These kinds of RTUs, even with a small footprint, have enough capacity to manage the limited number of I/O points that are required at each power generation tower — which Ovarro has found with a number of its customers.
The TBox has also been used on 30MW solar power plants in France and on grid connected Solar Arrays in Australia, producing as little as 250kW. These interconnects are much smaller than the gigawatt connections of a large power plant, but still require localized monitoring and often, control. The small TBox RTU is well suited to these applications.
Is monitoring smaller power plants less complex?
Not necessarily. In fact, while power management may be less complex, smaller power plants can have a more complex set of communication demands than traditional plants. Small sites are often independently owned and managed and must share data with numerous stakeholders. The ability of an RTU to collect data from numerous sources and distribute information to numerous stakeholders is a key advantage when compared to other process controllers.
What is the RTU responsible for on-site?
At small sites, the RTU is both the site controller and the site communications gateway. The RTU collects data directly, and can also provide a secure VPN, to other devices that may be operating on site, such as, programmable logic controllers (PLCs) managing solar panel tilt and azimuth control, weather stations and digitally networked power relays. The collected data is then made available to the grid operators who can issue commands back to the RTU to regulate the station. In parallel, the RTU relays key information to the asset owner or investor and to maintenance crews.
In Australia, data is also sent in parallel to cloud based data servers for local communities and schools, for educational purposes. With its ability to report alarms and historical data via email, SMS, FTP and MQTT, a TBox is the ideal choice for small power plants that need to manage both physical assets and wider communications demands.
Can RTUs be used with ‘non-grid’ power networks?
Yes, large facilities such as hospitals, universities, airports and railway lines often have their own internal power network that needs management. They have the same control and communications requirements as the main grid, at marginally less complexity.
Electrified railway networks, too, source their main supply from the grid and then distribute the power along the railway network. The demands on RTUs used in the Railway Network have many similarities to a Power Network RTU – they are exposed to remote environments, occasional voltage spikes and must be able to store, manage and report large volumes of data and above all else, control the local switchgear.
Are smaller RTUs resilient to the network environment?
Yes, an important feature with any RTU is resilience to the site environment. Ovarro RTUs can operate in these rugged conditions at temperatures between -40 and +85 degrees Celsius and have up to 5,000 volts of isolation on I/O cards to protect the CPU from spurious electrical events.
In addition to being resilient to the environment, RTU systems should have layers of redundancy so it can continue to operate even if a major event damages one piece of the system. The Kingfisher RTU for example, can be configured with fully redundant Power Supplies, CPUs, and multiple communication paths. It means they can continue to manage intensive SCADA and telemetry applications, even in the event of a partial system failure.
What if the power generator fails?
RTUs have always operated in areas where power is either unreliable or unavailable. Each Ovarro RTU draws only a few Watts and can easily run off a solar power system or even a small and insignificant feed from the site generator. The RTUs also incorporate a battery management system and can run off a small rechargeable battery for extended periods. This removes the need for a UPS for the RTU. In addition, Kingfisher RTUs support multiple power supplies so that parallel connections to AC and DC supply systems can be used to diversify supply and minimize the risk of total failure.
How will RTUs evolve in the future?
For many years there has been an ongoing trend in increasing the volume of data collected from the field. This centralized data collection and analysis are vital for long term trend identification and planning, however, a localized response is still required for low latency control. If you need a field hardened PC, or ‘edge computer’ for monitoring electrical current, temperature, emissions, power and asset health, then you need an RTU.
RTUs are specifically designed to perform local control and in parallel, gather and relay information to SCADA or the cloud where it can be analyzed and trended, providing operators with the information they need for efficiency management and asset management in addition to real-time control.
MATTHEW HAWKRIDGE
Matthew Hawkridge is Chief Technology Officer at Ovarro. Ovarro is the new name for Servelec Technologies and Primayer. Ovarro’s technology is used throughout the world to monitor, control and manage critical and national infrastructure. Its connected technology is always there, always on. Secure, proven, trusted; integrating seamlessly with clients’ assets. Collecting and communicating data from some of the most remote locations and harshest environments on the planet. Enabling businesses to work smarter and more effectively. Ovarro works with customers across water, oil & gas, broadcast and transportation to help monitor, control and manage their assets.