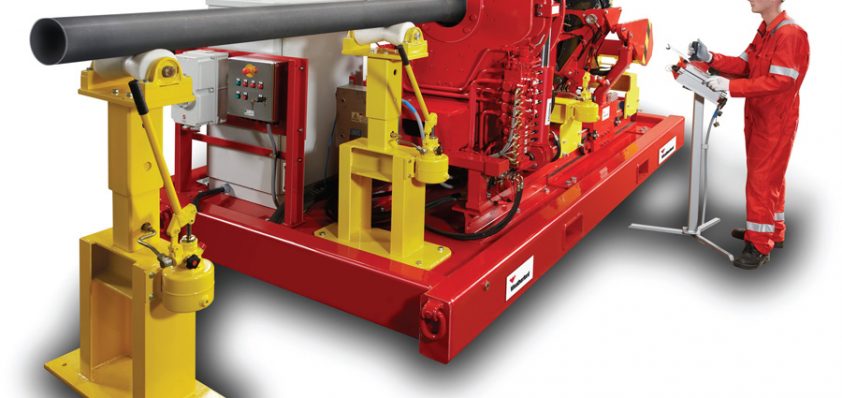
Weatherford Oil Tool GmbH
Tooled for success
As part of the Weatherford group of companies, Weatherford Oil Tool GmbH provides high-tech equipment for major projects in the oil and gas sector.
Based in Langenhagen, Germany, the company employs over 200 people, and is famed for its innovative and pioneering designs. As a consequence, it has made a significant contribution to the group having recently achieved a turnover of $6.1 billion.
Weatherford serves all of the key players within the oil and gas industry. Most often, however, the manufacturing plant at Langenhagen performs its business internally, and is charged with supplying its more than 170 sister entities around the world. These, in turn, utilise the company’s products to provide services to clients in the broad areas of drilling, evaluation, completion, production, and intervention.
“Our key strength is the will we have to create the best technology,” says Uwe Trampenau, technical services / technical sales manager at Weatherford Oil Tool GmbH. “Our branch of the company was founded in 1959, and so we possess nearly five decades of experience in designing equipment. We are manufacturing customertailored products, and always pay the utmost attention to safety in our work. Furthermore, all of the equipment that we manufacture is checked and inspected according to proven schedules before leaving the plant, and our testing yard even includes a rig structure to simulate realistic on-site conditions during this phase.
“As part of our emphasis on quality, we have, for several years, implemented the Enterprise Excellence Process (EEP). The objective of this is to achieve total client satisfaction, and so we have created teams to focus on process improvement in areas such as delivery times, R&D project length, and improved quality of vendor parts. We do this without ever losing sight of our fundamental responsibility for the well-being of personnel, assets, and the environment.”
Weatherford’s facility in Langenhagen, Germany, in close co-operation with the US technology centre, is responsible for several of the major innovations in the company’s range. For example, as part of the unit’s focus on rig mechanisation, it has developed a technically sophisticated OverDrive™ system, designed to provide a safer and more efficient alternative to conventional casing installation. Mounted to the rig’s top drive is the TorkDrive™ tool, which combines several casing-running applications into one: power tong, elevator, fill-up tool, and weight compensator.
Uwe explains that the company has continued to make significant breakthroughs in this area: “We have finished the development of the third generation of TorkDrive systems, called TorkDrive™ Compact. We revealed the prototypes for these earlier this year, and received a lot of attention because they were acknowledged as a major improvement within the oilfield service industry.”
The TorkDrive™ Compact offers numerous advantages to its users. The tool possesses the flexibility to run a wide range of casing sizes, boasts a design that allows for high-volume circulation during running and drilling, and includes a mode that permits venting of compressed air during casing fill-up operations. Furthermore, the tool can be quickly positioned over successive joints, and multiple safety interlocks enhance both efficiency and safety.
“We showcased this new design at the OTC in Houston earlier this year,” says Uwe. “ONS 2008 will provide a further opportunity to demonstrate the work that we have been doing. These events are always a great opportunity for revealing the latest developments in our product lines to any potential customers. In addition, we always like to be in close contact with our clients, and events such as ONS allow for detailed discussions.
“We understand that there are many companies out there who attempt to use our ideas and advancements to benefit from our success. By focusing very carefully on customer relations, however, we become aware of industry needs and general market trends at a very early stage. This is important to our R&D, in which we invest substantially, and it ensures that we remain one step ahead of our competitors.”
In recent years, the company’s devotion to research has been responsible for many leading products within the oilfield services industry. Notable amongst these is the Riser-Tong 21-300, which is well distinguished the world’s strongest hydraulic makeup tong. The demand for this new design came from a client in the Asia-Pacific area, as part of a deepwater development project, West Seno, which was being conducted from two small tension leg-platforms with a tenderassisted drilling rig. The connectors for the joints on the risers that were being installed required 125,000 ft-lbs of makeup torque, and 225,000 ftlbs of breakout torque.
Weatherford’s Riser-Tong 21-300, distinct from any previous design, was the first to be capable of generating 300,000 ft-lbs of both makeup and breakout torque. Deploying two of these units, West Seno was completed successfully, with no complications, and this trend has continued in subsequent projects. From a financial perspective, the tong has provided clients the benefits of reducing the number of personnel needed on the rig floor, whilst greatly enhancing operational efficiency and safety.
Uwe explains that, despite its success, Weatherford is not short of challenges, and he highlights one issue in particular that the company is currently working to address: “We are confronting a shortage of raw materials on the market, and this can sometimes lead to slight delays in delivery. This is frustrating, because it is our objective to satisfy all requests that we receive from clients in good time, and with the best quality. We are working to deal with this threat by strengthening our material flow processes and logistics.”
This unerring desire to provide complete customer satisfaction has led Weatherford to the forefront of the sector, and Uwe is optimistic that the company can maintain its leading position: “The market has reached an absolute high, and we must continue in our plans for further growth. For example, we are presently building an additional production site here in Germany, and are considering even more. We expect to continue to develop high-end products, and therefore to be responsible for reducing process time and increasing safety for our customers. Indeed, we believe that our superior designs should ensure that we will be largely unaffected should there be any long-term slowing in the market.”
Weatherford Oil Tool GmbH
Products Oilfield services equipment