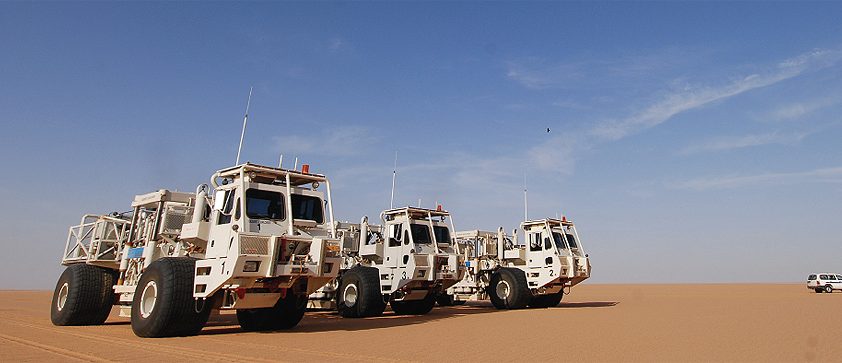
Wintershall Holding AG
Tradition of excellence
Wintershall Holding AG has been involved in the exploration and production of crude oil and natural gas for over 75 years.
Its work has taken the company around the world and today it operates across Europe, North Africa and South America, as well as in Russia and the Caspian Sea. The company was founded in 1894 in Germany, by the industrialist Heinrich Grimberg, and drilling contractor, Carl Julius Winter. Its original focus was as a drilling company, mining for potash. Following an accidental oil leak into one of the potash mining shafts in 1930, the company added crude oil production as a further business segment.
Wintershall today operates globally in selected core regions but has its strongest roots in the European market. The business continues to explore and produce oil and gas in its original market of the German mainland. It expanded into the neighbouring Dutch sector in 1965, carrying out further exploration and production work. As natural gas from the North Sea will continue to make a significant contribution to Europe’s energy supply, Wintershall has acquired not only new exploration rights in the German and Dutch sectors of the North Sea, but also promising licenses in British, Danish, and Norwegian waters, in order to drive the specific expansion of its activities.
Wintershall’s Dutch subsidiary, Wintershall Noordzee is based in Rijswijk. Beginning its activities in the Netherlands as partner to Pennzoil, it was one of the first exploration companies of its kind in the region. After assuming the operatorship in 1988, Wintershall Noordzee has expanded over the years while still concentrating on its core region of the southern North Sea, where the company has been active since 1965. The company is today one of the largest producers of natural gas in the Netherlands, it hosts 25 offshore platforms off which nine manned installations and one onshore processing site. Following the successful acquisition of Clyde Netherlands B.V in 2002, the company has been able to increase its production and its reserves of natural gas. The acquisition also enabled the company to extend its company-wide competence centre for offshore technology.
Gilbert van den Brink, managing director of Wintershall Noordzee, talks about the company’s strengths: “Our main advantage over our competitors is the range of work that we offer, much of which can be carried out or at least initiated in-house. We manage our own exploration department, so we are competitive in that respect, and we can follow up the project after exploration. This covers all the development and engineering, as well as initial construction engineering work. We also keep core people within our business, and as exploration is crucial to us, this includes a large exploration team that has been quite successful. Beyond this we sub-contract a lot of our drilling and seismic work. By retaining key personnel at Wintershall, we always have the vital core knowledge within the business.”
Another key area for the company is the meeting of environmental guidelines. Wintershall takes the ecological impact of its work in the North Sea very seriously, and aims to minimise the effects of its projects on the area. The company has achieved this through its refurbishment work on several platforms. Gilbert outlines the most recent of these: “We are presently undertaking the E18 project, with the help of a large number of sub-contracting personnel. The work takes place at the E18 field in the North Sea, and involves an old P14-A platform, which was taken to shore for refurbishment to create the new E18-A unit. The platform must be able to work with existing wells in the region, in this way we must incorporate drilling technology for abandonment of existing wells in the P14 block and with lifting and moving of the platform, making it a very complicated project. It was successfully carried out without major incidents and within budget.”
The P14-A gas production platform was dismantled from its location in the Dutch North Sea, taken apart and transported to shipyards in Rotterdam, Ridderkerk and Vlissingen. The topside of the platform was stripped and refitted with accommodation and process facilities, now to be re-used in the E18 block, which will begin operations mid 2009 in the North Sea.
“We are also currently working on the P9AB project,” Gilbert continues. “This involves the first real subsea well tie-ins according to the Daisy concept, meaning we link up the flowlines between the two wellheads. This is a different technology for us once more, and we are supported by strong partners to undertake the task.”
One of the partners that Gilbert mentions is Tideway Offshore Contractors, a leading offshore business specialising in dredging and rock placement. Tideway was ideal for this project as the P9 8” gas pipeline had to be installed along a route characterised by the famous Southern North Sea sandwaves. In order for Technip to lay and trench the pipeline, Tideway was asked to remove the sandwaves with its D.P. trailing suction hopper dredger, ‘Pearl River’, prior to pipelay. Due to the size of the vessel, the works were executed in late winter without major weather downtime.
After installation of the P9 gas pipeline, Tideway Offshore Contractors returned to the site with its two D.P. fallpipe rockdumping vessels, ‘Seahorse’ and ‘Rollingstone’, to protect pipeline crossings and structures from scouring. Furthermore, rock protection layers were installed along the route to increase weight on the pipeline and to minimise the risk of pipeline upheaval buckling. This is just one example of how Wintershall is able to work successfully with partners throughout the industry in a range of projects and market sectors.
In 2005, the company installed and commissioned, what was at the time, the largest Wintershall production platform in the North Sea, the F16-A. It is located within the southern sector of the North Sea, Wintershall Noordzee’s predominant region of operation. The natural gas platform is capable of processing up to six million cubic meters of natural gas per day. This is enough capacity to absorb the volumes of field E18-A, which was discovered in 2007 in close proximity to the platform.
The F16 is Wintershall’s largest North Sea production platform, standing at 27m high, incorporating seven levels and weighing 3,600 tonnes. Within the F16, the natural gas is air-cooled and dehydrated in facilities onboard the unit. In this state, it is then piped to Ouden-Staten Zijl, in the province of Groningen, via a pipeline and from there it is fed into the network of the Dutch firm GTS. Like its sister platforms in the North Sea, the F16 is capable of operating completely independently. The six-man crew, plus cook and steward, who work on the platform, can produce their own drinking water using a seawater desalination system. There is also a mini power station, which produces electricity from gas extracted from the field.
The F16 installation was followed by the full-scale conversion and complete modernisation of the L5-C gas production platform in 2006, which allowed the company to effectively meet environmental and economic targets. Previously, the platform has been used for production in block K10bc in the Dutch sector of the North Sea. The refurbishment of the old platform, which spanned ten months, saved costs and time over the construction of a new platform, because much of the original material was reused.
Another recent innovation is the newly constructed centre for remote controlled operations (RCO) at Den Helder. Ever since 2007, there has been a radio control system operating from Den Helder, which monitors the production operations of 18 of the offshore platforms that Wintershall operates in the southern sector of the North Sea. This will ensure that production from the Dutch offshore reserves is efficient in the future. Converting to RCO operation has meant that Wintershall can achieve significant savings in areas such as material procurement, maintenance, preparation work, personnel deployment planning, and logistics, which also makes the development of smaller deposits financially viable. Additionally, the number of flights to the respective platforms can be reduced, thus effectively increasing employee safety.
“The centre is unique,” Gilbert elaborates. “It carries out monitoring services at offshore platforms. From the production control centre (PCC), we basically take charge of a number of functionalities in terms of production, and production volume, as well as alarm management. This involves managing the various alarms that we receive and responding accordingly. We are then able to directly contact the platform and inform and instruct the operators working outside, rather than in the control room.
“The remote control facility also enables us to collect centralised data from all our processes, which can then be analysed. This generally allows for a much closer analysis of the whole process and whenever it begins to deviate from the desired settings, or perform below expectation, then our detailed study can assess why this has happened, if it is the well itself or our process that is responsible, and then we can investigate how to prevent it in the future. The whole system allows us to interact more fully with our platform, and this can happen a lot quicker as well, meaning that ultimately we can optimise our production by being more accurate in our prediction and meeting the targets.”
The Netherlands is also home to the corporate-wide Wintershall competence centre for offshore technology. The expansion of offshore expertise is generally gaining importance in oil and gas exploration and production, and with the support of the new centre, Wintershall is able to apply its enhanced expertise in activities in other regions of the world.
Gilbert elaborates further on quality issues: “We have our own HSE department, which employs around ten people. This team develops work programmes for the business on a yearly basis, taking into account exactly what is required to meet health, safety and environmental targets and attain the quality standards that we set out to achieve. As a company we then aim to comply with the requirements outlined. Our approach is to look not only at what has happened in the past to see what we can learn for the future, but we are also trying to anticipate what the new legislative requirements will be. In this way we are assessing what we see as being necessary to remain a prudent operator.”
As the industry moves through the current financial hardship, Gilbert still anticipates opportunities for Wintershall’s growth within the market: “The industry activity has subsided a little bit in recent times and I am conscious that it is becoming much more difficult for many companies to gain access to the funds required for their projects, due to the recession. However, we are a fairly large operator in the Netherlands, ranked fairly highly in terms of size and so we generate a lot of cash, and we are able to use these funds on a variety of projects. The constraints that we are experiencing are on the chemical side of the business, which is struggling much more than the oil and gas market. As part of the BASF group we are suffering with the downturn, although we are by no means in a critical situation as BASF is performing well compared to its other peers in the chemical industry. Wintershall, as a whole, is a good cash generator for the BASF group, so we are confident about the future.”
The company’s own future development will continue its current prolific presence in the market, as Gilbert explains: “We feel that we have a firm foothold in our industries. We are still trying to develop at least one or two projects on a yearly basis to ensure that we maintain our market presence and strong reputation. We are continuously looking at new development opportunities in a rather mature area, which makes it a little more difficult to work at. Having said that we did make several new discoveries over the last year, which will result in substantial amount of work in the years to come. Beyond this, we aim to continue to optimise technologies that we have developed within the business, so for instance the remote control aspect that I outlined earlier will definitely be further expanded on, as we are very excited about the possibilities of this system.
“One of our main drivers in the future is to remain one of the low cost operators, because, although we are already a fairly sizeable company in the Netherlands, we want to continue to be the preferred operator of choice productionfor our partners. This depends of course on how the partners that actually work with us in the Netherlands perceive us. We will continuously have to prove that we are worthy to be their operator of choice. So in the immediate future, we will focus on streamlining our operations to offer the most efficient and cost effective service to our partners and shareholders. For the moment we are doing well, so I foresee that we will retain our presence in the industry for many years to come.”