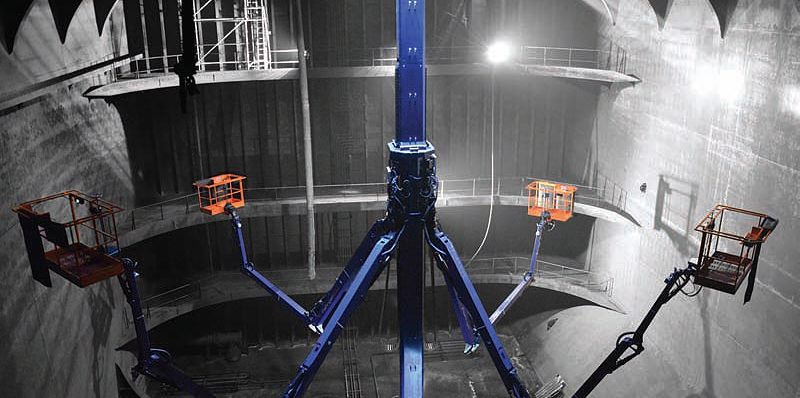
Palfinger Systems GmbH
Evolution by revolution
The globally active manufacturer provides access and maintenance solutions for both the offshore and shipping industries, calling upon its strengths in offering flexible standardised solutions, as well as customised applications through to the highest level.
The business was founded in 1992 focusing on the construction of marine cranes, and in 2000 established a department focused exclusively on the development and manufacture of innovative access and maintenance solutions.
“In that period as a development department we assessed how the industry reacted to maintenance needs, accessing difficult areas on both ships and jack-up rigs. Realising the cost and time implications in the use of scaffolding and a large number of operators we began designing a system which would eliminate this,” says Thomas Hinterseer, managing director. Creating solutions that solve major problems that occur on platforms and ships is the fundamental ambition of the business. Palfinger Systems access solutions increase the safety of repair and maintenance work dramatically, with work platforms and baskets providing safe access in suitable working positions. As a result, handling is much safer and easier compared to climbing and scaffolding systems.
“Essentially we were going in with the goal of changing the industry, with fewer people, a higher level of automation and having a smaller impact on the environment, all of which benefit the end user, speeding up the time that the ship or jack-up is in the harbour or yard,” points out Thomas. By listening to the customers, analysing the market and designing prototypes the business developed the ideal solution to carrying out the work. At the same time as developing these new technologies, the business introduced a new water blasting system, eliminating the need to use grit-blasting services, leading the way as the industry looks to greener solutions. “We are a corporate, socially responsible organisation and therefore protection of the environment is high on our agenda and an aspect that we aim to drive forward,” he adds.
The focus in the development of the access solution was to design a system for a quick and easy installation. In the offshore industry today it is not possible to reach some locations without special training, such as using industrial climbers. The new access method for Palfinger Systems offers major advantages with all areas brought into reach of platforms and baskets, which means that checks can be effectively carried out at heights. “The initial prototype we developed was for the offshore jack-up segment, called the jack-up maintenance platform (JUMP). We tested the first model in 2009, making more improvements, enhancements and revisions before receiving full approval from the licensing authorities and launching the development to market in 2013. We have now received our first orders,” says Thomas.
The JUMP solution offers safe, reliable and efficient access to the leg, and is designed to allow inspection and maintenance works such as blasting, painting and steel work repairs. The unit is driven by an onboard diesel powered HPU, requiring no external power source, with the configurations including telescopic cranes, aerial platforms, supply and rescue platforms, full enclosure and ancillary power for use with options such as hand tools or lighting. Inspection and maintenance on the legs of jack-up rigs is necessary at regular intervals for both maintenance and class requirements. Conventionally, scaffold towers are erected and rope access teams utilised, which requires a lot of effort, workforce, time and money. The JUMP concept considerably mimimises this outlay.
The market place for jack-up rigs repair and maintenance has been extremely active over the past few months, and despite the general slight depression in shipping, inspection, maintenance and repair remains active. “Our customers, the ship and rig owners are looking towards optimising cost and reducing time out of service,” says Thomas. The traditional method of installing and removing a scaffold to service the rig or ship can take up to three weeks and involves a high number of personnel. The Palfinger Systems solution not only reduces the set up time to just 24 hours but also eliminates the number of operatives working, particularly at height therefore eliminating the safety risks.
“One of the biggest challenges we face is that the oil and gas and shipping industries are very traditional businesses, so changing the mindset through the introduction of new automated equipment has, in certain areas, been met with natural resistance to change. Automated systems ultimately result in a lesser requirement for personnel and questions have also been raised as to just how much safer and faster the system can be. Some have questioned whether water blasting is really better than grit blasting, providing the same quality, as well as questioning automatic painting and how a robot can do as good a job as an experienced operative. These are all natural questions that arise when introducing an alternative to an existing business model. There can be a fear of the unknown and modernisation, with the industry comfortable in past systems and methods,” explains Thomas.
The second major product development made by the business has been the introduction of the automatic HTC system, which is currently on the final testing and commissioning phase at the Jurong Shipyard in Singapore. The HTC is the world’s first environmentally friendly and cost-optimised automated hull treatment system for the coating/de-coating of spots or complete hulls, and also improving shipowners’ fuel consumption. “Singapore has very stringent obligations on its environmental footprint, and is also driven to reducing the amount of unskilled labour. Holding a strong image as an innovative technology leader the Singapore Government has been supportive of our systems and approach to maintaining and painting ships. This has been a great support in the credibility of our system,” Thomas highlights.
The product will be officially launched at OSEA 2014 in Singapore in December. Commenting on the drive behind the company’s involvement in such trade shows, Thomas says: “It has always been important for our company to be a part of the largest exhibitions, to meet and discuss projects with our existing clients and other members in the offshore area, including establishing new contacts with visitors from all over the world. This year we have been targeting exhibitions much more aggressively, attending five trade shows in 2014, and will be present at OTC 2015. We have the first reference projects now, with very satisfied customers and it puts us in a very good position to convince businesses with a more traditional approach that this is the future for the industry.”
Another ship access solution is the ITP8 (Internal Tank Platform). The treatment of the internal areas of tanks and cargo holds on marine vessels, especially tankers, is difficult and labour intensive. Scaffolding is required to reach thousands of square meters of walls and roofs, however, providing access with scaffolding is costly and time consuming. In some cases, the use of cherry pickers is possible. Nevertheless, requirements like big openings and plane surfaces restrict the use of this equipment drastically. Further disadvantages like exhaust pollution or high loss ratio make a successful application even more difficult. The ITP-8 is thus equipped with four two-man baskets. Additionally, the ITP-8 is height-adjustable and can either be placed on the floor where it can be freely positioned or suspended from the tank opening. A very good range is thus available from the company. The ITP-8 can also be used to work on the hull of a ship or a tank, meaning that a wide range of different applications is thus possible.
Focused on contributing to the sustainability of the regions in which it operates, Palfinger Systems recruits and supports the education of a local workforce. “Although we need less personnel than traditional operations we do require people of a certain skill set, and for the industry, automation is the way forward, certainly in European shipyards and Western Shipyards,” says Thomas. Because labour is so expensive, automation can make shipyards more competitive and sustainable. Reviewing the market place he adds: “The US holds great opportunities for the future and we can help shipyards that are struggling to solidify and move systems forward on a healthier basis reducing costs and lay up time.
“In Asia, although there is relatively low cost labour systems available, there is a strong future for these systems. Penetrating the markets of Korea, Singapore and China, which is the biggest shipbuilder in the world in terms of tonnage, offers an interesting future. Brazil, Africa and the Middle East, are new and developing regions and the ability to build a sustainable business with a localised shipyard in those regions using some automated systems, will provide quality, safety and speed. We expect there to be some good opportunities around the corner in Africa and the Middle East with high growth rates, which is very appealing to us.”
As Palfinger Systems moves into a very active future Thomas concludes: “We are continuing our drive to introduce our products into the broader market, demonstrating our systems for both rig and shipping businesses. Through the aim of proving our systems are viable solutions to their needs we expect to become the prime supplier for all maintenance, inspection and repairs works for ship and jack-up owners. In the future we will look to expand our product range, entering new markets such as the semi-submersible and drill-ship business. The system and approach that we are taking towards automation, lower environmental impact and speed is completely transferable to a number of other assets and markets.”
Palfinger Systems GmbH
Services: Manufacturer of access and maintenance solutions for offshore and ship industries