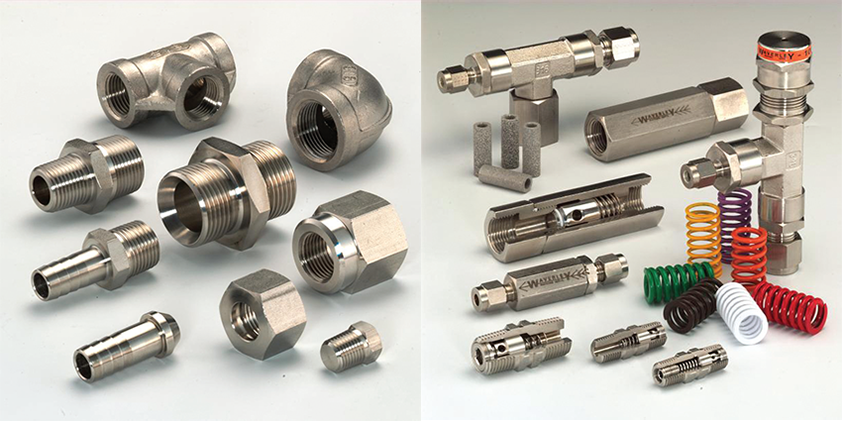
Waverley Brownall
Confident delivery
Waverley was first established back in 1929 as an automobile manufacturer and has developed over the years to become a leading manufacturer and global distributor of a range of 316 stainless steel and exotic material compression fittings, valves and bespoke instrumentation products.
Waverley Brownall in its modern format came about following the acquisition of Brownall from the Delta group in 1999 by Tatem Industries. This led to the eventual buy out of the company by group member, Waverley Components and Products. Ever since it became Waverley Brownall, the company’s philosophy has been governed first and foremost by the quality of the products it designs and manufactures, and the customer services it provides.
The business has built upon its reputation for quality by supplying some of the largest industrial companies in the world with its high quality and reliable products. The company’s many accreditations include ISO 9001, Lloyds type approval and TUV accreditation among others, and together with the approvals of many of the major oil and gas companies, Waverley Brownall has a strong reputation for quality in all it does. Adding to this, the company’s sales director, Nick Douse, describes the company’s main strengths: “Our watchwords are service, supply, quality and flexibility and those are the four areas we work on improving all the time. If a client has a short lead-time or needs early delivery we can accommodate them by re-prioritising our in-house production faculties.
“We work predominately on an exstock basis with exstock delivery through out the UK and Europe to keep our customers stock to a minimum. Our people are also a huge asset to the company. We have excellent sales staff who are efficient and knowledgeable, as well as production staff who are experienced working with high tech machinery. Finally, our innovative design and development team drive through new products and materials, helping us to expand our product range. We manufacture 100 per cent of our parts in the UK and stock this in one location. Additionally we endeavour to keep 95 per cent of our catalogue items in stock. Our longest lead time for in house produced parts is three weeks.”
Within its vast product offering, the company supplies a wide range of fluid and gas system control products predominantly used for instrumentation applications in specified and non-specified markets in the fields of alternative fuels, pharmaceutical, petrochemical, food and drink, oil and gas, power, and the semiconductor industry. Waverley also provides the majority of instrumentation fittings and control valves to the gas distribution network in the UK (National Grid). Additionally the company is specified on many oil and gas installations from the Britannia platform in the North Sea to the Mossgas Platform in South Africa.
Looking at recent developments, Nick describes the company’s move to offices in Essex: “One of the most significant improvements was when we decided to bring all the parts of the business (sales, production and stock) under one roof in our current location in Essex. In 2006 we also changed our production focus from cumbersome multi-spindle machines to twin spindle 7 axis machines, which are more flexible and enable rapid product set up and turnaround, as well as enabling finished components to come off the machine.”
These changes have brought significant improvements to Waverley’s clients as its response and delivery times have been rapidly decreased, while quality has been increased significantly. “The confidence in our ability to deliver has encouraged many clients to stop carrying stock all together and rely entirely upon us for on time delivery,” Nick continues. “This gives us significant advantages in niche markets when compared to our competitors, which are largely US-based multinationals. Due to our flexibility and willingness to tackle difficult materials and short lead times, we have been able to overcome our competition. These company structural changes also led to one of our proudest awards: the Excellent Supplier Performance award from ConocoPhillips for the Britannia Satellites Project. Since then we’ve increased production and sales and business is certainly improving since the move around.”
In terms of the future, Waverley will continue developing new products to expand its range. Nick comments: “Moving forwards we will focus on the introduction of exotic alloys materials of high corrosion resistance into our product portfolio. This is because we feel the niche market these fall into will fit our production flexibility well, and coupled with short delivery demands that our clients expect, we are able to provide a strong service in this area.”
Waverley Brownall
Services: Instrumentation products